Alumina fire brick is the most representative product of aluminum-silicon refractory bricks. They have higher refractoriness than clay bricks and can be used for many years at high temperatures of 1300℃-1550℃ without erosion or wear. However, the biggest disadvantage is that Thermal shock stability against temperature changes is relatively poor.
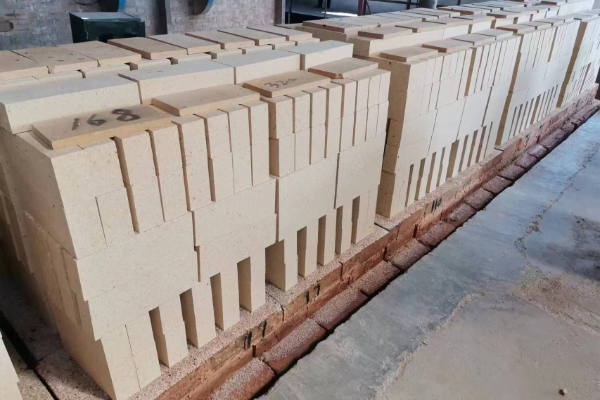
Introduction to high alumina bricks
High alumina bricks are both aluminum-silicon AL2O3-SiO2 refractory materials and neutral to acidic refractory bricks. The mineral element AL2O3 contained in them is an amphoteric oxide. When the AL2O3 content in the high alumina bricks is greater than 73%, it can be used as a medium-grade refractory brick. When the AL2O3 content is less than 41%, it is called clay refractory brick and is used as an acidic product.
How to choose high alumina bricks?
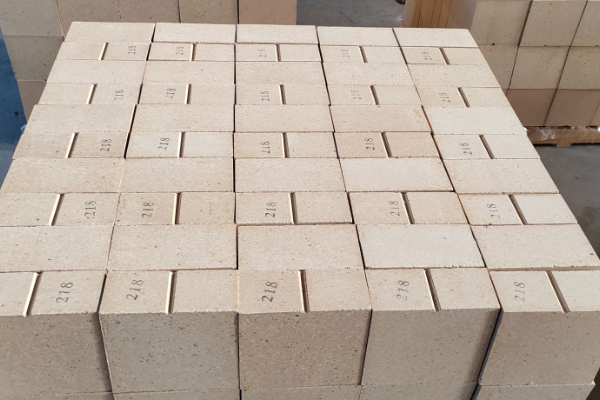
High alumina bricks can be divided into four grades according to different aluminum contents. The selection of high alumina bricks should be based on the production environment of the industrial furnace lining to reasonably select different grades, or select different products for different temperature zones. High alumina bricks Aluminum bricks cannot be used in all environments, but the biggest feature of high alumina bricks is the stable presence of mullite phase and corundum phase under high-temperature use. This is also the reason why high alumina bricks can no longer be corroded or worn. Reasons for long-term use.
Reasons for thermal expansion of alumina fire brick
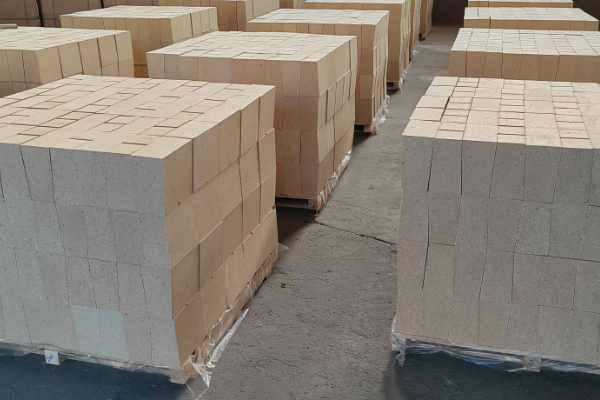
The reason for the thermal expansion of high alumina bricks is that the machine-formed high alumina bricks will be fired in a tunnel kiln. The maximum temperature will be burned to 1430 °C, which will undergo the change from the green body to the molded product, and corresponding thermal expansion will also occur. Among them, at 1365 C and 1330 C, the dimensional expansion rate of the product is 2%~ 3.5%, 1.0%~2%. The linear expansion will stabilize only after reaching 1430°C. The expansion rate is between 0.5% and 1%. In this process, it can be seen that at different temperature sections, the high alumina brick changes from expansion to contraction, so it is a liquid phase sintering Expansion changes.
WeChat
Scan the QR Code with wechat