Дно электрической печи является ключевой частью электрической печи, которая выдерживает давление, тепловой удар, и коррозия. In order to ensure the stability and durability of the bottom of the electric furnace at high temperatures, dry ramming material is usually used for construction. Dry ramming mass (also known as dry ramming castable) is a refractory material formed by ramming materials. It has high thermal shock resistance, Высокая температурная стойкость, и коррозионная стойкость. Special attention should be paid to the operating details during construction to ensure that the performance of the refractory material at the bottom of the electric furnace is optimal.
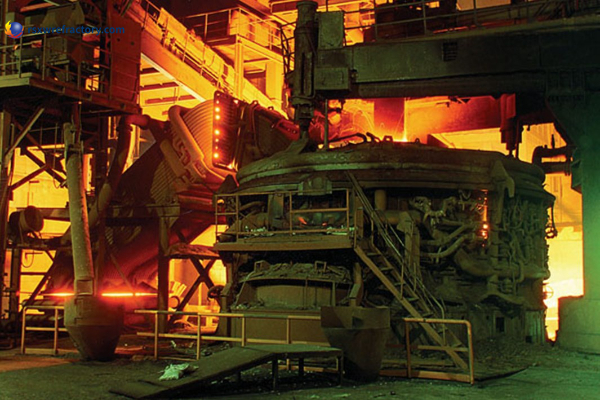
Construction of dry ramming material at the bottom of the electric furnace
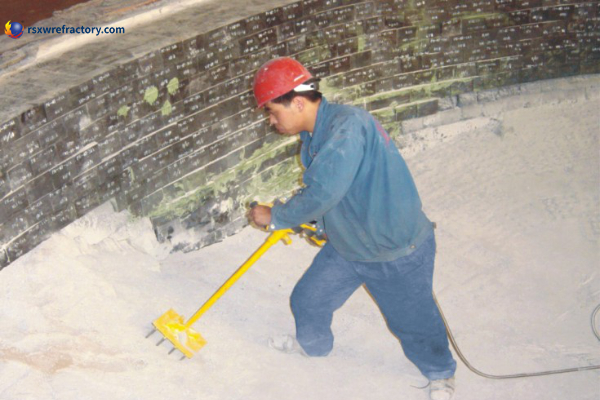
After shoveling and laying the material with a shovel, tamp it down with your feet to remove the air in it. After tamp it down, insert the steel chisel into the material and shake it repeatedly, and then tamp it down further with your feet. The construction thickness of each layer of the ramming material should be 150~200mm, and then use a knotting tool to tamp it repeatedly in a spiral from the periphery to the center for 3 раз.
The method to check the knotting quality is usually to place a round steel with a diameter of 5mm on the ramming layer and press it down with a pressure of 10kg, and the depth should not exceed 30mm. During on-site construction, the steel chisel can be inserted forcefully, and the depth should not exceed 30mm.
The method of knotting the furnace slope is the same as that of the furnace bottom. First, tamp it down with your feet, and then tamp it with a knotting tool. The maximum angle between the furnace slope and the furnace bottom should not exceed 40°. Prevent rolling or collapse due to the large slope of the furnace slope.
In places where the molten steel is stirred and eroded severely, such as the steel outlet seat bricks and the furnace door, it should be rammed more strongly and the size can be appropriately thickened to extend the service life of the refractory materials in these damaged parts as much as possible.
After ramming, a 5-10mm thick steel plate is laid on the ramming material to prevent the shape of the furnace bottom from being damaged when loading scrap steel or the scrap steel from penetrating the ramming material layer, causing hidden dangers of steel leakage. If steelmaking cannot be carried out in time, 100-200mm thick lime is added to the iron plate to prevent the ramming material from hydrating.
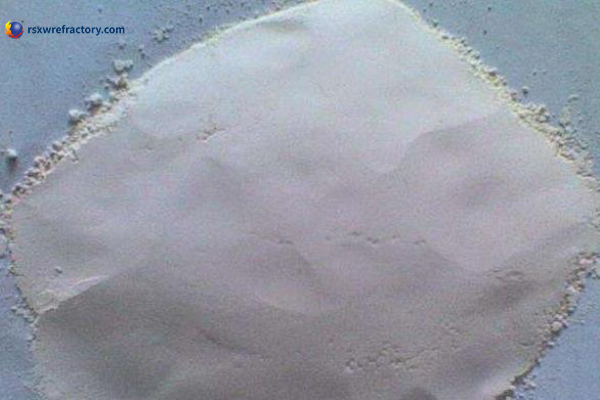
Maintenance after construction
- Curing temperature control: After the construction is completed, drastic temperature differences should be avoided to avoid cracks in the dry ramming material. The initial curing temperature is controlled at 100-150℃, and the temperature is gradually increased to the normal working temperature to avoid direct heating.
- Slow heating: The temperature of the furnace bottom needs to be increased slowly, and the initial heating rate is about 50-100℃/hour, gradually reaching the high temperature required for the electric furnace to work.
- Keep dry: Within 24 hours after the construction of the dry ramming material is completed, contact with water or moisture should be avoided. Especially in high humidity weather, ensure that the environment is dry during construction.
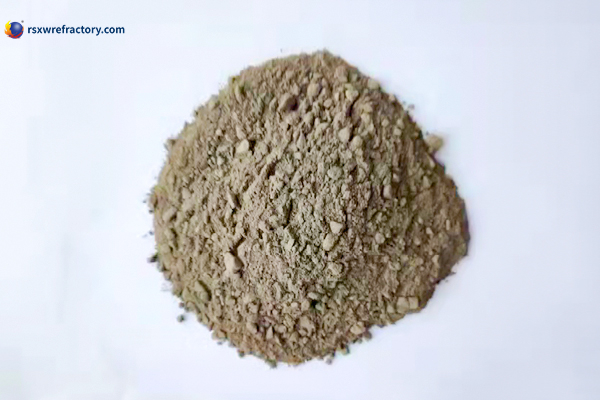
Вичат
Сканируйте QR-код с помощью WeChat