The production of mag carbon bricks is not complicated, but every step is related to the quality of coal bricks. Among them, mixing, molding, and heat treatment (drying) are particularly important aspects of production.
Mag carbon bricks production process
Raw material crushing
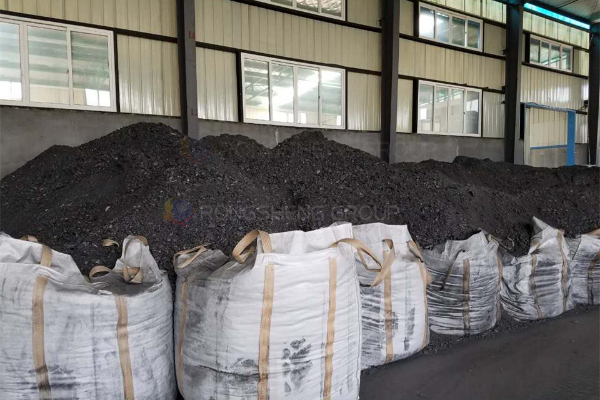
Raw material crushing is the process of processing large pieces of materials into ideal particle-size materials. It is an essential process in the production of refractory materials. Although it is simple, it is very important. It has an important impact on the stability of product quality. The purpose of crushing during the production of magnesia carbon bricks is mainly to prepare raw materials of various particle sizes. Increase the specific surface area of the material and destroy the crystal lattice of the material to cause defects, thereby accelerating the physical and chemical reaction speed of the material.
Ingredients
Ingredients are the process of combining different raw materials and different particles according to product formula design. The method of ingredients varies depending on the type and state of the raw materials.
The gravimetric batching method is usually used in the production of magnesia carbon bricks because the gravimetric batching method has high accuracy and generally does not exceed 2%. Commonly used weight-batching equipment includes manual weighing scales, automatic weighing scales, weighing trucks, etc. The corresponding equipment is selected according to the requirements and automatic control level.
Mixing of magnesia carbon brick raw materials
There are many general categories of magnesia carbon bricks, and the formulas are different depending on the parts they are used in. The main types of magnesia, the amount of graphite added, and the types and quantities of additives will change.
For example, in the slag line of the ladle, in order to improve the slag resistance and thermal shock resistance of magnesia carbon bricks, the grade and amount of graphite must be increased. If the carbon content is less than 10%, a continuous carbon network cannot be formed inside the magnesia carbon brick, and the properties of carbon cannot be fully exerted, affecting the slag resistance and thermal shock resistance of the magnesia carbon brick. If the carbon content is too high, it will not only cause difficulties in the production of magnesia-carbon bricks but also make the magnesia-carbon bricks easily oxidized. Therefore, the carbon content in magnesia carbon bricks is generally controlled between 10% and 20%.
In order to make the magnesia particles evenly wrapped by graphite, the mixing process is generally carried out as follows: first, the pellets, then the resin, then the graphite, and finally the fine powder and various additives. Graphite has a low density, floats easily, and is added in large amounts, so it is not suitable for mixing. Moreover, the amount of additives added is very small, so if you want to mix the entire material evenly, you must stir at high intensity for a long time. However, the binding agent will evaporate and dry out during the mixing process. If the time is too long, the graphite and fine powder wrapped in the particles will fall off, so the mixing time must be controlled.
Mag carbon bricks molding
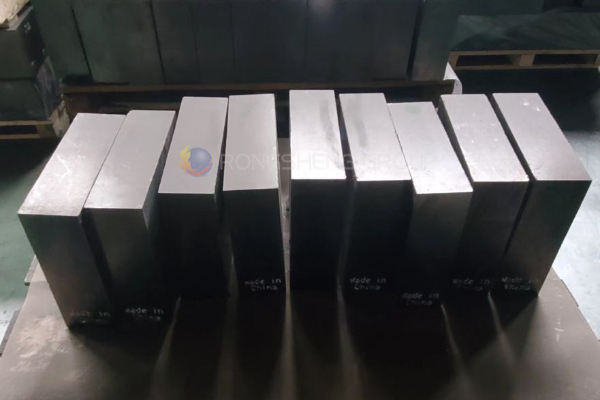
Molding is an essential process for producing shaped refractory products. It is a process in which the refractory mud becomes a green body with a certain shape and strength under the joint action of pressurizing equipment and molds.
Refractory materials have a variety of molding methods. Magnesia carbon bricks are formed by semi-dry pressing. Semi-dry molding has less strict requirements on the mud material and the process is simple. During the pressurization process, due to the low moisture content of the mud material, high pressure must be used to force the particles to be tightly bonded. Under the action of external force, the pellets are rearranged, gases are discharged, and the particles combine and then generate strength, forming a green body with a certain shape. The most important factor in semi-dry molding is external pressure. Within a certain pressure range, the amount of external pressure directly determines the properties of magnesia carbon bricks. As the pressure increases, the density of the green body increases, the porosity decreases, and the strength increases.
Magnesia-carbon bricks with excellent performance all have one thing in common, that is, magnesia-carbon bricks have high volume density and low porosity. Magnesia carbon bricks with an open porosity below 4% have a very low corrosion rate.
The purpose of molding is to densify the structure of magnesia-carbon bricks. Since magnesia-carbon bricks are formed using a semi-dry method, they must be formed under high pressure. Since the mud used for molding has small particle size and high graphite content, molding must be done strictly in accordance with the regulations, otherwise, cracks or spalling will easily occur. It should be light first and then heavy, pressurize multiple times, use a light hammer to exhaust slowly, and a heavy hammer to maintain pressure and lift slowly.
If possible, you can use a vacuum brick press to evacuate the mud in the mold cavity before pressurizing. There is no need to exhaust when pressurizing. In this way, even if the light hammer pressurization speed is accelerated, there will be almost no impact. Magnesia carbon bricks develop cracks or spalls. This is especially important for products such as high-carbon magnesia-carbon bricks, which are prone to spallation.
Heat treatment
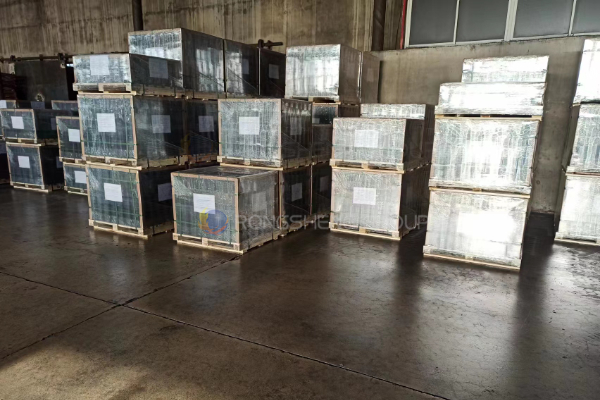
The heat treatment temperature of magnesia carbon bricks has a direct impact on the performance of magnesia carbon bricks. The heat treatment process of magnesia carbon bricks is actually the curing process of phenolic resin. The heat treatment temperature and heat treatment time directly determine whether the phenolic resin is completely cured. Within a certain range, the complete curing time of the resin is inversely proportional to the curing temperature, but it is not a linear relationship.
WeChat
Scan the QR Code with wechat