Los materiales de embromado refractario generalmente se refieren a la masa de embriaaje seco, que incluye arcilla, alúmina alta, mullita, corundo, silicio, magnesio, carburo de silicio, Mullite Corundum, etc.. Es un material a granel hecho de una variedad de aditivos de polvo ultrafino, cemento fusionado, o resina compuesta como una carpeta. Los diferentes métodos de unión son el vidrio de agua, ácido fosfórico, fosfato, sulfato de aluminio, salmuera, cemento de alúmina alta, arcilla, y otras carpetas. Se utiliza para llenar el vacío entre el equipo de enfriamiento del horno y la mampostería o como relleno para la capa de nivelación de mampostería. El confusión tiene buena estabilidad química, es resistente a la erosión, tener puesto, peladura, y choque térmico, y se usa ampliamente en metalurgia, materiales de construcción, fundición de metal no ferroso, quimicos, maquinaria, y otras industrias manufactureras.
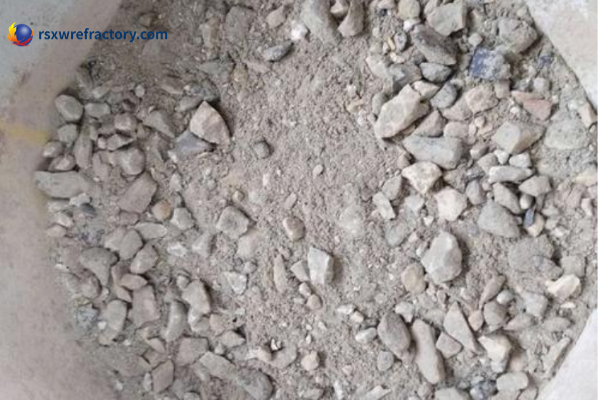
Ácido, neutral, y las masas alcalinadas de embrimiento se usan ampliamente en hornos de frecuencia media sin núcleo y hornos de inducción con núcleo. Como masas de embrimientos de horno de frecuencia media, se usan para derretir el hierro fundido gris, hierro dúctil, hierro fundido, aleaciones de hierro fundido y hierro fundido, Derretir acero al carbono, acero aleado, acero de alto manganeso, herramienta de acero, acero resistente al calor, acero inoxidable, derretir aluminio y sus aleaciones, fundir cobre, latón, plata de níquel, bronce y otras aleaciones de cobre y otros aceros especiales.
Masa de embrollo de carbono
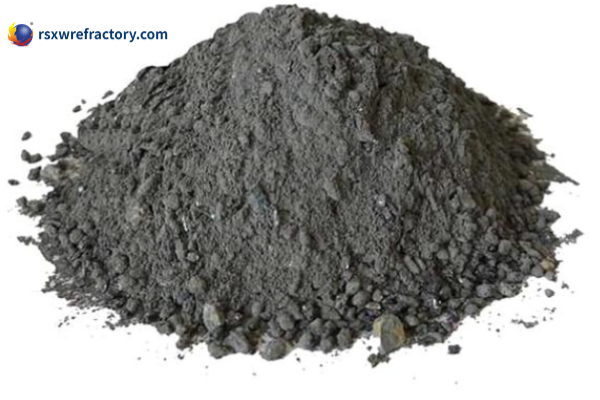
De acuerdo con diferentes tipos de alto horno y diferentes requisitos de diseño de materiales, La masa de embromado de carbono se usa principalmente para los espacios entre los ladrillos de carbono en la parte inferior del alto horno y la placa de sellado en la parte inferior, entre los ladrillos de carbono en el hogar y la pared de enfriamiento, así como la nivelación sobre la línea central de la tubería de enfriamiento de agua en la parte inferior del horno y el relleno de la pared de enfriamiento. Todas las partes requieren que la masa de embromado de carbono después de la embriaaje tenga una cierta resistencia y densidad, llenar cada esquina y un vacío muy pequeño para cumplir con los requisitos de no fugas de gas de hierro fundido y carbón, y la conductividad térmica de la masa de embriaaje de carbono debe ser básicamente consistente con el rendimiento de los ladrillos de carbono caliente y la pared de enfriamiento del alto horno, para no afectar la vida del alto horno, manteniendo así la producción normal del alto horno.
Actualmente, El problema común encontrado en el uso de la masa de embriaaje de carbono es que la conductividad térmica de la masa general de embriaaje de carbono es baja, que no es propicio para el enfriamiento rápido del cuerpo del alto horno, afectando así la vida útil. Por lo tanto, La investigación actualizada y la aplicación de la masa de embriaaje de carbono con un alto coeficiente térmico tienen excelentes perspectivas de mercado. Si agregue aditivos al material de embromado de carbono para cambiar las propiedades del material a través de reacciones in situ a altas temperaturas, o cambiar la estructura de uso del material local desde una perspectiva de diseño, La capa de material de embromado de carbono puede alcanzar una conductividad térmica que coincida con los ladrillos de carbono y las paredes de enfriamiento cuando aumenta la temperatura de trabajo, para garantizar la conducción de calor normal sin dañar la estructura de construcción general, logrando así el requisito de aumentar la vida del alto horno.
