Los castibles se hacen mezclando agregados y polvos refractarios, Agregar aglutinantes y aditivos, y amasar. La carpeta generalmente se usa en moldes es aluminada de cemento. La cantidad de cemento agregado puede afectar el rendimiento general del castible, fuerza de alta temperatura, resistencia a la corrosión, etc.. Los castibles bajos en cemento se realizan ajustando la fórmula durante el proceso de producción para reducir el contenido de CAO, Mejorar el rendimiento general del castible, y aumentar la vida útil del forro.
¿Qué es un castable con cemento bajo??
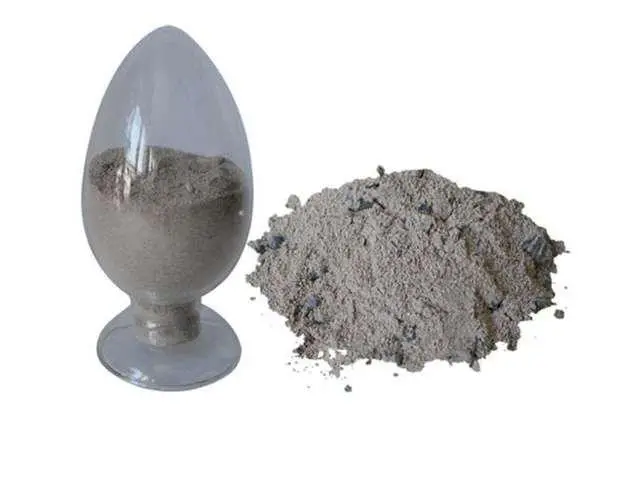
Bajo cemento Castable es un moldeo refractario con bajo contenido de cemento. Castables refractarios con aluminamiento de cemento como una carpeta y contenido de CAO menos que 2.5% se puede llamar castables de cemento bajo; Castables con un contenido de CAO de 1.0-2.5% se puede llamar Castables de cemento ultra-bajo. Castable de cemento bajo es un castable refractario de alto grado, que se llama cemento bajo debido al bajo contenido de CAO en el cemento.
Indicadores físicos y químicos de moldes de cemento bajo
Artículo | Arcilla | Alúmina alta | Corundo |
Al2O3 % | 45 | 75 | 92 |
SiO2 % | 50 | 12 | 5 |
cao % | <1.8 | <1.5 | <1.5 |
Densidad a Granel(110℃, 24H) gramos/cm3 | 2.3 | 2.6 | 3.0 |
Fuerza de aplastamiento en frío(110℃, 24H) MPA | 72 | 75 | 85 |
Tasa de cambio lineal(1350℃, 3H) % | ± 0.3 | ± 0.5 | ± 0.5 |
Temperatura de trabajo máxima ℃ | 1450 | 1600 | 1700 |
Se necesita agua % | 6.0~ 6.5 | 6.0~ 6.5 | 4~ 5 |
Características de castibles con cemento bajo
Tipos de castibles refractarios bajos en cemento
¿Cuáles son los castibles refractarios de bajo cemento comunes?? Los moldes de baja cemento se pueden hacer en moldes de alta aluminio con bajos cementos, Corundum Castables bajos en cemento, espinela de aluminio-magnesio castibles con cemento bajo, etc.. Según las materias primas refractarias seleccionadas.
Según el rendimiento de la construcción, Se puede dividir en moldes de bajo cemento y moldes de vibración de bajo cemento de tipo vibración.
Alcance de la aplicación de moldes de cemento bajo
Los moldes de cemento bajo son adecuados para revestimientos de hornos de calefacción, Varios hornos de tratamiento térmico, cubiertas de horno eléctrico, hornos verticales, hornos rotativos, Tapholes de alto horno, cucharón, cucharones de hierro, etc.; Los moldeses de cemento bajo auto-flujo son adecuados para revestimientos de componentes refractarios de alta temperatura con anclajes de metal, como el revestimiento exterior de los tubos de hornos calefactores refrigerados por agua, Revestimientos integrales de pistola de pulverización para la metalurgia de chorro, Reinicias de tubo de impregnación para dispositivos de desgasificación de aspiradora RH y DH, Componentes de suministro de gas de cucharón, y revestimientos de desgaste de alta temperatura de reactores de agrietamiento catalítico petroquímico, etc.; Se utilizan principalmente para la construcción de estructuras complejas., que puede mejorar en gran medida el efecto de uso general.
La composición de la materia prima de un fundible de cemento bajo
Agregados refractarios: principalmente incluir corundum, mullita, Corundum Mullite, espinela de aluminio-magnesio, etc..
Micropowder: como el micropowder de sílice, se usa para llenar los vacíos entre los agregados y mejorar la densidad de moldes.
Aglutinante: Por lo general, aluminando cemento o fosfato, que juega el papel de los agregados de unión y los micro polvos.
Dispersantes: tales como policarboxilato de alto peso molecular, se utilizan para reducir la viscosidad de los castibles de cemento y mejorar la fluidez.
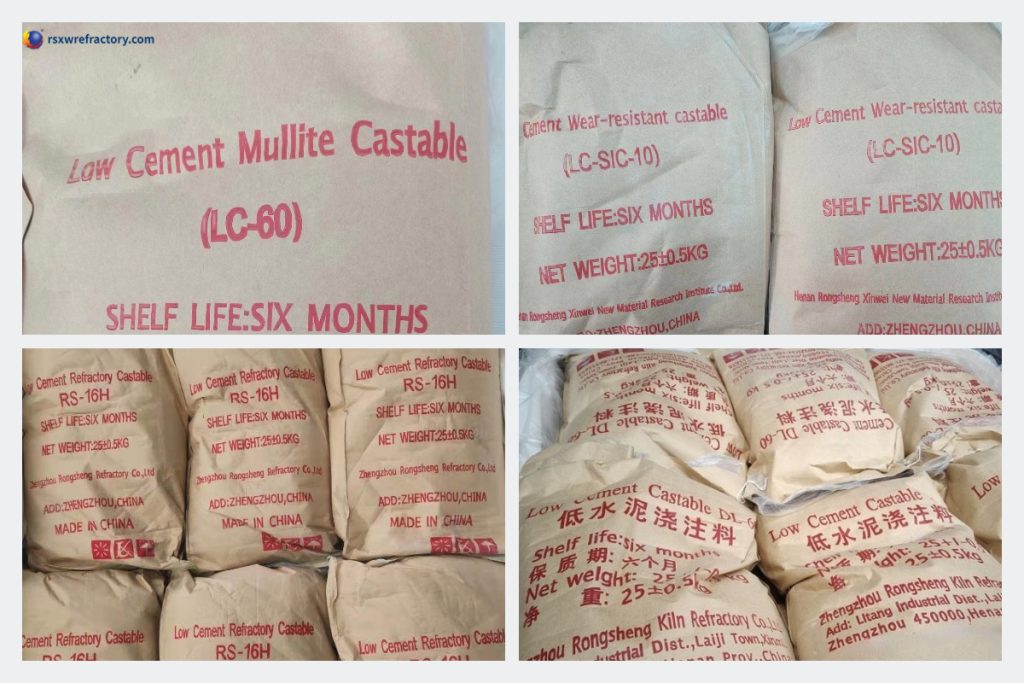
WeChat
Escanea el código QR con wechat