The ladle sliding nozzle is an important system for controlling steel production. If the system leaks steel during use, it will seriously restrict the stable and smooth production and threaten the safety of personnel and equipment. This paper analyzes the various factors that affect the leakage of the ladle refractory slide gate plate system.
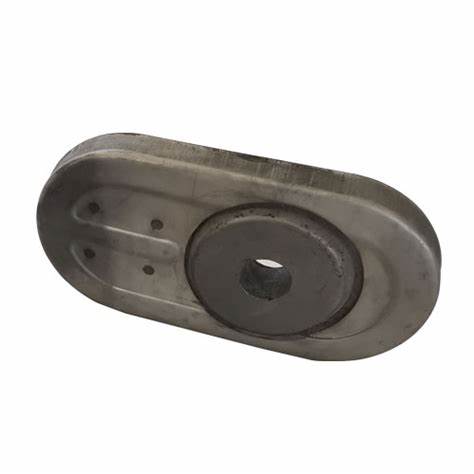
Analysis of the cause of steel leakage from ladle refractory slide gate plate
1. Slide gate plate leakage caused by mechanical reasons
Due to partial deformation of the bracket or the use of some springs, the clamping force on both sides is inconsistent, resulting in uneven surface pressure between the two slide bricks, one side is subject to greater force, and the other side is subject to less force. When the pressure of the molten steel exceeds the surface pressure on either side between the two slides, the molten steel will enter between the two slide surfaces, causing the slide to clamp the steel or leak steel.
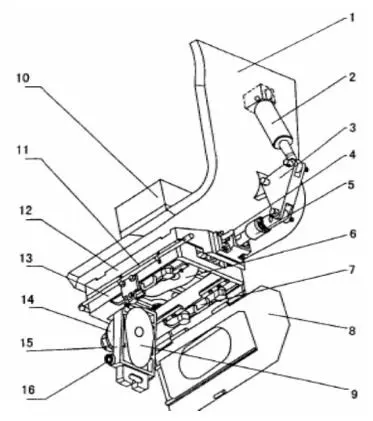
Schematic diagram of ladle slide gate plate: 1. Ladle wall; 2. Hydraulic cylinder; 3. Tripod; 4. Apoiar; 5. Pull rod; 6. Upper slide; 7. Pressing part; 8. Guard plate; 9. Lower slide; 10. Water inlet base brick; 11. Cold air pipe; 12. Square bottom plate; 13. Bracket; 14. Lower water inlet rotary sleeve; 15. Sliding trolley; 16. Trolley sliding wheel
Due to the falling of the slider or the loosening of the lower rotary sleeve, the pressure on the plate surface is insufficient, which can easily cause the plate surface to clamp the steel when the flow is controlled during the process. As the clamping of the plate surface intensifies, the gap between the slide plates gradually increases, and finally causes steel leakage. The falling of the slider causes the trolley to be unable to maintain horizontal operation during operation, resulting in gaps between the slide plates; when the lower rotary sleeve is loose, the lower slide plate will sink, resulting in gaps between the plate surfaces.
Steel leakage caused by ladle refractory slide gate plate material
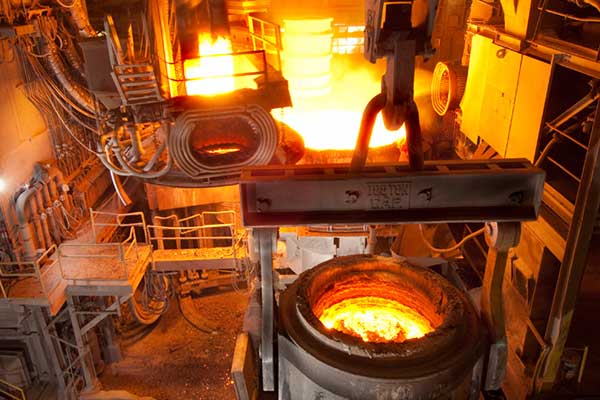
⑴ When pouring calcium-treated steel or high-manganese steel, the upper water inlet and the slide bricks have poor corrosion resistance, the water inlet and the slide expand quickly, and the effective stroke of the slide becomes smaller, which can easily cause the casting flow to be out of control or the plate surface to clamp the steel.
⑵ The upper and lower slide bricks have low high-temperature strength or poor resistance to “thermal shock”. Before the slide is poured, when the plate surface temperature (~350℃) starts to pour steel, the pouring hole suddenly contacts with the high-temperature molten steel (~1580℃) and is subjected to strong “thermal shock”. The outside of the pouring hole produces tensile stress exceeding the strength of the slide, forming radial cracks centered on the pouring hole. The appearance of cracks accelerates chemical erosion, and at the same time, chemical erosion reactions promote the formation and expansion of cracks (in severe cases, cracks will seep steel and leak steel).
