Refractory balls are also called heat storage balls. A corundum refractory ball is a type of heat storage ball. Heat storage balls are divided into high alumina heat storage balls, corundum heat storage balls, and mullite heat storage balls according to product materials. Zirconium corundum heat storage ball. This article introduces corundum refractory balls.
The function of heat storage ball
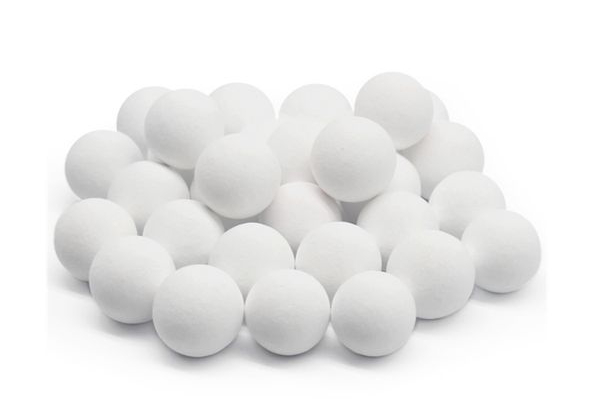
Heat storage balls, also known as spherical heat storage bodies, are made of materials such as AL2O3, kaolin, synthetic aggregates, and mullite crystals and are sintered at high temperatures. There are two methods: rolling and machine pressing. A thermal storage ball is a refractory material that can withstand high temperatures and corrosion and release a certain amount of heat. Especially in the steel smelting industry, thermal storage balls must be used for smelting.
The working process of refractory balls in the regenerator
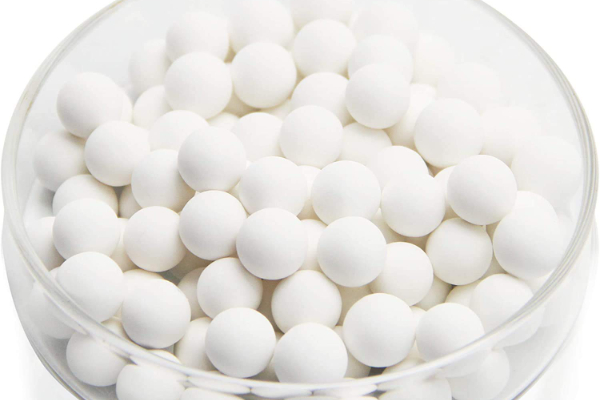
- The regenerator is a space filled with refractory balls. The surface of the regenerator is the heating surface of the regenerator. The regenerator is the medium for storing heat. Therefore, the work of the regenerator must both transfer heat quickly and store heat. more, and at the highest possible temperature level.
- The numerous small balls of the heat storage ball divide the airflow into small streams. When the airflow flows through the heat storage body, it forms a strong turbulent flow, which effectively breaks through the boundary layer on the surface of the heat storage body. Since the ball diameter is small, has a small conduction radius, small thermal resistance, high density, and good thermal conductivity, it can meet the requirements of frequent and rapid reversal of regenerative burners.
- The regenerator can use 20-30 reversals per hour. After the high-temperature flue gas flows through the regenerator bed, the flue gas can be reduced to about 130°C and then emitted.
- When high-temperature gas and airflow through the regenerator are in the same path, they can be preheated to only about 100°C lower than the flue gas temperature, and the temperature efficiency is as high as more than 90%.
- Because the heat storage ball is very small in size, the specific surface area can reach 240㎡/m³. In addition, the small pebble bed has a strong circulation capacity, so even if the resistance increases after dust accumulation, the heat exchange index will not be affected.
- The size of the cross-sectional area of the regenerator is generally obtained by deducting the cross-sectional area of the combustion chamber from the diameter of the selected hot blast furnace. It should be calculated by the airflow velocity in the channel area after filling the regenerator balls. The regenerator is the most important part of the hot blast stove, and its working quality has a significant impact on the air temperature. In itself, its heat transfer efficiency has a lot to do with the size and shape of the heat storage ball.
Characteristics of corundum refractory ball
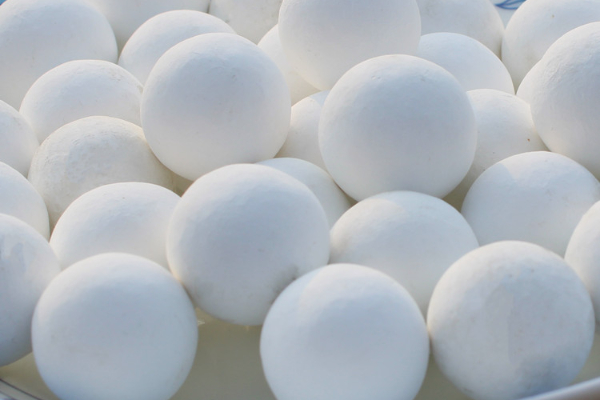
Physical properties of corundum refractory ball:
Composition: Mainly composed of α-Al₂O₃ (corundum) crystal phase.
Density: High density, usually above 3.5 g/cm³.
Hardness: High hardness, typically 9 on the Mohs hardness scale.
Thermal properties of corundum refractory ball
High-temperature resistance: Maintains structural stability at extreme temperatures up to over 1800°C.
Thermal conductivity: Has high thermal conductivity, which helps diffusion and heat dissipation.
Mechanical behavior
Compressive Strength: Has excellent compressive strength and can withstand high-pressure environments.
Chemical stability
Resistant to chemical attack: It has good resistance to chemicals such as acids and alkalis.
Application areas
Lining for high-temperature industrial equipment such as kilns, reactors, and furnaces.
Acts as support material for catalysts.
Widely used in some industrial processes that require high wear resistance and high-temperature stability.
WeChat
Scan the QR Code with wechat