Phosphate castable refers to a castable combined with phosphoric acid or phosphate, and its hardening mechanism is related to the type of binder used and the hardening method.
The binder of the phosphate castable can be phosphoric acid or a mixed solution of aluminum dihydrogen phosphate produced by the reaction of phosphoric acid and aluminum hydroxide. Generalmente, the binder and aluminum silicate do not react at room temperature (except for iron). Heating is required to dehydrate and condense the binder and bond the aggregate powder together to obtain the strength at room temperature.
When using a coagulant, heating is not required, and fine magnesia powder or high alumina cement can be added for coagulation. When magnesium oxide fine powder is added, it reacts quickly with phosphoric acid to form, causing refractory materials to set and harden. When aluminate cement is added, phosphates with good gelling properties, water-containing phosphates such as monocalcium phosphate or diphosphate are formed. Hydrogen calcium, etc., cause the material to condense and harden.
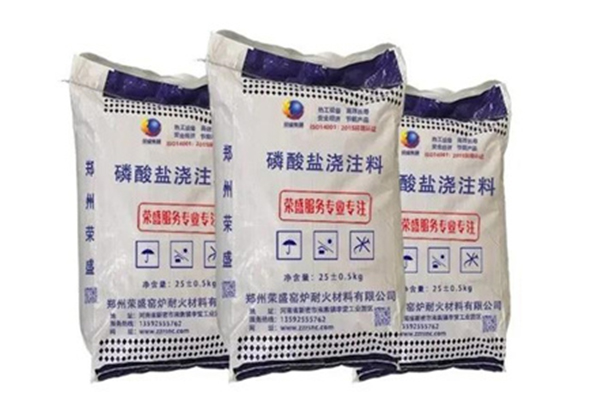
From the hardening mechanism of phosphoric acid and phosphate refractory castables, it is known that only when the reaction rate between the cement and the refractory aggregate and powder is appropriate during the heating process can an excellent refractory castable be formed. Sin embargo, the refractory raw materials are easily brought into the process of pulverization, ball milling and mixing, and it is easy to bring in impurities such as metal iron. During mixing, it will react with the cementing agent to release hydrogen, which will cause the refractory castable to swell, loose the structure and reduce the compressive strength. This is unfavorable for the production of ordinary phosphoric acid and phosphate refractory castables.
- Process method to eliminate bulging
1) Difficult material
That is to say, about 3/5 of the amount of refractory aggregates and powders and cementing agent are mixed and mixed evenly, put into the silo or trapped material site, covered with plastic cloth to prevent the cementing agent from evaporating; at the same time, it must not be in contact with water, and the temperature should be greater than 15 ℃, let it stand for a period of time to make the cement fully react with the metal in the refractory aggregate and powder to release hydrogen.
2) Flushing, magnetic separation
Use porcelain ball mill to grind or use strong acid (such as hydrochloric acid, etc.) to wash the powder, and use magnetic separation and other methods to bring in or remove metal and other impurities.
3) Inhibitor
It is also possible to reduce the amount of cementing agent in the refractory material, or add some inhibitors to reduce the bulging phenomenon of the refractory castable.
- Correct storage method
For large-scale construction and production of phosphoric acid and phosphate refractory castables by vibration molding and other methods, trapping is an effective and economical method, so it is widely used. After weighing the trapped material, add the coagulant and stir evenly, then add the remaining cementing agent, and continue to stir for 1 a 2 minutes before it can be used for molding. The trapping time is mainly determined by the chemical reaction speed between the cement and the metal contained in the refractory aggregate and powder, and the ambient temperature and other conditions.
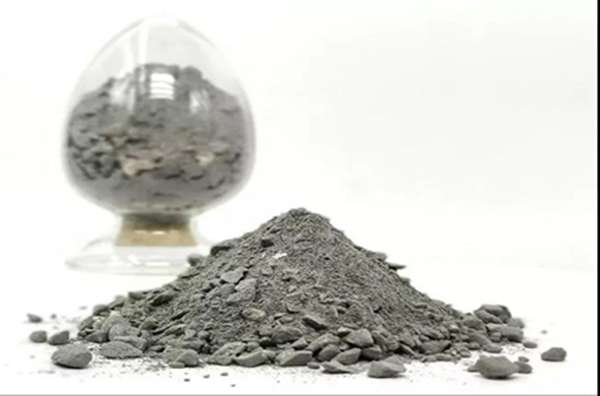
Phosphoric acid combined with refractory castable samples are stored indoors, outdoors, and in the standard curing room for castables. With the increase of storage time, the compressive strength at room temperature increases, but indoor storage is better than outdoor. Standard curing after 3 months The intensity tends to decrease slowly. When stored indoors, the compressive strength after burning is more than 10MPa higher than that in the open air. The compressive strength after burning stored in the standard curing room is also better than that in the open air. Samples stored in the open air may have low performance of refractory castables due to changes in cold and heat and cycles of dry and wet.
It should be pointed out that although the storage environment has some influence on the room temperature performance of phosphoric acid and phosphate refractory castables, it has little effect on the high temperature performance and does not affect the use. This is because the cemented phosphoric acid produced by adding coagulant before 200℃ Salt plays a leading role, while at high temperatures the ceramic bond formed plays a leading role. Por lo tanto, after the phosphoric acid and phosphate refractory castables with coagulant are hardened, the requirements for the storage location are not very strict. Phosphoric acid and phosphate refractory castables without accelerator can be stored only after heat treatment. Without heat treatment, there is no strength, and the heat treatment temperature is low, and it is easy to produce “deliquescent” phenomenon.
Although the binder in the phosphate castable does not react with the material itself at room temperature, it will slowly condense and harden due to temperature changes during storage or transportation or other environmental changes. If you need to store it for a long time, you can add it Retarders such as citric acid, tartaric acid, etc.. to extend the storage time.
When phosphoric acid and phosphate refractory castables are stored or under low-temperature use conditions, white crystals will precipitate on the surface of the refractory castables. After chemical and X-ray analysis, “white hair” is the crystallization of aluminum salt and calcium salt. In the case of high temperature or long-term heating, the aluminum salt and calcium salt are transformed into insoluble salts, and the “white hair” also disappears. This phenomenon has no effect on the performance of refractory castables under normal circumstances. Sin embargo, excessive precipitation will loosen the internal structure of the castable, reduce its strength, or even collapse, so care should be taken during storage or use.
WeChat
Escanea el código QR con wechat