High alumina refractory bricks are a kind of alumina-silicate refractory material with a content of alumina oxide of more than 48%. It is calcined and formed by the raw material of bauxite or the material with a high content of AL2O3. High thermal stability, the refractoriness is more than 1770℃. Good slag resistance, used for the liner of masonry steel-making electric stoves, glass furnaces, and cement revolvers.
If the Al2O3 content of High alumina refractory brick is higher than 90%, it is called corundum brick. Due to different resources, the standards of different countries are not completely consistent. For example, in European countries, the lower limit of Al2O3 content for high alumina refractories is 42%. In China, Al2O3 content in high alumina brick is generally divided into three grades: Grade I – Al2O3 content > 75%; grade II – Al2O3 content is 60-75%; grade III – Al2O3 content is 48-60%.
High Alumina Refractory Brick Physical and Chemical Index
Artikal | Properties | |||||
RS-80 | RS-75 | RS-65 | RS-55 | RS-48 | ||
Al2O3(%) | 80 | ≥75 | ≥65 | ≥55 | ≥48 | |
Refractoriness(°C ) | ≥1790 | ≥1790 | ≥1790 | ≥1770 | ≥1750 | |
Bulk density(g/cm3) | 2.65 | 2.5 | 2.45 | 2.4 | 2.3 | |
Softening temperature under load(°C ) | 1530 | ≥1520 | ≥1500 | ≥1470 | ≥1420 | |
Reheating Linear changes Rate (%) | 1500°CX2H | 0.1 | 0.1 | 0.1 | 0.1 | 0.1 |
1450°CX2H | -0.4 | -0.4 | -0.4 | -0.4 | -0.4 | |
Apparent porosity (%) | 22 | ≤23 | ≤23 | ≤22 | ≤22 | |
Cold crushing strength (Mpa) | 55 | ≥50 | ≥45 | ≥40 | ≥35 |
Advantages of high alumina bricks
- Strong high-temperature resistance: The main component of high alumina bricks is alumina, so they have extremely high-temperature resistance and can usually withstand temperatures above 1500 degrees Celsius.
- Good corrosion resistance: High alumina bricks have strong resistance to chemical corrosion such as acid and alkali, so they are often used in environments in contact with corrosive media, such as the metallurgical industry, glass industry, itd.
- Strong thermal shock resistance: Due to its unique composition and structure, high alumina bricks have good thermal shock resistance and can withstand rapid changes in temperature.
- Low thermal conductivity: Compared with other refractory materials, high alumina bricks have low thermal conductivity, which makes them advantageous in some special industrial applications, such as thermal insulation layers inside high-temperature kilns.
- High strength: High alumina bricks have high compressive strength and can withstand large mechanical stress.
- Good volume stability: High alumina bricks are not prone to significant volume changes in high-temperature environments, which makes them widely used in industrial furnaces and other occasions.
- Strong wear resistance: High alumina bricks have high surface hardness and have strong resistance to the friction and impact of some particulate materials.
- Not easily contaminated: The surface of high alumina bricks is not easily contaminated, which makes them widely used in some industrial fields that require high product purity.
The difference between heavy high alumina bricks and lightweight high alumina bricks
1. Different production processes
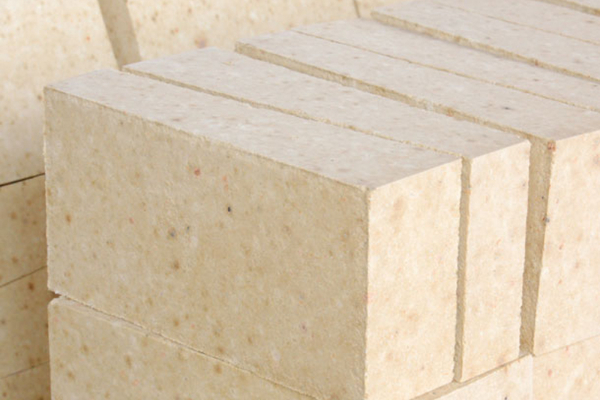
Heavy high-alumina bricks use high-alumina clinker as the main raw material, and soft clay and waste slurry as the binding agent. After high-pressure molding, drying, and high-temperature firing.
Lightweight high alumina bricks are made by mixing high alumina bauxite clinker with binder and foaming agent, then casting and finally firing at high temperature.
Both heavy high-alumina bricks and lightweight high-alumina bricks require high-temperature sintering, but one uses high-pressure molding, and the other uses casting molding.
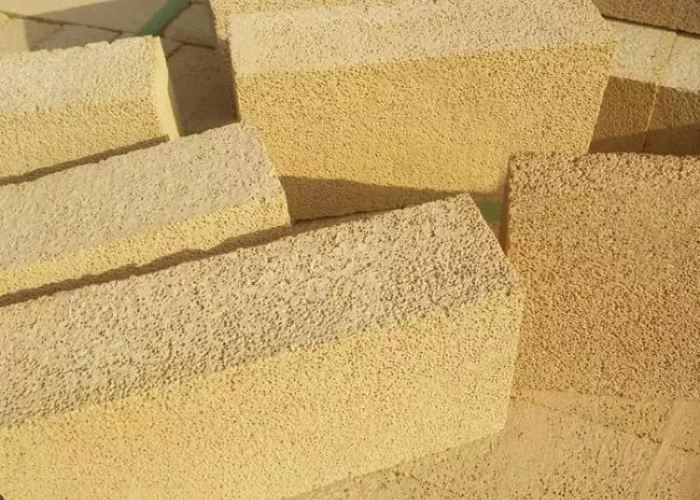
2. Different volume densities
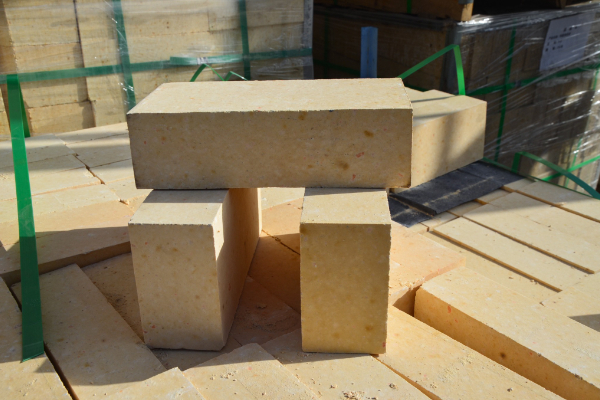
The volume density of heavy high alumina bricks is 2.3-2.65G/CM3, the volume density is dense, and the porosity is low, less than 23%.
