Fused AZS brick is an important refractory material for glass electric furnaces. Improving the service life of fused zirconium corundum bricks is crucial for glass electric furnaces.
The glass tank kiln melts horizontally, the material liquid level moves horizontally, and the three-phase interface is seriously eroded except for the liquid flow hole, as shown in Figure 1. Electric glass melting furnaces melt vertically, and most of them use cold top melting. The glass liquid surface is covered by a layer of raw material, and there is less three-phase interface. Due to the vertical melting, the erosion of the pool wall bricks is no longer concentrated at the three-phase interface, but the overall erosion. Therefore, the weak link of the fused corundum bricks is the breakthrough point of erosion, as shown in Figures 2 to 4.
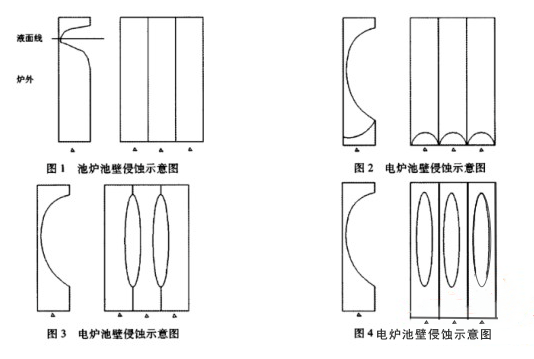
In view of the corrosion mechanism of fused zirconium corundum bricks, the Na2O content in the raw material ingredients of fused zirconium corundum bricks must first be strictly controlled. The national standard requires that the Na2O content in 33#WS should be below 1.45%, and the Na2O content in 41#WS should be below 1.3%. Below, Rongsheng Company’s electric furnace standards require that the Na2O content in 33WS be below 1.35% and that in 41#WS be below 1.05%.
For the erosion site in Figure 2, it is required that the ratio of the riser to the bricks must reach 1.5:1. Through the pressure of the riser material, the residual pores in the bricks can be effectively reduced, and the anti-erosion ability of the bricks at the injection port can be enhanced, and the injection port is required. No obvious shrinkage remains.
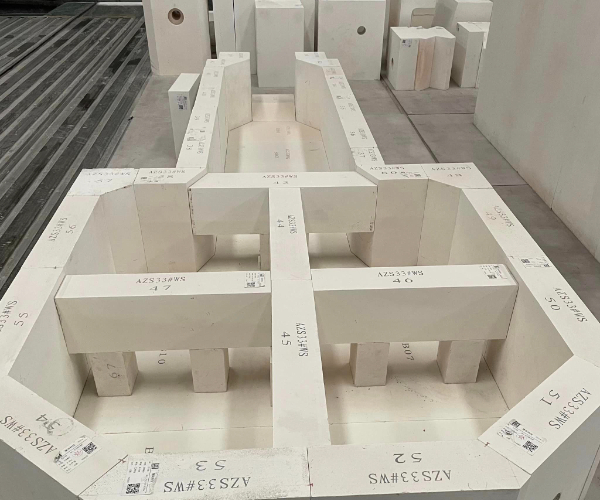
For the corroded parts in Figure 3, the brick joints are strictly inspected during the assembly process of the fused zirconium corundum bricks and are required to be below 0.3mm. During the kiln baking process, the expansion difference of each part is strictly controlled to ensure the tightness of the brick joints during the process, thereby reducing Gas enters to prevent the formation of a three-phase interface at the brick joints and reduce erosion in the location shown in Figure 3.
In view of the erosion in the area shown in Figure 4, the width of the bricks is required to be less than 400mm during the design process. Excessive width will lead to excessive shrinkage cavities and loose interiors; it is required that the ratio of the riser to the bricks must reach 1.5:1, and the bricks must be discharged through pressure and discharge. The gas rate improves the internal quality of the bricks; reducing heat preservation in the later stages of the kiln operation reduces the erosion rate by lowering the temperature of the bricks.
WeChat
Scan the QR Code with wechat