A submerged entry nozzle can protect the molten steel from oxidation when it flows into the crystallizer from the tundish, evenly distribute the molten steel into the crystallizer, and control the flow state of the molten steel in the crystallizer, with good slag resistance, anti-blocking, long service life, and low accident rate.
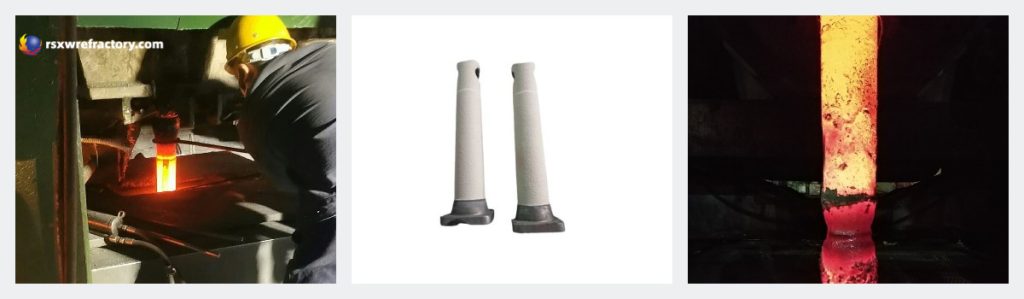
Technical parameter of erosion resistance submerged entry nozzle
Physical and chemical indicators:
Barang | Indeks | |||
JSK55 | JSK50 | JSK45 | JSK40 | |
Al2HAI3 % | ≥55 | ≥50 | ≥45 | ≥40 |
C % | ≥16 | ≥18 | ≥20 | ≥22 |
Flexural Strength MPa | ≥5.5 | ≥5.5 | ≥5.5 | ≥5 |
Apparent porosity % | ≤19 | ≤19 | ≤19 | ≤19 |
Kepadatan curah g/cm3 | ≥2.36 | ≥2.32 | ≥2.28 | ≥2.18 |
Slag Area:
Barang | Indeks | |||
Z75 | Z70 | Z65 | Z55 | |
ZrO2 % | ≥75 | ≥70 | ≥65 | ≥55 |
C % | ≥9 | ≥12 | ≥15 | ≥18 |
Apparent porosity % | ≤21 | ≤21 | ≤21 | ≤22 |
Kepadatan curah g/cm3 | ≥3.6 | ≥3.5 | ≥3.4 | ≥3.2 |
The main functions of the submerged nozzle
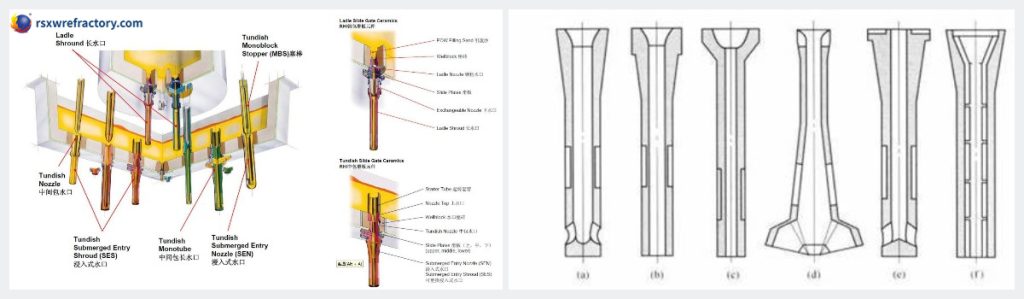
(1) Prevent secondary oxidation and nitridation of molten steel and splashing of molten steel;
(2) Regulate the flow state and injection speed of molten steel;
(3) Prevent non-metallic inclusions in protective slag from being drawn into molten steel, which plays an important role in promoting the floating of inclusions in molten steel;
(4) It has a decisive influence on the yield rate of side casting and the quality of the ingot.
The production process of submerged nozzle
The manufacturing process of the submerged nozzle is as follows: various raw materials are kneaded to form a uniformly mixed composite powder, which is isostatically pressed to form a green body of the required shape, which is sintered at high temperature to form a product with a certain strength, and then shaped to the required size. Finally, after inspection, it is packaged and shipped out.
What are the materials of submerged entry nozzles?
The materials of the submerged nozzle are fused silica, high alumina graphite, kuarsa, and zirconia
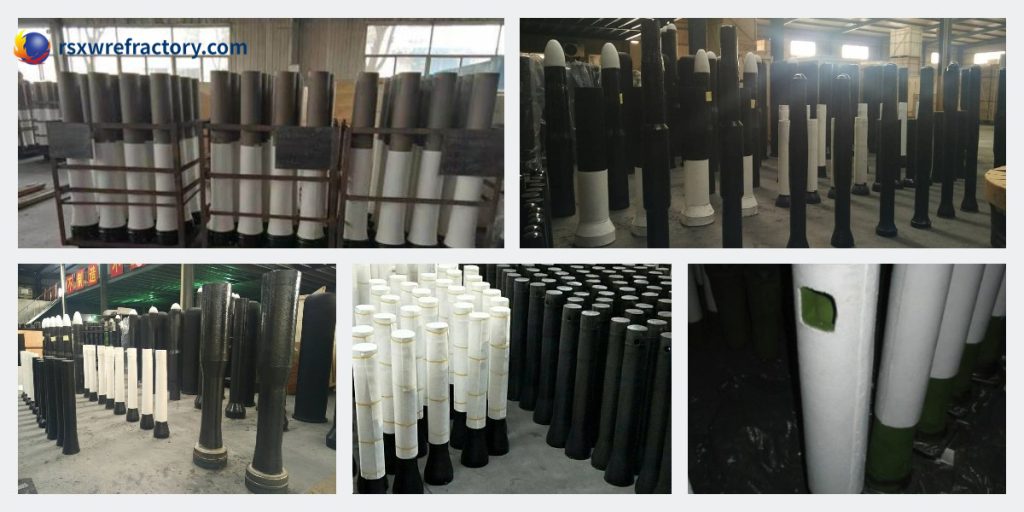
Wechat wechat
Pindai Kode QR dengan WeChat