Панель силиката кальция является неорганическим строительным материалом с превосходной производительностью, который широко используется в проектах теплоизоляции в полях строительства, металлургия, электричество, нефтехимический, и т. д.. Он имеет характеристики легкого веса, Высокая сила, Пожарная стойкость, теплоизоляция, устойчивость к влажности, и сопротивление плесени, и является важной частью современных высокоэффективных энергетических проектов. Чтобы гарантировать, что кальциевая силикатная плата достигает хороших результатов в реальном использовании, Научный и стандартизированный процесс кладки необходим.
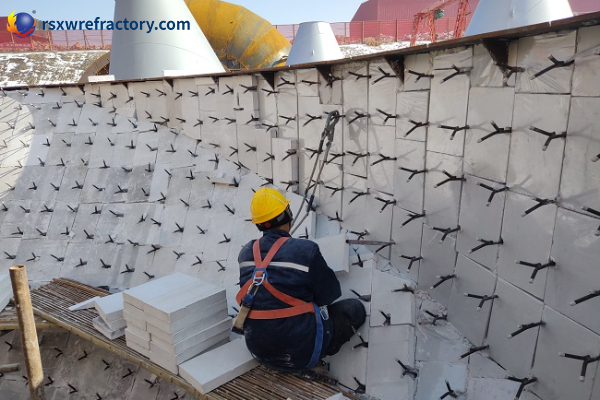
10 Шаги для установки силикатной панели кальция
- Перед строительностью кремниевой крышки, Материальные спецификации кремниевой крышкой пластины должны быть тщательно проверены, чтобы увидеть, соответствуют ли они дизайну. Особое внимание следует уделять, чтобы предотвратить использование низкорезодированных материалов для высокоразмерных материалов.
- Когда кальциевая силикатная доска наклеена на оболочке, Кремниевая крышка должна быть тонко обработана в соответствии с необходимой формой, чтобы минимизировать промежутки, вызванные избеганием гвоздей и других ситуаций. После обработки, равномерно нанесите слой клея на кремниевую крышку, Вставьте его на оболочку, и крепко сжимайте его вручную, чтобы снять воздух, чтобы кремниевая крышка находилась в тесном контакте с оболочкой. Крышка кремния не должна перемещаться после ее построения. И избегайте повреждения кремниевой крышко.
- Ручные пилы или электрические пилы должны использоваться для обработки кремниевых пластин, и Throwels запрещено использовать для резки.
- При заливании рефрактерных материалов под кремниевыми пластинами, построенными на верхней крышке, Чтобы предотвратить падение кремниевых пластин, до того, как прочность клея будет применена, Металлические провода можно использовать, чтобы завязать их на ногти, чтобы сначала починить кремниевые пластины.
- При укладке двухслойных кремниевых пластин, Шофяная каменная кладка должна быть выполнена.
- При заливании материалов на застроенных кремниевых пластинах, Слой гидроизоляционного агента должен быть распылен на кремниевые пластины заранее, чтобы предотвратить влажные кремниевые пластины, а из -за недостаточно увлажненных материалов из -за нехватки воды из -за недостатка воды. Для кремниевых крышек, используемых сверху сверху, Поскольку трудно распылить гидроизоляционный агент вверх при поиске вверх, гидроизоляционный агент должен распылять на стороне в контакте с заливающими материалами перед вставкой.
- При укладке рефрактерных кирпичей на встроенных кремниевых пластинах, Пошарочная кладка должна проводиться во время строительства. Если есть пробелы, они должны быть наполнены клеем.
- Для вертикальных цилиндров или прямых поверхностей, а также вертикальные конические поверхности, Нижний конец используется в качестве эталона во время строительства, и связь выполняется снизу вверх.
- Для каждой части, Комплексная проверка должна быть проведена после завершения кладки. Если есть пробелы или свободные связи, заполните их клей.
- Для кремниевых пластин с большей пластичностью, экспансионные суставы не рассматриваются. Нижняя часть опорной кирпичной пластины крепко подключена кремниевыми пластинами и клеями.
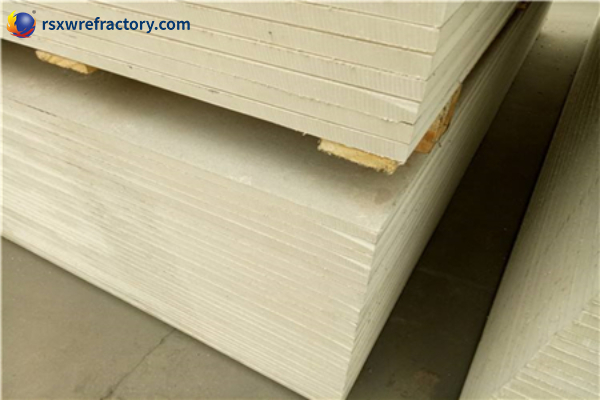
Вичат
Сканируйте QR-код с помощью WeChat