⑶ The working surfaces of the upper and lower slides have poor high-temperature wear resistance (the slide material has poor oxidation resistance or the upper and lower slides have poor fit, the gap is too large, and the air inhaled during steel pouring causes the sliding surface to be oxidized and the strength is reduced), and the sliding surface is easy to “roughen”. After the molten steel is infiltrated, the “roughening” phenomenon is aggravated when pushing and pulling, and the friction resistance of the slide plate increases. In severe cases, steel leakage may occur between the sliding surfaces. The refractory material used for the slide plate contacts the high-temperature molten steel and slag during the process, and a series of chemical reactions occur, causing chemical erosion.
Steel leakage from ladle slide gate plate caused by improper operation
⑴During the assembly process, there are mainly the following reasons.
①After the upper nozzle is assembled, the lower nozzle must be baked to increase the strength between the upper nozzle and the seat brick, so as to avoid the upper nozzle being pressed into the upper slide plate during use without baking, resulting in a gap between the upper nozzle and the slide plate.
②When the mud pad is clamped on the upper slide plate, due to the difference in the visual value of the gap, the mud pad is too little or too much. When the mud pad is too little, there is a gap between the upper nozzle and the upper slide plate, which may cause steel leakage between the upper nozzle and the upper slide plate or steel clamping between the plate surfaces. This kind of steel leakage is more harmful. After leakage occurs in the early stage, it must be handled as soon as possible to avoid steel leakage on all sides in the later stage, burning the mechanism tie rod bolts and burning the mechanism; when the mud pad is too much, it is easy to cause the slide plate surface to break. During the pouring process, the molten steel will form steel clamps at the cracks, and the steel leakage will be caused after the water nozzle clamps are pulled multiple times to expand.
③ The high-temperature strength of the nozzle seat brick is low. When using a pneumatic pick to heat-change the upper nozzle brick of the ladle, the pneumatic pick head often damages the seat brick, causing the seat brick to expand in diameter and the gap between the seat brick and the upper nozzle brick to increase. When pouring molten steel, the molten steel forms a vortex at the seat brick. Under the influence of the molten steel scouring, the molten steel easily penetrates into the gap, causing steel leakage around the upper nozzle brick.
④ The lower nozzle brick bursts during use. When the lower nozzle brick is exposed to steel, it will have horizontal cracks under the influence of thermal stress. Under the action of molten steel pressure, the cracks gradually expand into cracks, and molten steel seeps out from them. In severe cases, the refractory material under the crack breaks due to its own gravity and the pressure of molten steel.
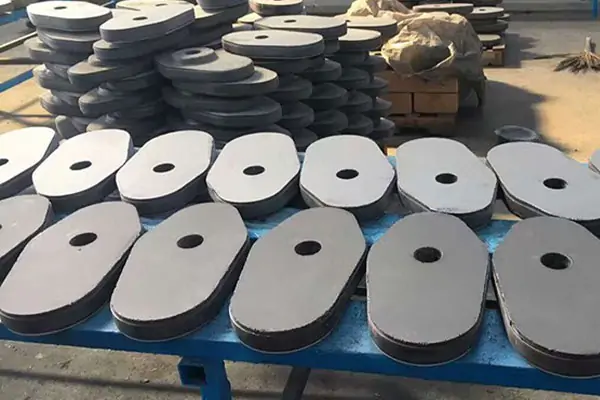
⑵ When the molten steel is poured, the sintered layer of the drainage sand is too thick. When the slide plate is fully opened, the sintered layer breaks and the steel appears when it flows down, causing the sliding trolley wheel to stick to the steel. During the pouring process, the sticking steel destroys the pressure balance of the mechanism, increases the gap on the plate surface, and causes steel leakage accidents.
⑶During the production process, due to the single-flow accident of the square billet, the steel drawing time was prolonged, the large ladle was semi-flow cast for a long time, and the sliding nozzle was frequently opened and closed, resulting in serious erosion of the plate surface. When the sliding nozzle was semi-flow cast, the lower slide brick was strongly scoured by the molten steel due to the interception of the molten steel. After a long time, grooves would be formed on the slide bricks, and horseshoe-shaped grooves would appear on the surface of the lower slide. When the ladle was closed, the molten steel condensed in the groove, resulting in steel sandwiched between the two slides. Além disso, the number of flow control times was relatively frequent, and the trend of steel sandwiching was relatively fast, which was prone to steel leakage accidents in the later stage of casting (Figure 2).
WeChat
Digitalize o código QR com wechat