Magnesium iron spinel brick is an excellent product of a “chrome-free” cement kiln firing zone. It has excellent kiln skin hanging ability, good thermal shock stability, cement clinker erosion resistance, and a low thermal expansion rate. It has an excellent application effect in cement kiln firing zones.

Magnesia-iron spinel brick brief introduction
Magnesia-iron spinel bricks are made of high-purity magnesia sand and ferroalumina spinel as the main raw materials. The firing temperature and firing atmosphere are strictly controlled to make the product have good flexibility and thermal stability. The kiln lining performance and corrosion resistance are better than high-quality magnesia-chrome bricks. This product is an updated product for the lining of large dry cement rotary kilns.
Parameter of magnesium iron spinel brick
Buyum | Magnesia-iron spinel brick | High toughness magnesia-iron spinel brick |
MgO% ≥ | 85 | 88 |
Fe2O3% | 5-7.5 | 5-6 |
SiO2% ≤ | 2 | 1.5 |
Al2O3% ≤ | 3.0-5.0 | 4.0-7.0 |
apparent porosity% ≥ | 17 | 16 |
volume density g/cm3 ≥ | 3 | 2.9 |
cold compressive strength Mpa ≥ | 45 | 55 |
0.2MPa refractoriness under load, ℃ ≥ | 1600 | 1650 |
Thermal shock stability(1100℃~water cooling), times ≥ | 6 | 8 |
Thermal conductivity W/MK ≤ | 2.6 | 2.6 |
Thermal expansion % (1400℃) ≤ | 1.6 | 1.7 |
Characteristics of magnesia-iron spinel bricks
- High temperature stability: Magnesium iron spinel bricks have a high softening temperature (about 1750℃), and can be used for a long time in a high temperature environment without softening and deformation, so they are widely used in high temperature industrial equipment.
- Good corrosion resistance: Magnesium iron spinel bricks have good acid and alkali resistance and corrosion resistance, and can be used for a long time in harsh chemical environments without damage.
- High strength and hardness: Magnesium iron spinel bricks have high mechanical strength and hardness, and can withstand large loads and impact forces.
- Excellent thermal conductivity: Magnesium iron spinel bricks have excellent thermal conductivity and can quickly transfer heat, which is conducive to reducing the energy consumption of equipment and improving work efficiency.
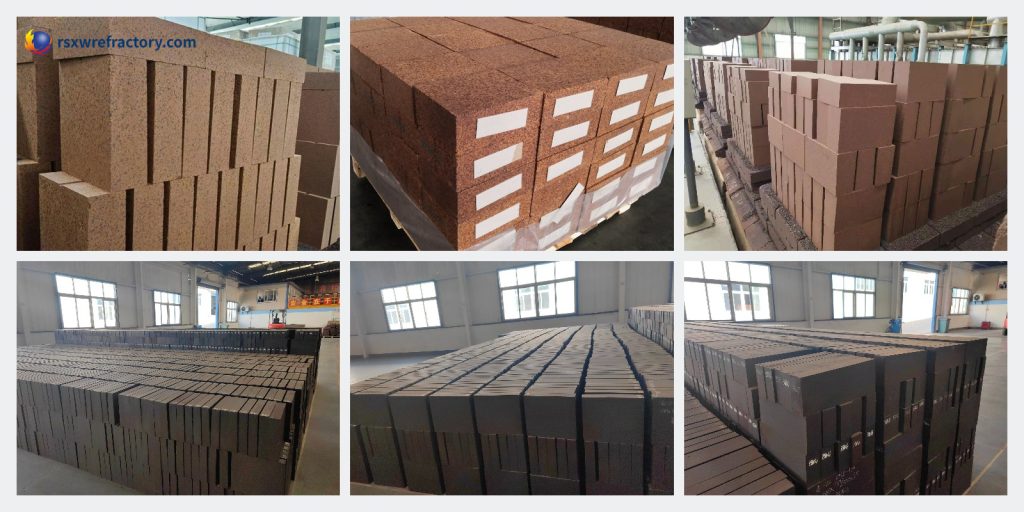
Application of magnesia-iron spinel refractory bricks
- Iron and steel smelting: Magnesium iron spinel bricks are often used in converters, electric furnaces, furnace linings and other parts in iron and steel smelting, and can withstand harsh conditions under high temperature and high pressure.
- Alumina smelting: Magnesium iron spinel bricks can be used in electrolytic cells and furnace walls in alumina smelting and can withstand erosion and thermal stress under high temperatures and high pressure.
- Glass manufacturing: Magnesium iron spinel bricks can be used in kiln linings, molten pools, and road plates of glass kilns. They have high-temperature stability and good corrosion resistance and can maintain the stability and purity of glass quality.
- Power industry: Magnesium iron spinel bricks can be used in boilers, hot blast furnaces, waste incinerators, and other equipment in the power industry, and can withstand harsh conditions under high temperatures and high pressure.
- Other fields: Magnesium iron spinel bricks can also be used in high-temperature processing equipment and reactors in the fields of chemical industry, metallurgy, building materials, etc., as well as in the production process of various refractory materials.
The production process of magnesia-iron spinel bricks
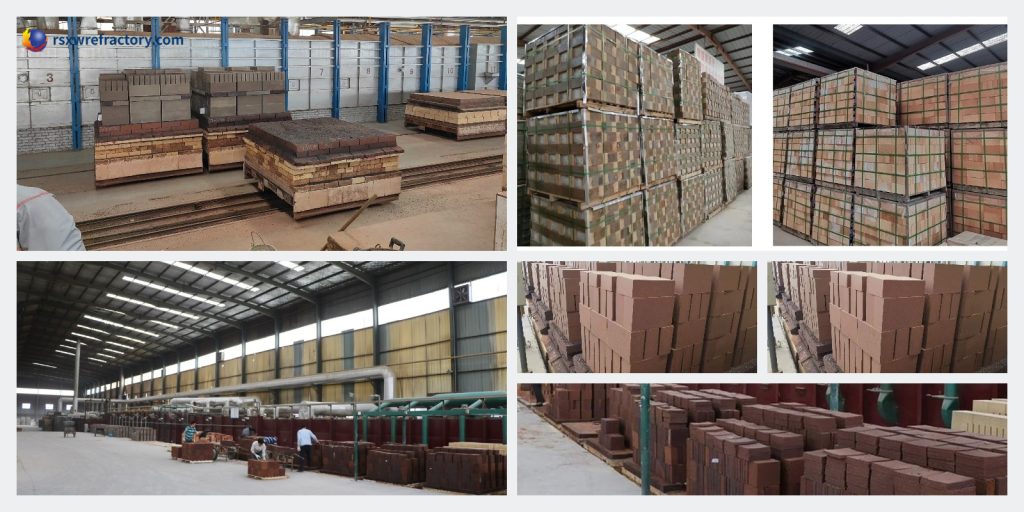
(1) Grind iron oxide into fine powder;
(2) Mix magnesium oxide and iron oxide in proportion by weight, wherein after magnesium oxide and iron oxide are mixed, 5%-15% of the total amount of binder water can be added and mixed evenly; the evenly mixed materials are compacted by a compactor and then put into a briquette machine to form balls; after the materials are formed into balls, they are dried and dehydrated at natural temperature for 2-4 days;
(3) Put the mixture or dried materials into a three-phase electric arc furnace and melt them at a temperature of 2800-3200 degrees for 9-11 hours;
(4) Cool the fired products at natural temperature for 6-7 days and break them into products.
WeChat
QR kodini wechat orqali skanerlang