In order to achieve the expected effect of mullite castables, in addition to reasonable design and good quality of the castables themselves, construction quality is also an important factor. daher, when making mullite refractory castables, it is necessary to follow the construction requirements of castables strictly.

Mullite refractory castable construction steps
Before construction, operators should master the key points and quality requirements of each process. After adding the materials to the mixer, dry mix and stir for 1 minute, and then add water. Too dry or too thin materials will affect the quality. It is fine if the materials can be kneaded into a ball and slurried. It is strictly forbidden to add water temporarily when pouring out of the tank. Once the amount of water is determined, it should not be changed easily to ensure that the density of each mixing is consistent. The recommended mixing time is 5 minutes. It is not good to mix too long or too short. The mixed castable should be poured immediately, and the parking time should not exceed 20 minutes. The castable should be laid evenly at the construction site, and the formwork, expansion plate, anchor brick, and other facilities should not be dislocated due to excessive force.
Generally, the material is vibrated with a vibrating rod after about 300mm of laying, and each part should be re-slurried. When pulling out the vibrating rod, it should be pulled out slowly to avoid leaving holes. If a part without vibration is found, it should be dug out and re-vibrated. After pouring, the surface of the casting body does not need to be smoothed. Natural curing for 2 Zu 3 Tage. During the curing period, it is strictly forbidden to step on or touch it. When the castable solidifies, the exhaust holes should be pierced in time to help remove water vapor. Demolding can be carried out only after confirming that it has sufficient strength.
Furnace lining baking
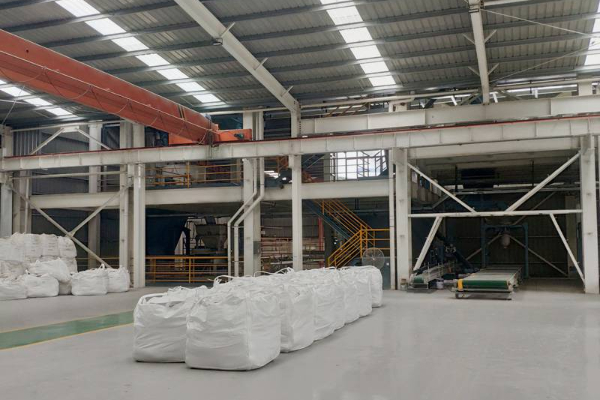
The quality of furnace lining pouring on site is certainly important, but the quality of furnace lining baking is directly related to the success or failure of castable application. The castable contains a large amount of free water and crystal water, which need to be fully removed through the furnace baking, which is an extremely important link for the longevity of the furnace lining. Since the volume and pressure increase sharply when the water turns into water vapor, if the baking temperature rises too fast, it will cause the furnace lining to crack, peel off or explode.
High-strength and high-aluminum mullite castables are dense and high-strength types with very low porosity, and it is not easy to remove water smoothly. Especially in the stage of removing a large amount of free water in the temperature range of 100-300 ℃, it is easy to cause excessive steam pressure and cause lining peeling or explosion accidents, so special attention should be paid and sufficient time should be given for removal. As the temperature continues to rise, free water and crystal water are continuously removed. When it reaches 500 ℃, the water content of the castable is only about 10% of the total water.
daher, the temperature of the castable should be slowly raised before 600 ℃, and there should be enough insulation time. After 1000℃, mullite begins to form in large quantities. After the primary crystal formation of mullite is basically completed at 1300℃, the mullite grains continue to grow, making the castable denser, increasing the bonding force, and increasing the strength. Based on the experience of the previous furnace baking, we assigned four work shifts to bake the furnace, record the temperature changes and fuel consumption of the heating section, soaking section, and preheating section every hour, and successfully completed the furnace baking task.
WeChat
Scannen Sie den QR-Code mit Wechat