Silicon carbide ramming mass is an amorphous refractory material made of silicon carbide (SiC) as the main raw material, combined with high-purity refractory aggregate, liant, and additives. This material has high thermal conductivity, excellent thermal shock resistance, erosion resistance, and wear resistance, and is suitable for repair and lining construction of high-temperature industrial equipment, especially for working conditions that require rapid sintering and long-term durability.
Silicon carbide ramming material characteristics
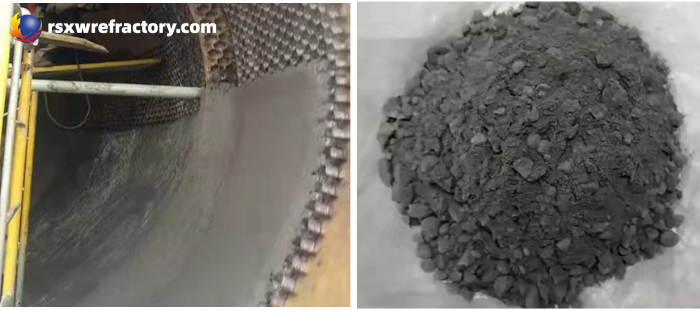
- High refractoriness: temperature resistance can reach above 1600℃, suitable for extremely high temperature environments.
- Excellente résistance aux chocs thermiques: low thermal expansion coefficient, can withstand drastic temperature changes without cracking.
- Chemical erosion resistance: good erosion resistance to acidic and alkaline slag and molten metal (such as aluminum and copper).
- High thermal conductivity: SiC’s high thermal conductivity (~120 W/m·K) helps to dissipate heat evenly and improve the thermal efficiency of equipment.
- Forte résistance à l'usure: suitable for high wear areas, such as metallurgical furnace tapping, kiln lining, etc..
- Convenient construction: ramming molding, suitable for repairing and masonry of complex shapes.
Silicon carbide ramming material introduction
projet | indice | ||
SC30 | SC50 | ||
% SiC | ≥30 | ≥50 | |
Bulk density g/cm3 | ≥2,5 | ≥2.6 | |
Porosité apparente % | ≤18 | ≤18 | |
Résistance à la compression normale de température MPA | 110℃×24h | ≥60 | ≥80 |
1100℃×3h | ≥100 | ≥120 | |
Heating permanent line change % 1400℃×3h | ± 0,3 | ± 0,2 | |
Wear resistance cm3 | ≤6 | ≤4 |
Application of silicon carbide ramming mass
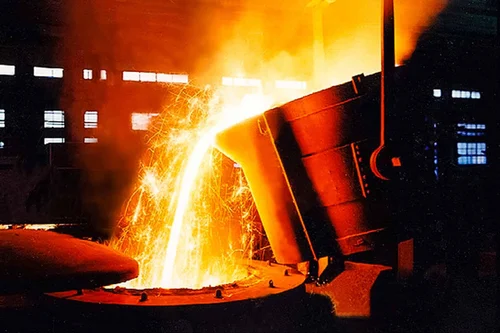
Metallurgical industry: Repair of linings of electric furnaces, blast furnace tapping channels, ladles, and tundishes.
Nonferrous metal smelting: Linings of aluminum electrolytic cells and copper smelting furnaces.
Industrie chimique: Anti-corrosion layer of gasifiers and incinerators.
Ceramic/glass industry: Wear-resistant layer of furnace bottoms and combustion chambers.
Others: High-temperature pipes, haut fourneau chaud, and other areas that require rapid repair.
Construction method
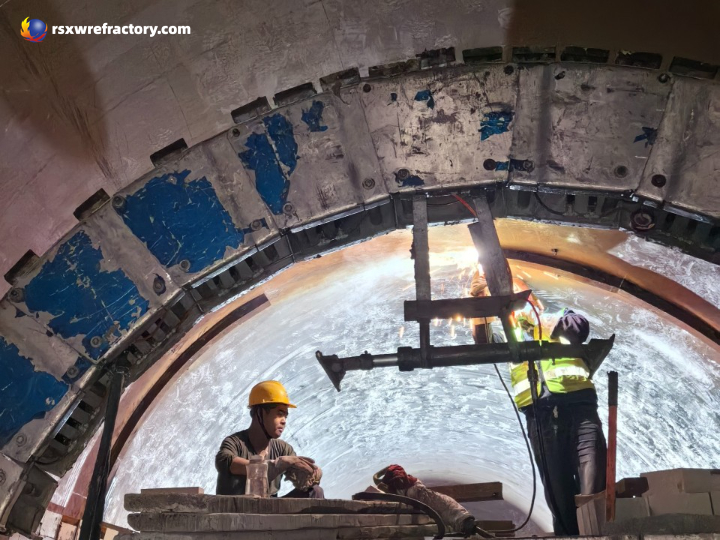
- Matrix treatment: clean the construction surface, remove impurities, and loose layers.
- Mixing and stirring: Add binder (such as water or resin) in proportion and stir evenly until there is no dry powder.
- Ramming and molding: ramming in layers (each layer ≤ 50mm) to ensure that it is dense and has no pores.
- Curing and baking: after natural curing for 24 heures, bake according to the heating curve (avoid rapid heating).
WeChat
Scannez le QR Code avec wechat