Magnesia ramming mass is an alkaline unshaped refractory made of high-purity fused magnesia/sintered magnesia with ultra-fine powder and additives. It has the characteristics of corrosion resistance, erosion resistance, good volume stability, high load softening temperature, and convenient construction. It is mainly used for new lining, repair, and caulking of iron and steel metallurgy furnaces.
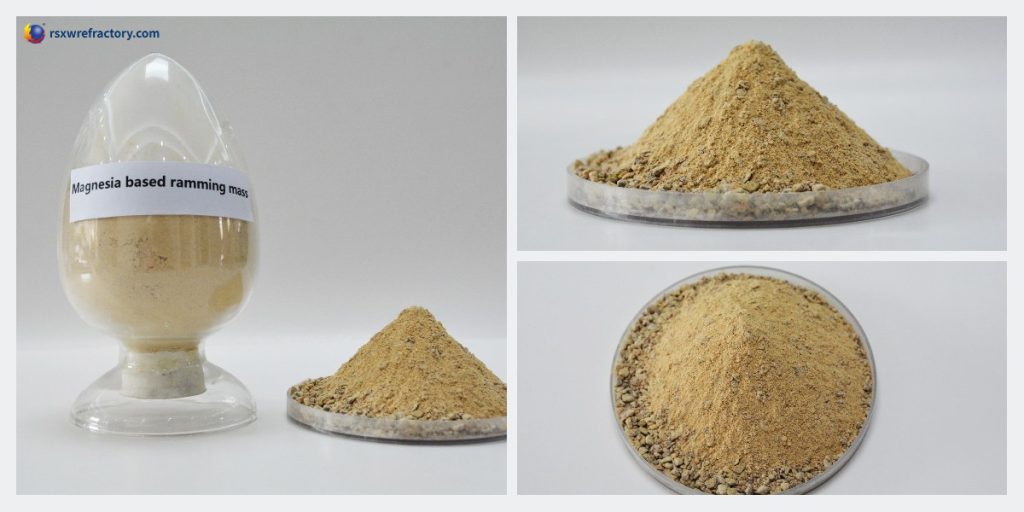
Technical parameter of magnesia ramming mass
Article | Indice | |
MZD1 | MZD2 | |
Mgo % | ≥90 | ≥95 |
Croisement2Ô3 % | ≥2 | |
Densité apparente g/cm3 110℃×24h | ≥2.8 | ≥2.85 |
Cold Crush Strength MPa 110℃×24h | ≥30 | ≥40 |
Grain Size mm | 0~5 | |
Bonding Type | Chemical ceramic bonding |
Characteristics of magnesium ramming mass
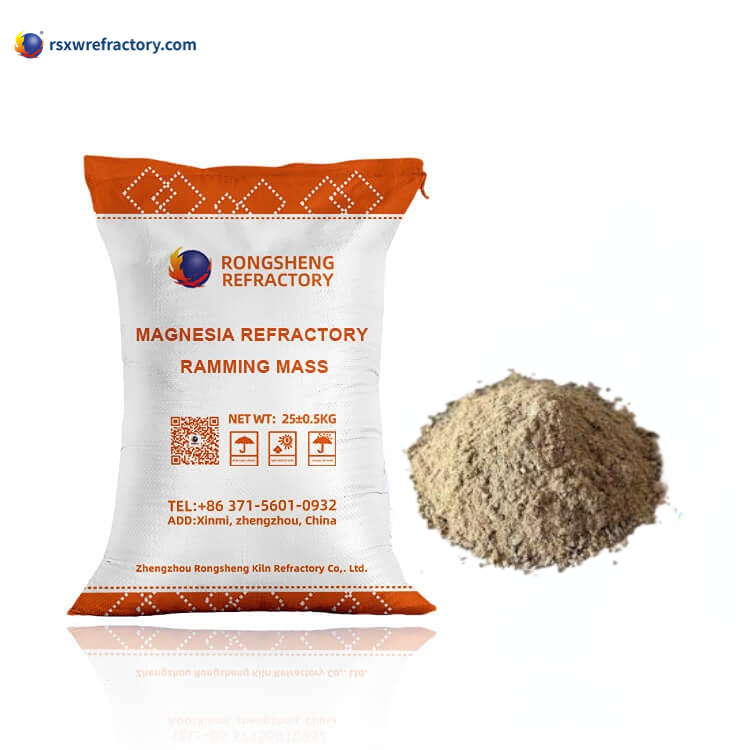
Unshaped refractory is a refractory material that can be used directly without firing. It has the advantages of fast construction, simplified process, energy saving, good integrity, and easy replacement. It is widely used in the metallurgical field. Parmi eux, ramming mass is an unshaped refractory material that is constructed by ramming (manual or mechanical), composed of a high proportion of granular materials and a low proportion of binders and other components, and hardened under heating above normal temperature. The use of magnesium ramming mass on the top of the electric furnace and the copper water jacket at the flue gas outlet of the oxygen-enriched side-blown furnace not only meets the process requirements but also reduces production costs.
