Los ladrillos de circón para hornos de vidrio se hacen principalmente sinterizando una sola piedra de circón. Para mejorar el rendimiento de los ladrillos de circón, Otros ingredientes (como Zirconia, alta alúmina bauxita, Corundón fusionado, óxido de cromo, etc.) se agregan ) to special zirconium bricks.
Properties of zircon raw materials
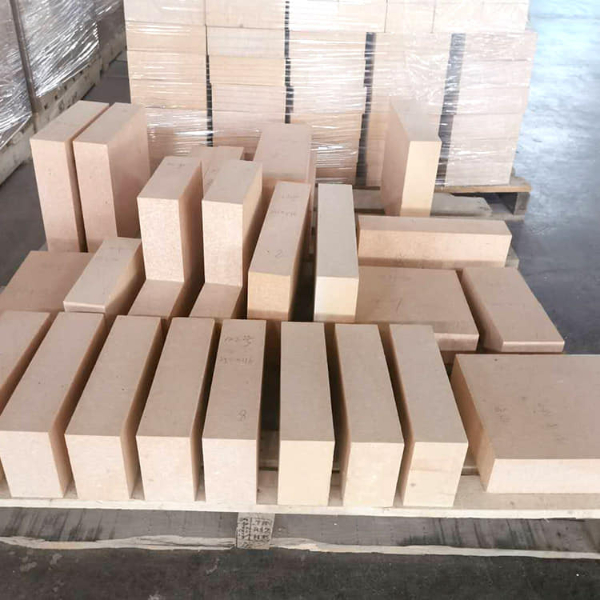
The thermal conductivity of zircon is low, and the linear expansion coefficient is lower than that of its crystal. Zircon is chemically inert and difficult to interact with acids. Some molten metals do not interact with it, while glass and furnace liquid react with it to a lesser extent. Molten alkali fluorides, hydroxides, carbonates, and sulfites can decompose zircon. Además, alkali and acid solutions do not react with zirconium when heated. The effect of stone.
Zircon bricks for glass melting furnace
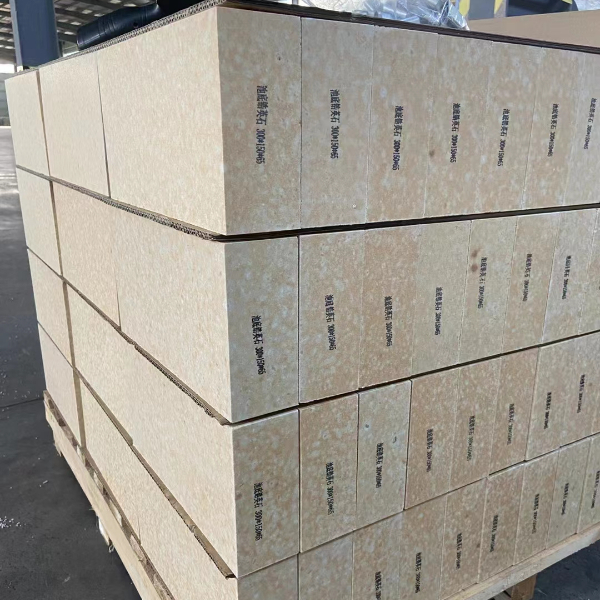
Zircon brick is one of the commonly used refractory bricks for glass kiln construction. Its main raw material is zircon (ZrO2·SiO2). Zircon is a tetragonal mineral with a hardness of 7.8 and a melting point of 2550°C. The chemical properties of zircon are quite stable and are not affected by the erosion of molten glass and slag. In the application of glass tank kiln, it is mainly used in the large slag furnace, fire sight hole, and detection hole, as well as the breast wall of the melting part, the sealing layer of the arch foot tank bottom, etc.. Zircon bricks have good resistance to the erosion of alkali-free glass liquid and can be used as refractory materials in areas with lower temperatures that are in contact with alkali-free glass liquid. Aggregate zircon bricks with good thermal shock resistance can be used in superstructures where temperature changes are not large. Además, zirconium corundum bricks have good electrical insulation properties below 1650°C and can also be used as electrical parts materials.
