A leading chemical company based in Nigeria, focusing on the production of chemical products. Since some highly corrosive chemicals are involved in their production, customers seek acid bricks with excellent acid resistance for lining chemical equipment. The customer saw Rongsheng’s website on Google, found the contact information from the website’s Contact Us page, and sent us an email.
Nigerian customer introduction
There is a high concentration of acidic substances in the customer’s production environment, and traditional building bricks cannot meet the corrosion resistance requirements. The customer needed an acid-resistant brick that could work stably in a corrosive environment to ensure the reliable operation of the equipment and increase the service life of the equipment.
Rongsheng acid bricks solution
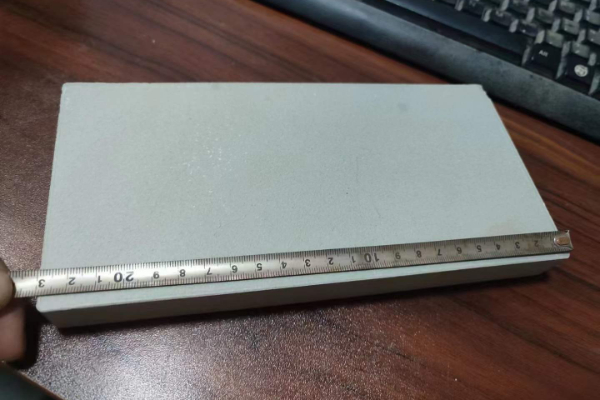
We provide our customers with professional acid-proof tiles, which are corrosion-resistant and acid resistant bricks made of high-purity acid-resistant materials. This acid-resistant brick has excellent corrosion resistance and stability and is suitable for highly acidic environments.
The usage environment of acid-resistant bricks purchased by Nigerian customers
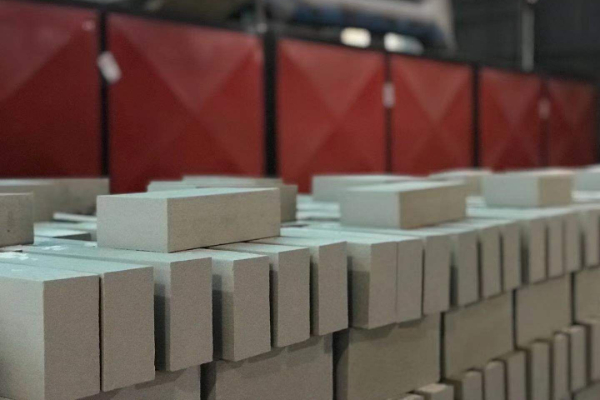
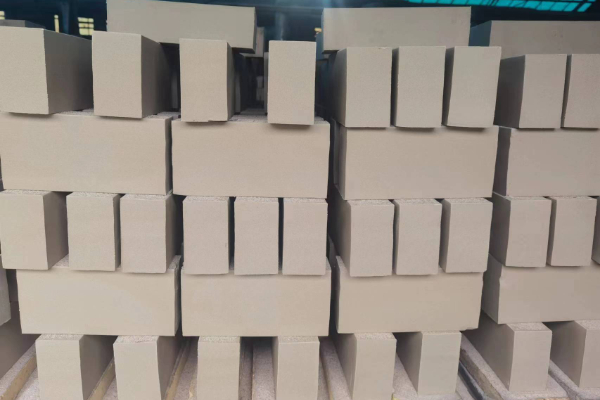
Customers apply our acid-proof tiles to the lining of chemical equipment. The specific usage details mainly include:
- Acid tank and reactor lining: Acid-resistant bricks are used to construct chemical reactors and lining tanks for storing acidic chemicals to resist the attack of strong acids.
- Pipes and pond linings: Acid-resistant bricks are used in the lining of liquid transfer pipes and ponds to ensure structural stability in acidic environments.
How to use acid bricks?
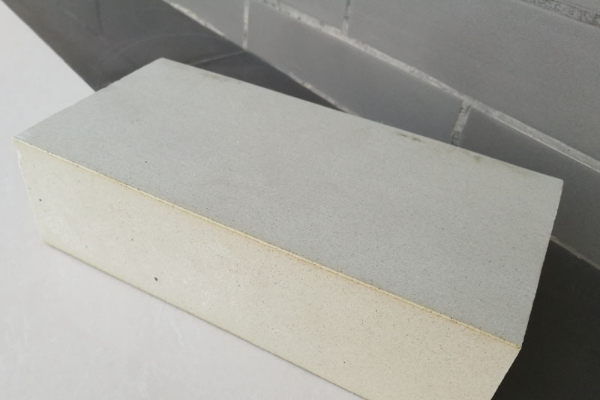
- Preparation: Before installation, ensure that the surface of the equipment is clean and free of impurities and corrosion products.
- Soaking treatment: Soak the acid-resistant brick in water before installation to ensure that the bricks are fully absorbent and improve adhesion.
- Mortar coating: Use special acid-resistant mortar to paste the acid-resistant bricks on the inner wall of the equipment to ensure that the bricks are closely combined with the surface of the equipment.
- Vertical and horizontal alignment: During installation, use a spirit level and measuring tools to ensure that the bricks are vertical and level.
- Gap filling: Fill the gaps between bricks with acid-resistant mortar to ensure the integrity of the lining.
WeChat
Scan the QR Code with wechat