O tijolo do bocal é feito de matérias-primas de alta pureza, formado por fundição vibratória e cozimento em baixa temperatura, e tem as vantagens de alta resistência térmica, resistência ao choque térmico, resistência à corrosão e resistência à erosão, e reparação térmica.
Introdução ao tijolo de bico
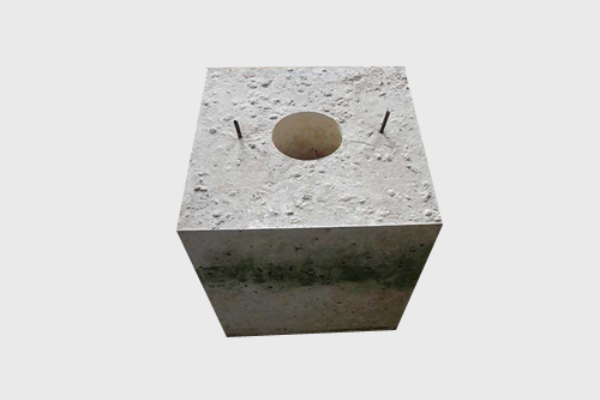
O tijolo do assento é um tijolo refratário construído na parte inferior do tambor de aço para fixar o tijolo do bocal. Seu formato é quadrado, então também é chamado de tijolo quadrado. O tijolo do assento é usado para fixar a posição da saída de água; é conveniente para desmontar e instalar a saída de água; ele suporta a extremidade inferior da haste do batente ao despejar; depois de derramar, certifique-se de que a haste do batente deslize ao longo da superfície do arco até a saída de água, e então corta o fluxo de injeção. Os materiais de tijolo do assento podem ser divididos em argila, alta alumina, ou alta alumina não queimada.
Especificação de tijolo de bico resistente ao fogo
Item | Índice | ||
Alumina fundida com cromo | Alumina Fundida | Espinélio de Corindo | |
Al2Ó3 % | ≥90 | ≥92 | ≥80 |
Al2Ó3+MgO % | / | / | ≥92 |
Cr2Ó3 % | ≥2 | / | / |
Densidade aparente g/cm3 | ≥3,0 | ≥2,95 | ≥2,95 |
Resistência ao esmagamento a frio MPa | ≥60 | ≥50 | ≥50 |
0.2Refratariedade MPa sob carga ℃ | ≥1700 | ≥1700 | ≥1700 |
Características do tijolo bocal
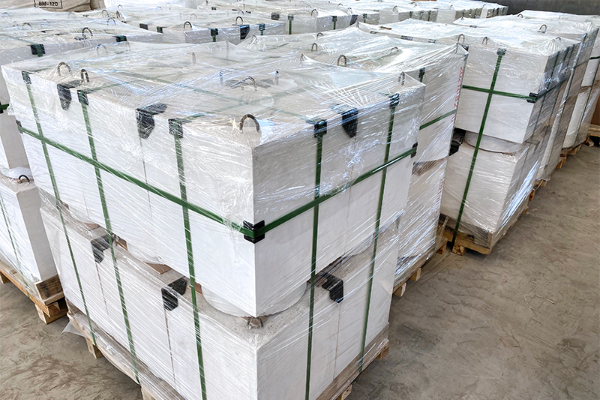
- Resistência à corrosão em alta temperatura
As panelas de refino têm requisitos muito rigorosos em termos de temperatura e tempo, e a temperatura máxima muitas vezes atinge acima 1750 ℃. Durante a operação de refino, a alcalinidade da escória tem grande influência na vida útil do material refratário. A alcalinidade da escória de refino em panela varia dentro da faixa de aproximadamente 0.6 para 0.4, então os materiais refratários são corroídos pela escória ácida, e escória alcalina com forte permeabilidade em altas temperaturas é danificada rapidamente. - Resistência ao desgaste em alta temperatura
Vários métodos de refino de panela usam agitação forçada, o que causa sério desgaste no bloco do bocal em altas temperaturas. - Resistência ao descascamento
Devido à operação intermitente, a temperatura vai mudar muito, que é propenso a fragmentação térmica e fragmentação estrutural, e as condições de uso são muito duras. Há uma grande lacuna entre o desempenho dos tijolos respiráveis revestidos de aço usados atualmente e o desempenho que deveriam ter. Por exemplo, em termos de resistência à corrosão em alta temperatura e resistência à lasca, especialmente a resistência à lasca precisa ser melhorada.
WeChat
Digitalize o código QR com wechat