Industrial kiln lining materials generally use refractory materials and insulation materials that are light in weight, high in strength and have good thermal insulation properties. This can reduce the weight of the kiln itself, save energy, and protect the environment. The construction of high-temp castable refractory should be adapted to local conditions. Depending on the type and location of the kiln, as well as the size of the maintenance area, the selection of construction methods is also different; choose a reasonable construction method.
Preparation work before construction of refractory castables
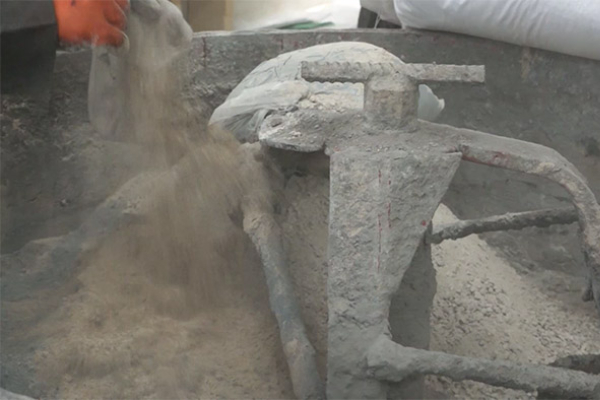
- Make a test block and figure out the amount of water added. Construction can only be carried out when the test block meets the design requirements;
- Check the corrosion of the steel shell, and remove rust from the steel plate shell surface in contact with the castable;
- Check whether the formwork is firmly supported. The surface of the formwork should be planned and painted with a layer of varnish to prevent the formwork from absorbing water and facilitate the removal of the formwork;
- For mixing the castables, a forced mixer must be used. All mixing tools must be clean. Add water and mix evenly. The materials can be unloaded and used only after they are completely uniform.
Construction steps of different parts of refractory castables
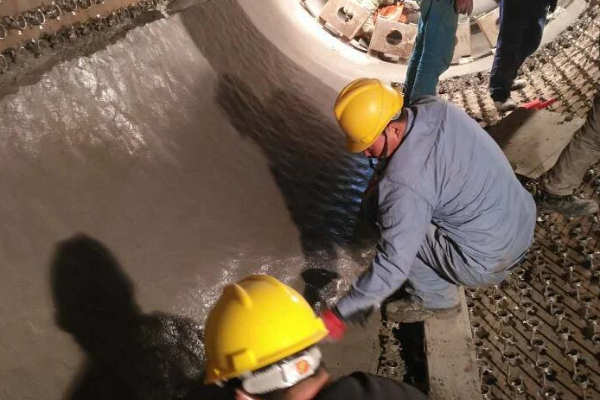
The packaging of Castane refractare is usually 25KG/50KG woven bags. When using, first take out the small bag of binding agent from each bag, then open it and pour the castables into the mixer. Dry mix for 3 to 5 minutes to mix evenly, and then add water to good castables and stir. The water must be clean water. The amount of water added should be based on the ratio provided by the manufacturer. The amount of water added should be accurately weighed. În general, the amount of water added is between 8% and 15%. The specific amount of water added is based on the On-site worker master experience and is added appropriately. The castable must be stirred evenly after adding water, usually about 3 minutes, and may be adjusted slightly depending on the site.
Construction steps of castable for insulation layer
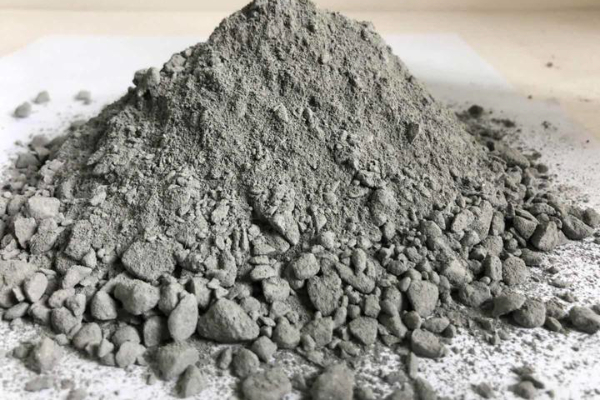
When pouring lightweight castables for the insulation layer, manual smearing, and pounding should be used to prevent particle separation and increase bulk density. When the thickness is greater than 100mm, the required thickness should be reached in one pour, otherwise, the layers will peel off and expansion joints should be left.
Construction steps of castables in high-temperature areas
When pouring heavy castables onto the fire surface, mechanical vibration should be used to ram it to eliminate the internal air. When tamping it manually, it should be even and dense, but it should not be calendered, because after calendering, the cement slurry will return upwards and the surface will be more dense. Dense, so the internal water is not easy to evaporate and cracks are easy to occur. To prevent water from evaporating too quickly, it should be covered after construction to keep it moist for maintenance.
Construction steps of corner transition section thermal insulation castables
When pouring the refractory castable in the corner transition section, a layer of plastic sheet should be laid to isolate the contact surface with the insulation blanket/cotton/board/brick to prevent the insulation brick/board/cotton from absorbing water. The refractory castable in the corner with difficult corners can be cast by the self-flowing method. The material has good fluidity, and the tamping time should not be too long to prevent the particles from separating and excessive moisture from returning upwards, which may cause cracks due to the evaporation of water. For some parts where the thickness of the construction is only a few centimeters, plastic should be used for coating. Before construction, pay attention to welding claw nails or tortoiseshell mesh on the repair parts. Fill the steel mesh with plastic so that there should be no gaps and it must be dense. The density cannot be increased. When applying, the plastic should be spread out and then smoothed with a wooden trowel until the surface is rough. In order to prevent cracks, the plastic surface can be smoothed with an iron trowel.
Precautions for high temp castable refractory construction
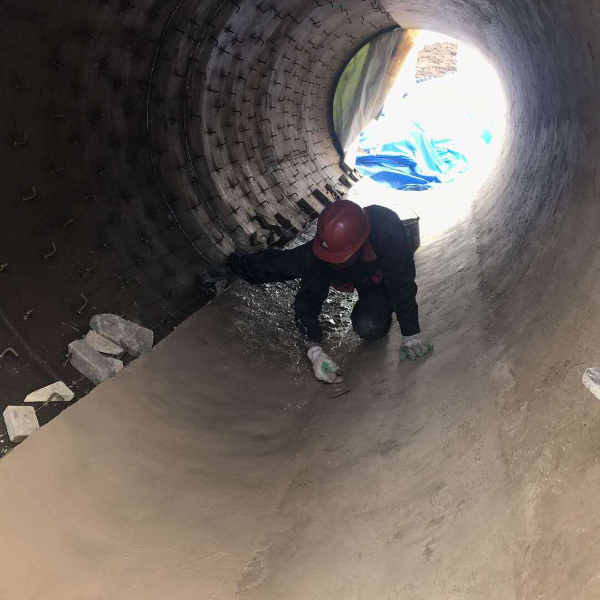
Use a vibrator or vibrator to vibrate, and tap every corner to ensure that no bubbles are discharged and no holes are produced. The castables should be prevented from bursting and peeling caused by rapid temperature rise during the oven process. and other phenomena; when mixing castables, all foreign matter in the mixer should be removed, clean water must be used, and the amount of water added should be strictly controlled. The mixed materials should be used up within 30 minutes.
WeChat
Scanați codul QR cu wechat