Zircon brick was widely used in high-temperature industrial equipment such as glass kilns, non-ferrous metal smelting, and electric power due to their excellent high-temperature resistance, corrosion resistance, and thermal shock stability. Its production process is complex and rigorous, involving multiple steps, each of which requires strict control to ensure the quality and performance of the final product. This article will introduce the production process of zircon refractory bricks in detail, and focus on the advantages of zircon bricks produced by Rongsheng Refractory Materials Co., Ltd.
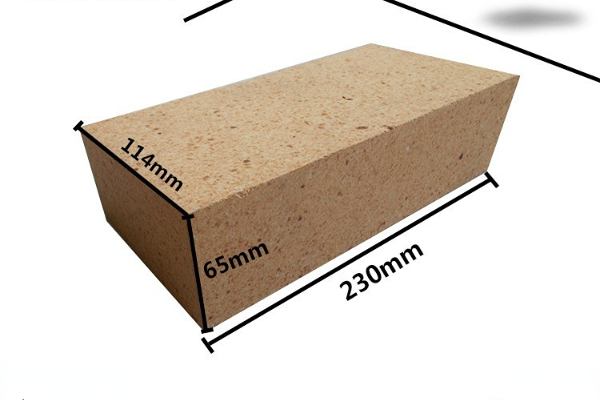
Zircon brick production process
The semi-dry production process can be used to manufacture clay-bonded zircon products. 2% plastic clay is added to zircon sand and zircon fine powder, and an electrolyte is used to adjust the properties of the clay. The clay is mixed and molded under a pressure of 127MPa (molding moisture is 4%). The green body is dried and fired at 1400℃.
When manufacturing pure zircon products, zircon fine powder can be surface activated. Zircon fine powder with a particle size of less than 0.03mm is mixed in a ratio of 1:1, and water or sulfite pulp waste liquid is added to prepare mud, which is mixed, molded (molding water content 4.5%), and sintered at 1450℃.
Select raw materials
The main raw materials of zircon refractory bricks are zircon and other refractory materials, such as zirconium oxide, alumina, dll.. These raw materials must be carefully screened and proportioned to ensure the bricks have the required refractory properties.
Mixing ingredients
The screened raw materials are mixed evenly in a certain ratio. Usually, a certain proportion of binder and anti-cracking additives are added to enhance the firmness and heat resistance of the bricks.
Molding and pressing
The mixed raw materials are placed in a mold and pressed into shape. The formed bricks need to have a certain shape and size to meet the subsequent sintering and use requirements.
Sintering treatment
The formed zircon brick needs to be sintered to make it have excellent refractory properties in a high-temperature environment. During the sintering process, the temperature and time need to be controlled to ensure that the structure and performance of the brick are well improved.
Quality inspection and packaging
After sintering, zircon bricks need to be inspected for quality to check whether their appearance and performance meet the requirements. Qualified products will be packaged into finished products and will be used in high-temperature environments such as kilns.
Advantages of zircon bricks from Rongsheng Refractory Company
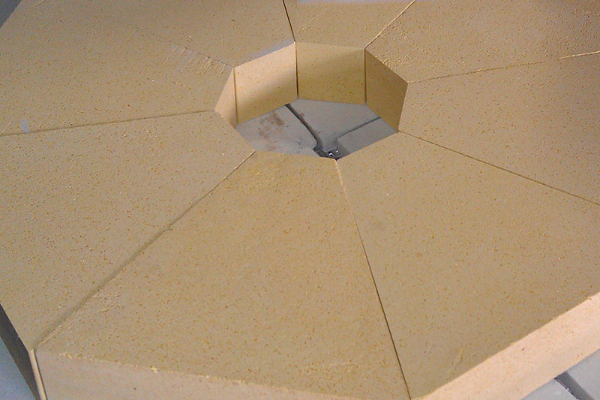
- High-purity materials: High-purity natural zircon ore is used to ensure that zircon bricks have a high zirconium dioxide content, providing excellent corrosion resistance, especially in high-temperature glass melting furnaces.
- Fine processing technology: Rongsheng uses advanced production equipment and fine processing technology to ensure that the dimensional accuracy and density of each zircon brick meet the standards. This not only improves the compressive strength of the brick but also greatly enhances its service life.
- Excellent thermal shock stability: Zircon bricks show extremely high thermal shock stability in high-temperature applications, can withstand rapid cooling and heating operating environments, and are suitable for a variety of high-temperature industrial furnaces.
- Customer customized services: According to the special needs of customers, Rongsheng can provide customized zircon brick products to meet the use requirements of different industrial furnaces and equipment.
- Reliable quality control: From raw material procurement to finished product inspection, each process is strictly controlled to ensure the stability and reliability of the product, which has been widely recognized by customers around the world.
Wechat wechat
Pindai Kode QR dengan WeChat