The volume density of lightweight high-alumina bricks is 0.6-1.5G/CM3, the volume density is small, and the porosity is greater than 45%

3. Different refractory temperatures
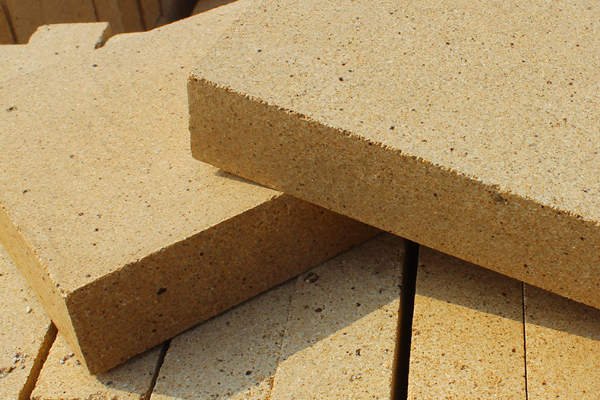
The fire-resistant temperature range of heavy-weight high-alumina bricks is 1580-1790 degrees, and they have good high-temperature resistance.
The service temperature of lightweight high-alumina bricks is lower than that of heavy high-alumina bricks, and the service temperature range is about 1350-1500 degrees.
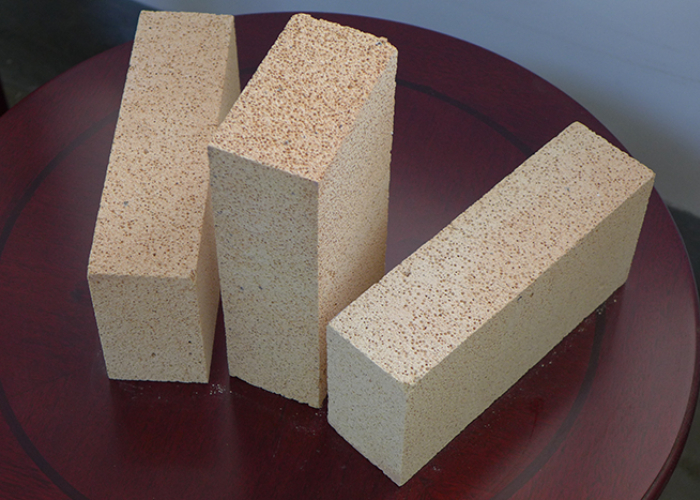
4. Different parts of use
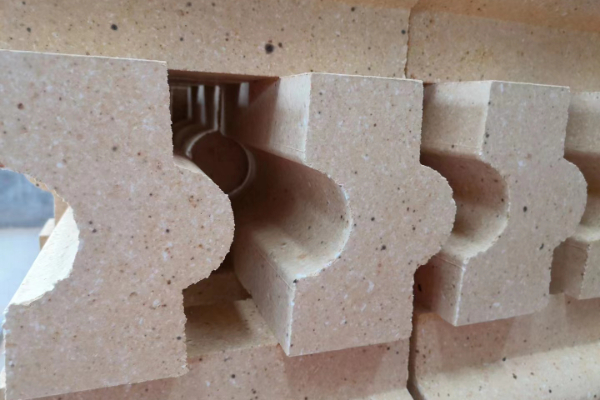
Heavy high alumina bricks have a higher operating temperature and can be used in parts that are in contact with slag. They have low porosity and strong anti-penetration ability.
Lightweight high-alumina bricks have low operating temperature and high porosity, cannot come into contact with flames or slag, and are mostly used for heat insulation layers.
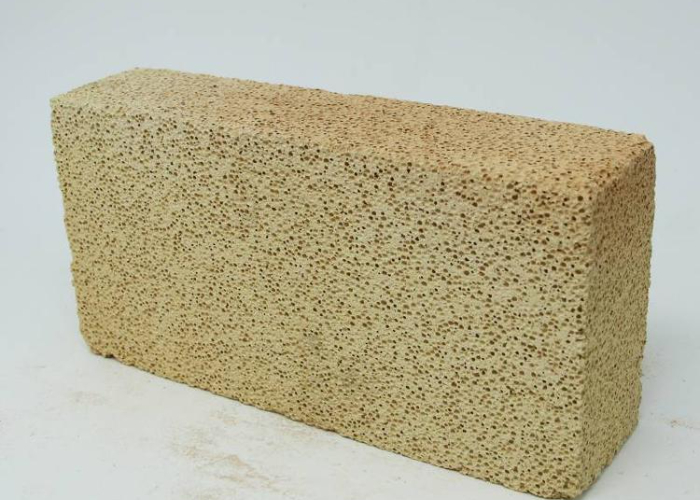
WeChat
Skenirajte QR kod pomoću wechata