Application of ramming mass
Medium frequency furnace ramming mass, magnesium ramming mass, and ferroalloy electric furnace ramming mass are new amorphous refractory materials with stable and reliable refractory performance. They are used in places that are not suitable for refractory brick masonry. They can also be used as caulking and filling. All product performance can reach the level of standardized products. Ramming mass is widely used in the manufacture of ultra-high power, high power, ordinary power arc furnaces and ferroalloy electric furnace bottoms, coreless medium frequency furnaces, cored induction furnaces, and as medium frequency furnace lining materials to melt copper alloys such as red copper, brass, white copper and bronze.
The difference between refractory plastic and refractory ramming material
Refractory plastic et refractory ramming material are amorphous refractory materials that are constructed by ramming or ramming. Due to different binders, their plasticity or working performance varies. When the plasticity index is greater than 15, it is called plastic, and when it is less than 15, it is called ramming material. Dry vibrating material has no plasticity, but it is also usually constructed by ramming. Except for the different ways of sample molding, the performance test methods of plastic and ramming material are basically the same as those of castables.
Testing method of refractory ramming mass
For ramming material, China generally adopts manual ramming method or pressure testing machine molding. Germany uses automatic tamping machine, pneumatic hammer ramming, and moves the mold back and forth at a uniform speed to ram layer by layer. The American standard uses press molding method to prepare samples.
Drying and curing of magnesium ramming mass before use
During the drying process of amorphous refractory materials before use, the surface moisture is first evaporated by heat, and the heat is conducted from the surface to the inside, causing the temperature of adjacent parts to increase gradually. Due to the evaporation of surface moisture, the moisture (steam) inside the refractory gradually diffuses to the surface for replenishment. If the heat supply is too large and the temperature rises too fast, the amount of steam generated per unit of time is too much. Due to the poor air permeability of amorphous refractory materials, the internal moisture (steam) is blocked from diffusing outward. En même temps, due to the vaporization of moisture, the volume increases sharply, and a large tension will be generated inside the refractory. If the tension exceeds the compressive strength of the refractory, it will cause the refractory to expand and crack; when the difference between the two is large, it will peel off or burst. Donc, conventional heating and drying requirements are high, and the performance of the refractory cannot be guaranteed. The magnesium ramming material used can be dried naturally at room temperature, avoiding the damage of high temperature to the refractory, and effectively guaranteeing the performance of the refractory.
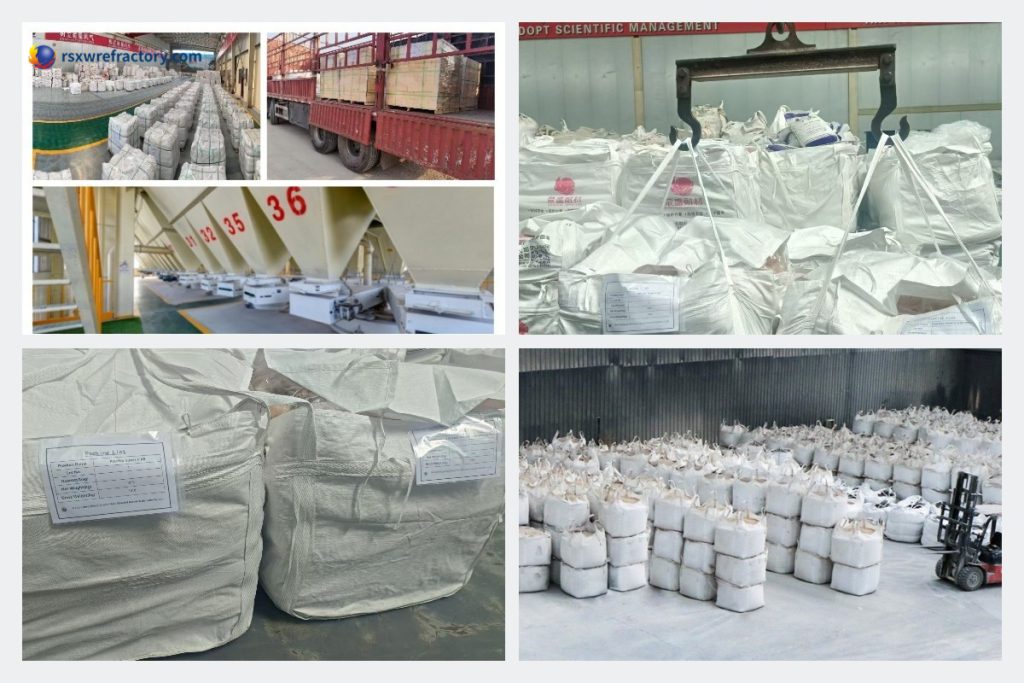
WeChat
Scannez le QR Code avec wechat