In the field of materiali refrattari, magnesia carbon brick and alumina magnesia carbon brick are two common high-performance materials, which are widely used in high-temperature equipment in industries such as steel, cement, and glass. Although they have similar names, they have significant differences in composition, performance, and application scenarios.
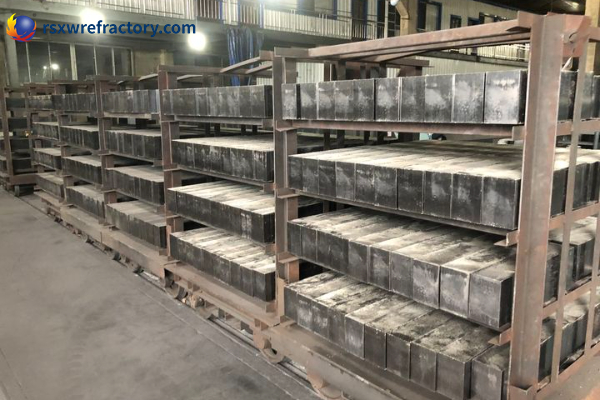
What are the differences between magnesia carbon brick and alumina magnesia carbon brick?
Magnesia carbon bricks perform well in heat resistance, Resistenza alla corrosione, corrosion resistance and spalling resistance. Magnesia carbon bricks are mainly used in the lining of converters, electric arc furnaces, DC arc furnaces, ladle slag lines and other parts.
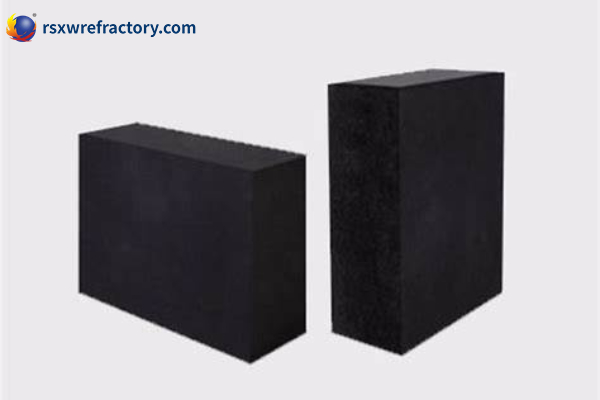
Magnesia-alumina-carbon bricks are made of high-quality bauxite, corindone, fused magnesia and graphite. Alumina-magnesia-carbon bricks have appropriate residual expansion, low thermal conductivity and better insulation function. Alumina-magnesia-carbon bricks are used for the slag line of the ladle, the lower part of the ladle wall, the bottom of the ladle and the free area of the ladle.
The magnesium oxide contained in magnesia carbon bricks is determined by the materials used. The rare magnesia carbon bricks mainly include 72% magnesia, 74% magnesia, 76% magnesia, 80% magnesia, 82% magnesia and 85% magnesia. The main raw materials for consumption of magnesia carbon bricks are fused magnesia, graphite, metal aluminum powder, metal silicon powder, and liquid phenolic resin, which are mixed by a sand mixer and then pressed by a press. Magnesia carbon bricks are used in the slag line of the refined steel ladle. Magnesia carbon bricks are also used in the lining parts of AC arc furnaces, DC arc furnaces and converters.
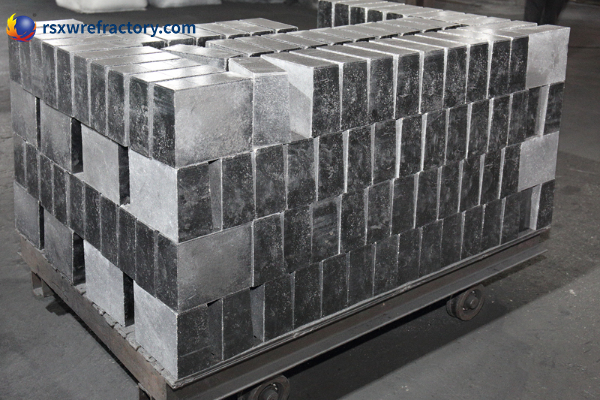
WeChat
Scansiona il codice QR con wechat