La alúmina tabular es un gran bloque de alúmina α con alta pureza y estructura cristalina densa después de sinterización de alta temperatura. Debido a sus excelentes propiedades físicas y químicas, it is widely used in high-performance Castables refractarios, especialmente en partes de acero de alta temperatura, metales no ferrosos, Industrias de vidrio y cerámica.
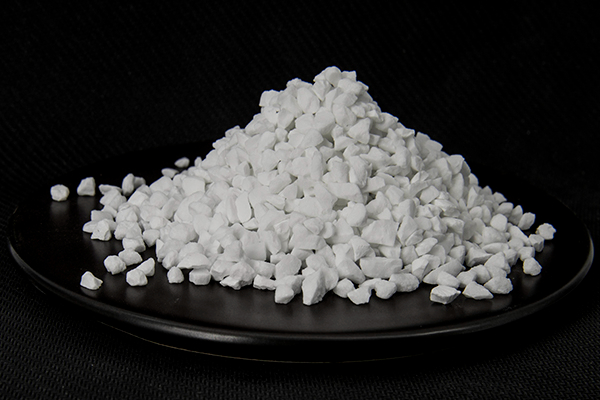
The role of tabular alumina in castables
Improve refractory performance: Tabular corundum has high refractoriness and high melting point, and can withstand high temperature environments and maintain structural integrity and stability. This feature makes castables made of tabular corundum have excellent refractory performance and can effectively resist the erosion of high-temperature melts such as molten steel and slag, thereby extending the service life of the equipment.
Enhance chemical stability: Tabular corundum has excellent chemical stability and can resist the erosion of various corrosive substances. Con la atención tabular corundum to the castable can significantly improve the material’s corrosion resistance, reduce material damage caused by corrosion, and further extend the service life of the equipment.
Improve wear resistance: Tabular corundum has good wear resistance and can withstand various wear and impact. In castables, tabular corundum can be used as aggregate to increase the hardness and wear resistance of the material, so that the equipment can still maintain a good shape and performance during long-term use.
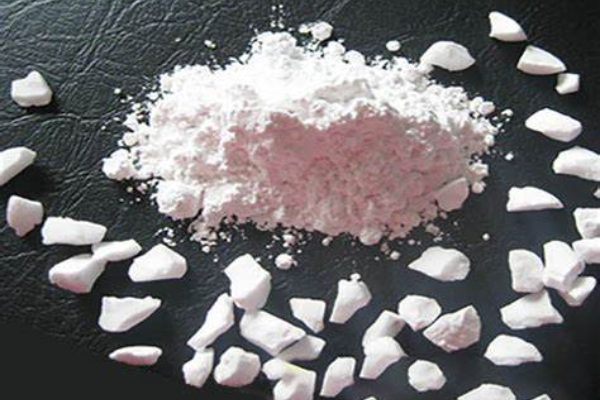
Optimize construction process: The construction process of tabular corundum is relatively simple, and it can be firmly adhered to the surface of the equipment by pasting and other methods. Al mismo tiempo, it can also be used in conjunction with fillers such as thermosetting resins to ensure that the tabular corundum presents a flat state on the surface of the equipment. This helps to optimize the construction process and improve construction efficiency and quality.
Improve thermal shock stability: Tabular corundum has good high temperature resistance, high thermal conductivity and low thermal expansion coefficient, which can effectively maintain the temperature of the smelting material, reduce thermal stress in the casting process, and avoid defects such as cracks and pores, thereby improving smelting efficiency and casting quality.
WeChat
Escanea el código QR con wechat