Ceramic filter foam is a porous material with high-temperature characteristics. The pore size ranges from nanometer to micrometer, the porosity is between 20% そして 95%, and the operating temperature is from room temperature to 1600℃. Foam ceramic has a high specific area, high porosity, low density, 低熱伝導率, and selective permeability to liquid and gas media. It also has the excellent characteristics of high mechanical strength, good chemical stability at high temperatures, and good adsorption.
Ceramic filter foam production process
1. Organic (polymer) foam dipping process
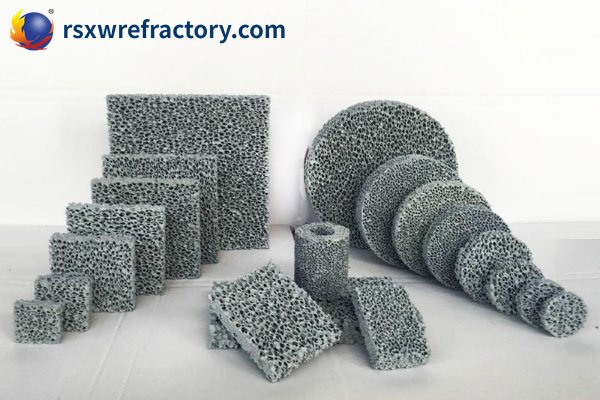
The ceramic slurry is impregnated with organic foam, and the organic foam is burned after drying. With the open-cell three-dimensional network skeleton structure of the organic foam, the prepared slurry is evenly coated on the organic foam network body, and the pores obtained after burning the organic foam are network-like. The key point lies in the selection of organic foam, and it is necessary to consider the pore size of the organic foam, the hydrophilicity and resilience of the foam, and the burning loss.
2 . Foaming process
The foaming process is to add organic or inorganic chemicals to the ceramic components, produce volatile gases through chemical reactions, generate foam, and then make foam ceramics through drying and sintering.
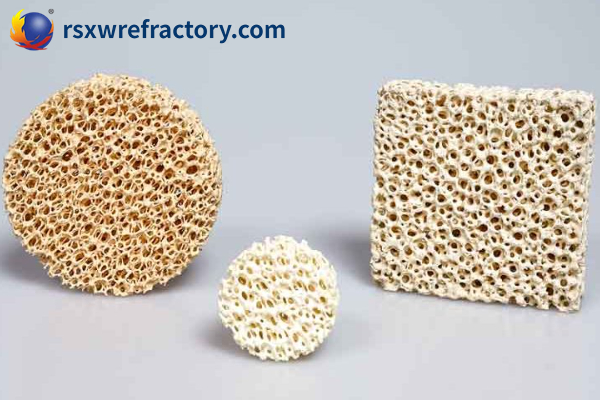
3. Adding pore-forming agent process
By adding pore-forming agents to the ceramic ingredients, the pore-forming agents occupy a certain space in the green body, and then after sintering, the pore-forming agents leave the matrix to form pores.
4. Sol-Gel Process
The sol-gel process is used to prepare foam ceramic materials. During the transformation of sol to gel, the viscosity of the system increases rapidly, thereby stabilizing the bubbles generated in the early stage and facilitating foaming. It is suitable for microporous ceramic materials with nanometer pore sizes and foam ceramic materials with high regularity.
5. Gel casting process
Using a non-porous mold and utilizing the chemical reaction inside the slurry or a small amount of additives to solidify the ceramic slurry in situ to form a green body, obtaining a green body with good microscopic uniformity and shape. This is a widely used molding method that can foam the suspension and enable the liquid foam to polymerize and solidify in situ.
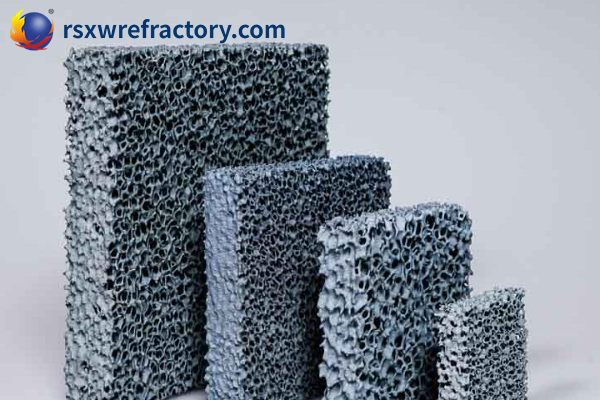
微信
wechatでQRコードをスキャン