Electric arc furnace steelmaking uses scrap steel or crude steel as the main solid material, and does not require a huge ironmaking and coking system; the raw materials can be used in a wide range, and are suitable for short-term, intermittent production in production scheduling: using electricity to melt (remelt) and heat it up, it is easy to obtain high temperatures, and the temperature adjustment is convenient and accurate, which is conducive to smelting various types of steel: the atmosphere in the furnace (oxidation, reduction, neutrality), vacuum, and pressure can be adjusted; the alloy yield is high, the composition is easy to adjust, the control range is narrow, the variety adaptability is wide, and the quality is good. It can smelt various types of high-quality steel and alloy steel with low P, S, and O; the equipment is relatively simple, the process flow is short, the footprint is small, the infrastructure cost is low, the production is fast, and pollution is easy to control: it consumes a lot of electricity, the productivity is lower than that of the converter, and the consumption of electrodes, refractory materials, dll.. is higher than other smelting methods.
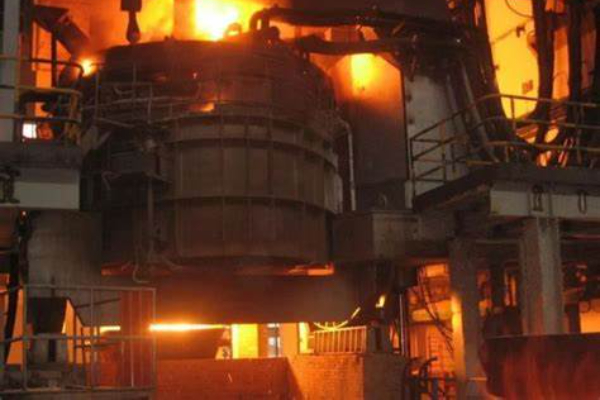
Steps of electric furnace steelmaking
- Adding materials
Adding raw materials such as molten iron or scrap steel to the electric furnace is the first step in the electric furnace steelmaking operation.
- Slag making
The operation of adjusting the composition, basicity, viscosity, and reactivity of slag in steel and iron production. For example, the air-blowing operation generates slag with sufficient fluidity and basicity, which can transfer enough oxygen to the metal surface, so as to reduce sulfur and phosphorus to below the upper limit of the planned steel grade and minimize the splashing and slag overflow during oxygen blowing.
- Slag discharge
During electric arc furnace steelmaking, slag discharge or slag removal is carried out according to different smelting conditions and purposes. For example, when using the single slag method, the oxidized slag must be removed at the end of oxidation; when using the double slag method to make reducing slag, the original oxidized slag must be completely discharged to prevent backflow, dll..
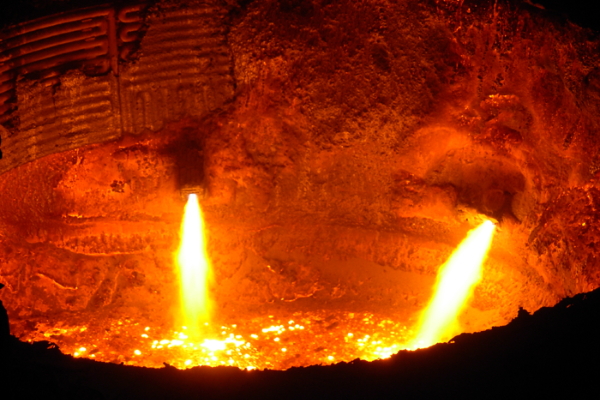
- Molten pool stirring
Energy is supplied to the molten metal pool to cause movement of the molten metal and slag to improve the kinetic conditions of the metallurgical reaction. Molten pool stirring can be achieved with the help of gas, machinery, electromagnetic induction, and other methods.
- Dephosphorization
A chemical reaction to reduce the phosphorus content in molten steel. Phosphorus is one of the harmful impurities in steel. Steel with a high phosphorus content is prone to brittle cracking when used at room temperature or lower temperatures, which is called “cold brittleness”. The higher the carbon content in the steel, the more severe the brittleness caused by phosphorus. Generally, the phosphorus content in ordinary steel is specified to be no more than 0.045%, and high-quality steel requires even less phosphorus.