Masa de marco de sílice
Material de marco de sílice, la principal materia prima, es sílice. La sílice es el nombre general del cuarzo de venas, cuarcita, y arenisca de cuarzo. Se utiliza principalmente para ladrillos refractarios ácidos en la industria metalúrgica. Se puede usar sílice pura para hacer vidrio de cuarzo o extraer silicio de cristal único. Se utiliza en la industria química para preparar compuestos de silicio y silicatos y también se puede usar como relleno para torres de ácido sulfúrico. Se utiliza en la industria de materiales de construcción para vidrio, cerámica, cemento de silicato, etc.. Las propiedades de apariencia son principalmente la forma, sección transversal, color, brillo, inclusiones, etc.. de sílice. Por apariencia, Se puede determinar preliminarmente si la sílice es de sílice cristalina o sílice cementada, si es cuarzo de venas, etc.. La aparición de la sílice cristalina es generalmente blanca lechosa, blanco grisáceo, amarillo claro, y marrón rojizo. Tiene un brillo brillante, una sección transversal suave y continua, y bordes afilados y esquinas, y tiene una gran dureza y fuerza. El cuarzo de la vena es denso y bloqueado, blanco puro, translúcido, y tiene un brillo grasiento. La sección transversal tiene forma de carcasa, y las partículas de cristal de cuarzo son en su mayoría más de 2 mm y se pueden ver a simple vista. La apariencia de sílice cementada es blanca, blanco grisáceo, gris amarillo, negro, rojo, etc.. La sección transversal es densa y en forma de concha, sin una estructura granular obvia. Los bordes afilados de la sección transversal no son obvios, Y es casi plano y no tiene brillo. La buena sílice debe ser densa y bloquea, A veces con secciones transversales en forma de conchas o escamosas, sin una estructura en capas obvia, No hay inclusiones entre capas, y no hay caparazón de piedra caliza. Su color depende de las impurezas. Generalmente, Los compuestos de hierro hacen sílice de color marrón rojizo, Mientras que las impurezas orgánicas hacen la sílice gris, negro, etc..
Misa de embrollo de corundum
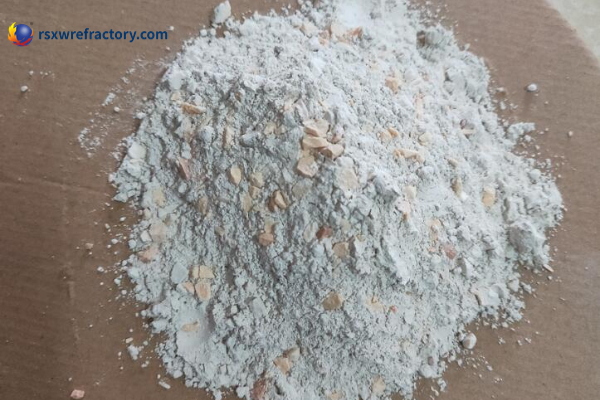
El material de embromado de corundum es un material a granel hecho de corindón, carburo de silicio, grafito, y antracita calcinada eléctrica como materias primas, mezclado con una variedad de aditivos de polvo ultrafino, y cemento fusionado o resina compuesta como una carpeta. Se utiliza para llenar el vacío entre el equipo de enfriamiento del horno y la mampostería o como relleno para la capa de nivelación de mampostería.
Masa de revestimiento de magnesio
Masa de revestimiento de magnesio es un material a granel hecho de magnesia fusionada como materia prima, mezclado con una variedad de aditivos de polvo ultrafino, y cemento fusionado o resina compuesta como una carpeta. Se utiliza para llenar el vacío entre el equipo de enfriamiento del horno y la mampostería o como relleno para la capa de nivelación de mampostería.
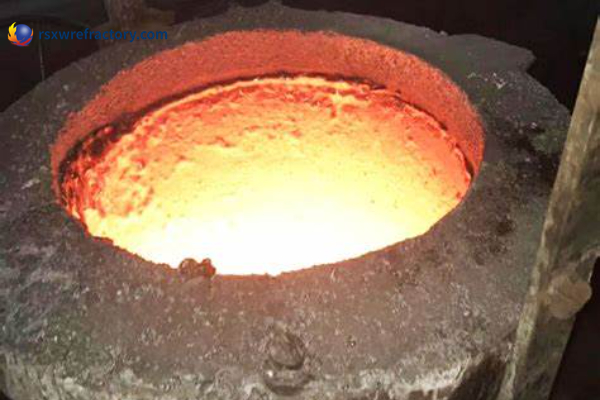
Misa de embromado del horno de frecuencia media
El horno de inducción de frecuencia media está hecho de una bobina de inducción hecha de un tubo de cobre y enrollado alrededor del exterior del horno. La carga de metal se coloca en el horno. Cuando la corriente alterna pasa a través de la bobina de inducción, Se genera un flujo magnético alterno en la bobina. A través de la carga de metal cerrado, Se genera una corriente de inducción dentro de una cierta profundidad en la superficie de la carga, haciendo que la carga se caliente y se derrita. El revestimiento del horno está construido con materiales refractarios, que requieren una buena resistencia a la corrosión, resistencia a la pelea, Sin grietas, y larga vida útil. El material utilizado para el horno de frecuencia media es el material de embrimientos de horno de frecuencia media, y sus principales indicadores de rendimiento.
WeChat
Escanea el código QR con wechat