Cement production needs to go through “two grinding and one burning”, that is, raw meal mill, cement kiln, and cement mill. The cement kiln burns cement raw meal at high temperatures. Thermal equipment for cement clinker is an extremely important link in cement production.
Main raw materials for cement production
Specifically, it includes limestone, clay raw materials, correction raw materials (supplementing deficient ingredients), and auxiliary raw materials (mineralizers, fluxes, grinding aids)
Cement kiln types
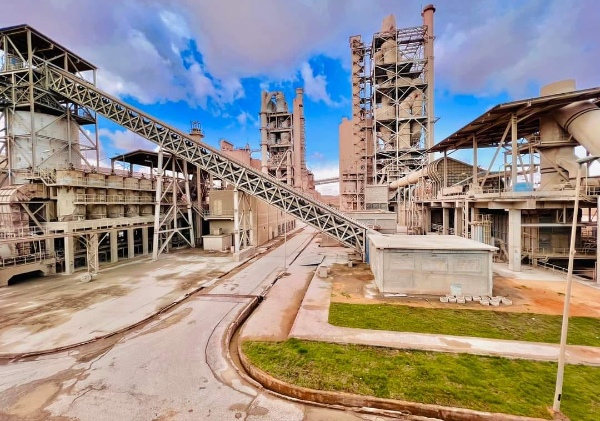
Cement kilns are divided into vertical kilns (vertical kilns) and rotary kilns according to the shape of the production kiln. According to the preparation methods of cement raw materials, they are mainly divided into dry methods, wet methods, and semi-dry methods.
Suspension preheater working environment
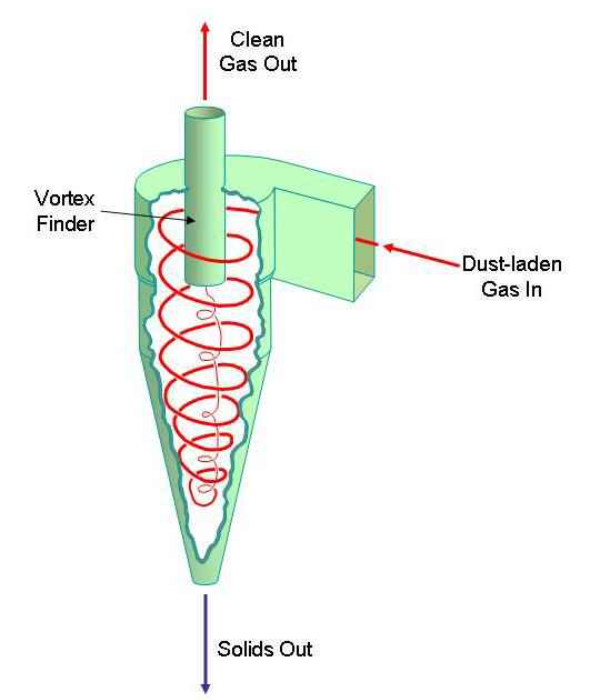
The suspension preheater has different temperatures from the first stage to the last stage, which are no higher than 450℃, 650℃, 750℃, 9000℃, and 1100℃. The temperature of the precalciner kiln is not higher than 1400℃. At the temperature of the first three preheaters, there is basically no liquid phase in the material, so there is basically no agglomeration and sintering, and the thermal state is relatively stable, so there is no thermal shock to the material.
Stability requirements are not high either. The range of 800 to 1200°C is the temperature zone where alkali metal oxides condense and deposit. Therefore, in the presence of raw and fuel materials with high alkali content, refractory materials are not only subject to thermal erosion but also to chemical erosion of alkali metal oxides.
Suspension preheater refractory material
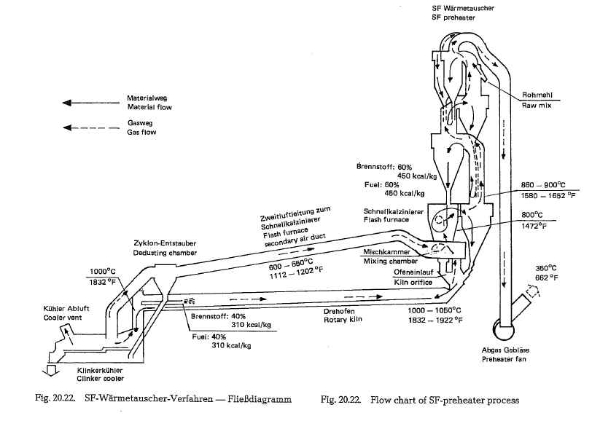
For the first three-stage preheaters of C1, C2, and C3, the penetration and erosion of alkali metal elements in the raw materials are mainly considered. The working layer refractory materials mainly use alkali-resistant refractory materials, such as alkali-resistant castables, alkali-resistant bricks, etc. For the C4 and C5 two-stage preheaters and precalciners, part of the liquid phase has been produced in the raw meal at this temperature, which is easy to mix with the cement raw meal and adhere to the surface of the refractory material, eventually causing the blockage of the raw meal channel. Therefore, C4 and C5 The two-stage preheater should use anti-crushing castables to resist crusting and resistance.
Blockage occurs. Compared with the lower preheater, the precalciner kiln has a relatively small problem of raw meal crusting. The main consideration is the temperature fluctuation caused by the combustion of pulverized coal, gas, etc. Anti-flaking high-aluminum bricks, anti-scaling castables or low-cement high-aluminum bricks can be used. Aluminum/mullite castables.
In terms of structural configuration, the material can adopt a double-layer structure and a layer of insulation material with low thermal conductivity and good thermal insulation effect is provided outside the working layer. The working layer can be made of refractory bricks or castables, but castables should be used for parts with complex shapes.
WeChat
Scan the QR Code with wechat