Рафинирование свинца осуществляется доменным методом спекания. (то есть, обжарочно-восстановительный метод рафинирования). Типы печей – доменные печи., доменные печи со свинцово-цинковым уплотнением, oxygen bottom blowing lead smelting (QSL) furnaces, and KIVCET method direct lead smelting furnaces.
Refractory materials for lead-zinc closed blast furnace This furnace is a new furnace type that combines a lead smelting furnace and a zinc smelting furnace to process lead-zinc oxide ore or lead-zinc mixed sulfide ore. It is a thermal equipment that can directly smelt and produce lead and zinc. The lead-zinc airtight blast furnace is mainly composed of an airtight blast furnace, a condenser, a lead mist chamber, a flue, и другие части, and is connected to the lead-zinc retention refining device.
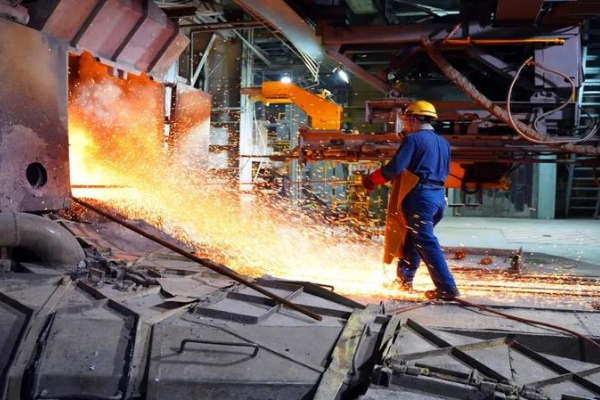
The standard furnace is equipped with 36 air outlets, and the area of the air outlet area is about 10m2. The working layer of the furnace hearth lining and the furnace waist water-cooling plate lining are generally built with magnesia bricks. The hearth’s non-working layer and the furnace body’s lining are made of clay bricks and dense clay bricks. The furnace roof and the chute lining at the connection with the lead mist chamber are generally poured on-site with high alumina cement огнеупорные отливки, or they can be made into prefabricated blocks and hoisted for masonry construction. The bottom and top of the lead fog chamber are built with dense clay bricks or are poured with high-strength refractory castables. The side walls bear the erosion and chemical erosion of lead fog and are damaged quickly, so they need to be built with clay combined with кирпичи из карбида кремния. The rotor and shaft in the lead fog chamber are made of graphite or silicon carbide materials. The flue and other parts are built with ordinary clay bricks.
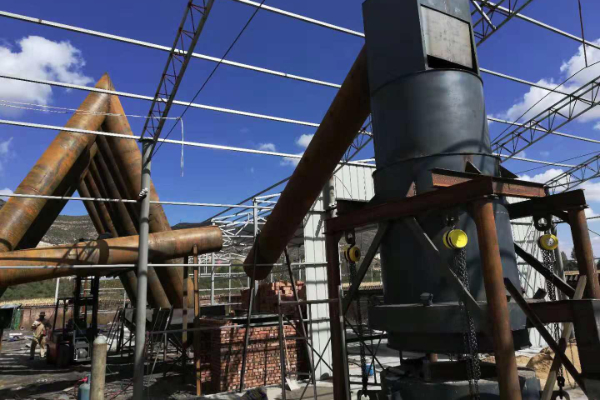
The service life of a furnace is generally 3 к 4 years. The linings in the charging port, furnace waist, damper area, and slag line area are easily damaged and require minor repairs several times during each furnace service. The lifespan of parts such as the lead mist chamber and flue is equivalent to several furnace services, but the rotor and shaft need to be replaced many times. The bottom and top of the lead-zinc separation chamber are generally built with clay bricks or dense clay bricks, the non-working layer of the side walls is made of clay bricks, and the working layer is made of magnesia-chromium bricks. The bottom of the lead liquid flow trough and the lead outlet trough are made of Alz0. It is built with high-alumina bricks with a content of 65%, and the tank walls are built with magnesia-chrome bricks or chrome bricks. The launder can also be poured with refractory castables of the same material to form a highly integrated trough lining. The groove cover plate comprises high alumina cement refractory castable prefabricated blocks. The linings of the lead-zinc separation chamber and launder are in good condition, less damaged, and can work for several furnaces. The linings of the combustion chambers, heat exchanger rooms, and chimneys of lead towers and brocade towers are generally built with clay bricks, and several furnaces can also be used.
Вичат
Сканируйте QR-код с помощью WeChat