Introduction to the production process of zircon bricks
Handling of raw materials
Zircon bricks are refractory bricks with zircon as the main crystal phase. They are one of the important varieties of zirconium-containing refractory materials. Today we will introduce the production process of zircon bricks.
To make pure zircon refractory bricks with coarse particles, to facilitate the adjustment of the particle size composition of the refractory bricks and reduce firing shrinkage, the concentrated ore is usually pre-calcinated or melted at high temperature to form zircon clinker briquettes. When calcining clinker, first grind part of the concentrated ore into a fine powder, mix it with another part of the concentrated ore and bind it with a temporary organic binder to make a ball or blank. temperatura) to form a dense mass. If there are alkali metal oxides or mineralizers such as MgO and CaO, they can also be calcined at a lower temperature above 1050°C. Zircon sand begins to shrink at 900°C during calcination, and the shrinkage tends to stop at about 1350°C. After that, it expands and shrinks sharply after 1700°C. The density of zircon concentrate sand briquettes increases after calcination, and the volume density can reach more than 3.5g/cm3. If pure zircon bricks are produced from fine powder materials, the concentrated ore can be directly calcined at 1450°C, loosened by rapid cooling, and then ground finely.
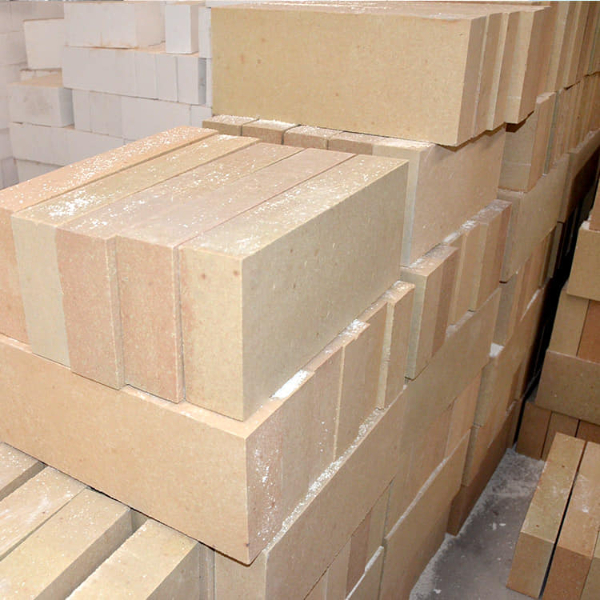
Production of refractory bricks
Temporary binding agents should be used to produce pure zircon bricks, such as sulfite pulp waste liquid, dextrin, and lignin. Ethyl silicate, calcium alkyl acid phosphoric acid, and water glass can also be used. If plastic refractory clay is used as a binder, the refractory bricks are easy to shape and sinter, but this often leads to a decrease in the refractory bricks’ refractory resistance and volume stability. The impact is particularly significant when the amount of clay added to the ingredients is high. In order to promote the sintering of pure zircon bricks, a small amount of CaO or Ca(OH)2, MgO or MgF2, and other mineralizers are often added to the ingredients. This additive promotes the decomposition of ZrO2·SiO2 at high temperatures, forms a ZrO2 solid solution with ZrO2, and enters the glass phase, thereby promoting sintering.
When using pure zircon stone ingredients, in order to ensure that the refractory bricks have good properties and shapes, the particle size, and the amount of binders and admixtures must be coordinated. For refractory bricks containing various levels of coarse particles, multi-level particle batching is required, and the specific surface area and content of fine particles should be higher than ordinary refractory bricks to facilitate the production of dense bodies and easy sintering. If the green body is entirely composed of fine particles, the large particle size of the fine powder is usually below 44/μm, among which those in the order of several microns should account for the majority. When forming, according to the requirements for the density of refractory bricks, ordinary refractory bricks are generally formed by mud extrusion and dry pressing methods; for dense ones, mud casting is often used; for high density, mud casting and isostatic pressing are often used. The various components in the ingredients should correspond to the molding method. This pure zircon refractory brick must be fired at a higher temperature. High-density refractory bricks require higher temperatures. Depending on the nature and content of the fine powder in the green body and the type and quantity of mineralizer, the high firing temperature is generally around 1700°C, which should be controlled so that the green body does not undergo significant sintering. deformation temperature and corresponding to the holding time.
WeChat
Escanea el código QR con wechat