AlSiC-brick (ASC brick ) is a commonly used refractory material for thermal equipment in the pretreatment stage of molten iron. Especially in molten iron, its usage rate is very high. ASC bricks have very good high-temperature properties and resistance to oxidation, spalling, and slag erosion. They can withstand long-term high-temperature solution erosion and have a long service life. AI203-SiC-C bricks are mainly composed of the following materials. The combination of various materials together forms the excellent performance of ASC bricks.
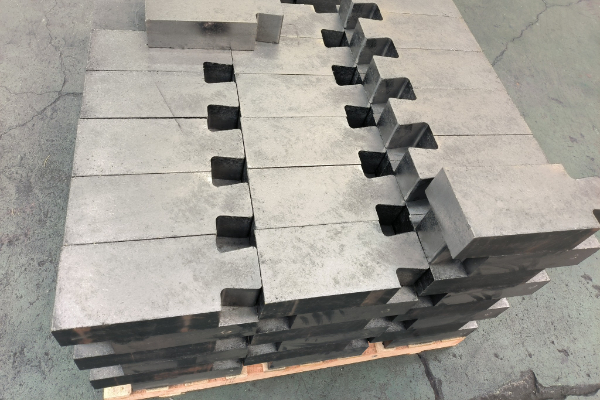
What is the raw material composition of AlSiC-brick?
AI203 raw materials
AlSiC-brick refractory materials have excellent performance, which is reflected in their resistance to chemical erosion by molten iron and slag and their ability to withstand the erosion and erosion of molten iron and slag. For tap trough injection materials, from the perspective of corrosion resistance, there are AI203, MgO series, and MgO-AI203 series. However, within the temperature range of molten iron containing 4.5% carbon and the temperature does not exceed 1500°C, the durability of the AI203 series Enough. Mainly include dense fused corundum, fused white corundum, brown corundum, tabular corundum, sub-white corundum, etc. When AI203 series raw materials are used as aggregate castables, the degree of deformation caused by repeated heating and cooling for a long time is lighter than other systems, and the expansion rate of the AI203 series is small, so the thermal stress generated on one side of the working surface is small when used. Regarding the role of AI203, it is generally believed that AI203 is an oxide with strong corrosion resistance to Na2C03, Fe, P, etc. However, pure AI203 has a large expansion coefficient, and poor peeling resistance, and the matrix part is easily damaged by clear melting. , causing the aggregate to peel off and cause melting loss. Therefore, pure AI203 refractory material cannot meet the requirements of trench material and molten iron pretreatment.
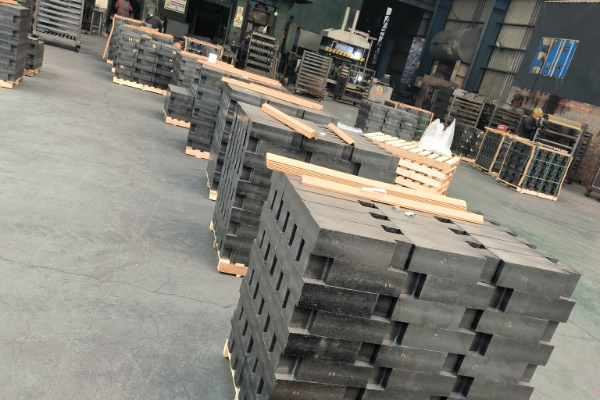
SiC raw materials
SiC has many characteristics that ordinary oxide raw materials do not have, such as high thermal conductivity, low thermal expansion, and difficulty in reacting with slag. For this reason, it has been used as the main raw material for refractory materials in areas where slag reaction and high-temperature peeling are severe for a long time. The same is true for unshaped refractory materials. From the era of digging materials and plastics to the current era of low-cement castables, the importance of SiC has not changed. The anti-oxidation atmosphere of SiC is weak, and along with the oxidation, solid-phase SIO2 and carbon and gas-phase CO and COs gases are generated. When the temperature exceeds 1823K, SiC is unstable and transforms into Si02, causing the ASC system to transform into the AI203-5i02-C series. However, if the system is not a closed system and the ASC working lining is in contact with the outside world, the CO partial pressure may be lower than 0.1 Mpa, at this time, SiC is the most stable.
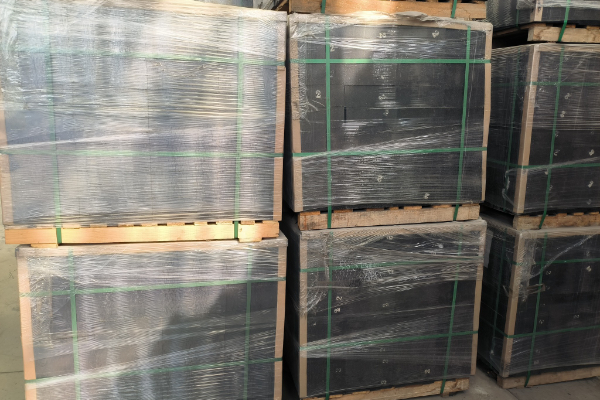
C raw materials
Carbon has the characteristics of not reacting with slag iron and a low thermal expansion rate. Therefore, carbon materials have strong resistance to slag erosion and are not easy to stick to slag. Under certain temperature conditions, 5i in the matrix reacts with C to generate very fine particles. The fibrous Si℃ (diameter is about 0.1~0.5um) forms a reinforcing effect of 5ic. Therefore, when developing ASC refractory materials, carbonaceous materials that evaporate less and have relatively more fixed carbon should be used, and antioxidants and dispersants should be added proportionally.
WeChat
Scan the QR Code with wechat