- Bottom blowing of electric furnace Bottom blowing of electric furnace
The nozzle placed at the bottom of the furnace is used to blow N2, Ar, CO2, CO, CH4, 02, and other gases into the molten pool in the furnace according to the process requirements to accelerate melting and promote the metallurgical reaction process. The bottom-blowing process can shorten the smelting time, reduce power consumption, improve dephosphorization and desulfurization operations, increase the residual manganese content in steel, and increase the metal and alloy recovery rate. It can also make the composition and temperature of molten steel more uniform, thereby improving steel quality, reducing costs, and increasing productivity. - Melting Period
The melting period of steelmaking mainly refers to open-hearth and electric furnace steelmaking. The melting period of electric arc furnace steelmaking is from the start of power-on to the melting of all the steel and accompanying materials in the furnace, and the melting period of open-hearth steelmaking is from the addition of molten iron to the melting of all the materials. The task of the melting period is to melt and heat the materials as quickly as possible and to make the slag for the melting period.
- Oxidation period and decarburization period
The oxidation period of ordinary power electric arc furnace steelmaking usually refers to the process stage from melting and cleaning of furnace charge, sampling, and analysis to removing slag. Some people also believe that it starts from oxygen blowing or adding ore for decarburization. The main task of the oxidation period is to oxidize carbon and phosphorus in molten steel, remove gas and inclusions, and heat the molten steel evenly. Decarburization is an important operation process in the oxidation period. In order to ensure the purity of steel, the decarburization star is required to be greater than about 0.2%. With the development of refining technology outside the furnace, most of the oxidation refining of electric arc furnaces has been moved to ladles or refining furnaces. - Refining Period
The steelmaking process uses slag making and other methods to remove some elements and compounds that are harmful to the quality of steel from the molten steel by chemical reaction into the gas phase or discharge and float into the slag.
- Reduction period
In the steelmaking operation of an ordinary power electric furnace, the period from the end of gasification to steel tapping is usually called the reduction period. Its main task is to reduce slag for diffusion, deoxidation, desulfurization, control chemical composition, and adjust temperature. The reduction period has been canceled in high power and superpower electric furnace steelmaking operations. - Secondary refining
The steelmaking process of transferring the molten steel from the steelmaking furnace (converter, electric furnace, dll.) to another container for refining is also called secondary metallurgy. The steelmaking process is therefore divided into two steps: primary refining and refining. Primary refining: The charge is melted, dephosphorized, decarburized and alloyed in a furnace in an oxidizing atmosphere. Refining: The primary molten steel is degassed, deoxidized, desulfurized, inclusions are removed and the composition is fine-tuned in a container in a vacuum, inert gas or reducing atmosphere. The benefits of dividing steelmaking into two steps are: it can improve the quality of steel, shorten the smelting time in the steelmaking workshop, simplify the process and reduce production costs. There are many types of secondary refining, which can be roughly divided into two categories: secondary refining under normal pressure and secondary refining under vacuum. According to different treatment methods, it can be divided into ladle treatment type secondary refining and ladle refining type secondary refining.
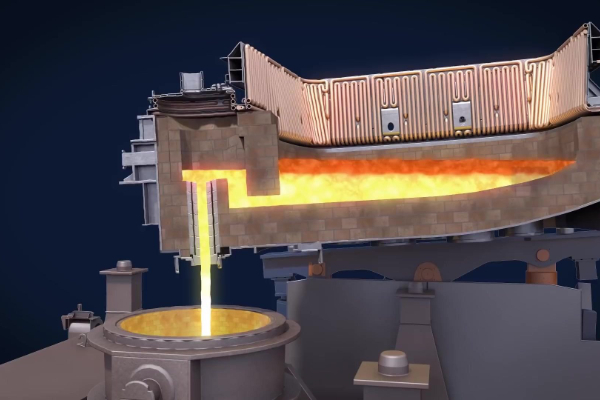
12. Molten steel stirring
The stirring of molten steel during the refining process outside the furnace. It makes the composition and temperature of the molten steel uniform and can promote metallurgical reactions. Most metallurgical reaction processes are phase interface reactions. The diffusion rate of reactants and products is the limiting link of these reactions. When the molten steel is in a static state, its metallurgical reaction rate is very slow. For example, it takes 30 to 60 minutes to desulfurize the static molten steel in the electric furnace; while it only takes 3 to 5 minutes to desulfurize the molten steel by stirring it in the furnace refining. When the molten steel is in a static state, the inclusions float up and are removed, and the removal speed is slow; when the molten steel is stirred, the removal rate of the inclusions increases exponentially and is related to the stirring intensity, type, characteristics and concentration of the inclusions.
13. Ladle wire feeding
The method of feeding deoxidation, desulfurization and fine-tuning powders covered with iron sheets, such as Ca-5i powder, into the ladle through a wire feeder, or directly feeding aluminum wire, carbon wire, dll.. to perform deep desulfurization, calcium treatment and fine-tune the carbon and aluminum components in the molten steel. It also has the function of cleaning the molten steel and improving the morphology of non-metallic inclusions.
Wechat wechat
Pindai Kode QR dengan WeChat