Ceramic fiber modules (also known as aluminum silicate fiber modules) are composed of silicon dioxide and aluminum oxide. It does not contain asbestos and uses natural fiber as the main raw material. According to different specifications, the temperature resistance can reach 850℃-1350℃/24 hours. It is a high-refractory thermal insulation material. It is widely used in various industrial kilns and high-temperature environments; especially furnaces, kilns, boilers, and heaters.
What is a ceramic fiber module?
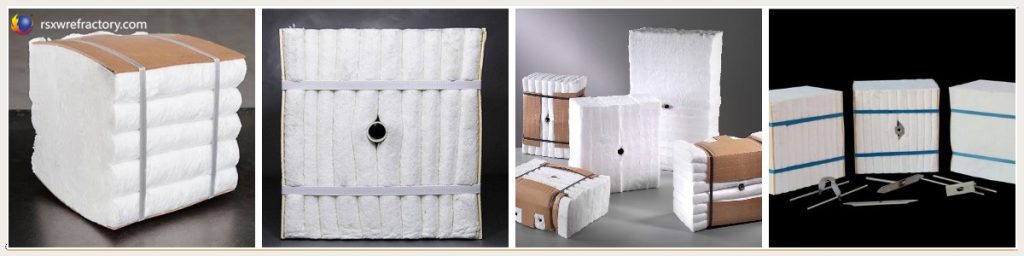
Ceramic fiber modules are pre-formed, rigid insulation components made from high-quality ceramic fibers. These modules are engineered to provide superior thermal insulation and withstand extreme temperatures, making them ideal for various industrial applications. The manufacturing process involves needle-punching the ceramic fibers and bonding them with a high-temperature adhesive, ensuring a strong and durable structure.
Physical and chemical indicators of aluminum silicate fiber blanket
tem Model | Seramika tolasi moduli | |||
1260 Saber block | 1400 Saber block | 1400 Unblock | 300*300*150, 200, 250 , 300 | |
Classification temperature(°C) | 1260 | 1400 | 1260 | 1400 |
Density ( Kg/m3) | 300*300*150, 200, 250, 300 | |||
Linear shrinkage(%) | (1100℃x 24 hrs)1.0 | (1200 ℃x 24 hrs) 1.0 | ( 1100 ℃ x 24 hrs ) 1.0 | (1200℃ x 24 hrs) 1.0 |
Thermal conductivity Kcal/mh °C(W/mK) ,ASTM C201(160 kg/m3) | ||||
Mean 400 °C | 0.09 | 0.09 | ||
Mean 600 °C | 0.14 | 0.14 | 0.14 | 0.14 |
Mean 800 °C | 0.21 | 0.21 | 0.2 | 0.2 |
Mean1000 °C | 0.26 | 0.28 | ||
Available size( mm/pc ) | 160, 192, 210 |
Features of aluminum silicate fiber modules
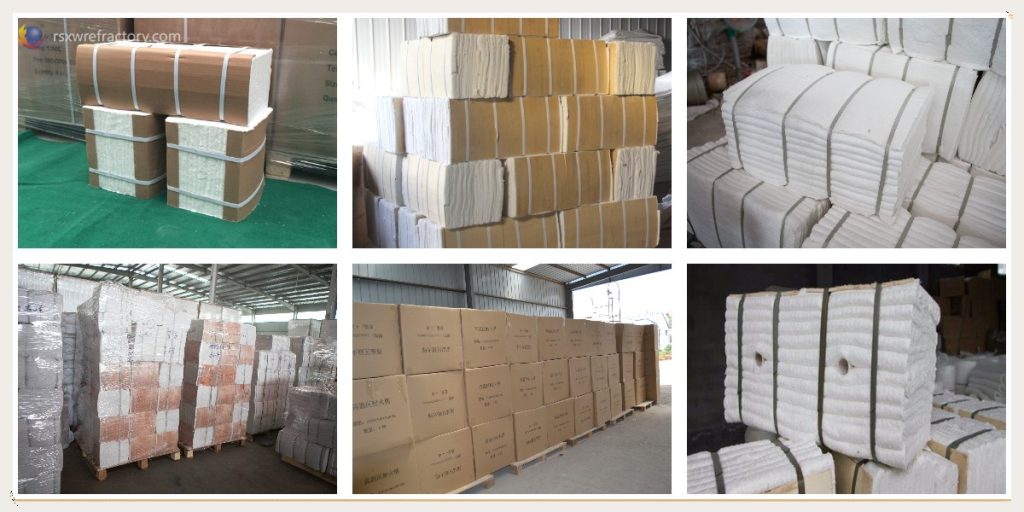
- Elastic fiber blanket can resist mechanical external forces
- The elasticity of the fiber blanket can compensate for the deformation of the furnace shell so that there is no gap between the components
- Due to its lightweight, it absorbs little heat when used as an insulation material.
- Low thermal conductivity brings a high energy-saving effect.
- It has the ability to resist any thermal shock.
- The lining does not need to be dried and cured, so it can be put into use immediately after installation.
- The anchoring system is away from the hot surface of the component so that the metal anchor is at a relatively low temperature
Application of ceramic fiber modules in the industry
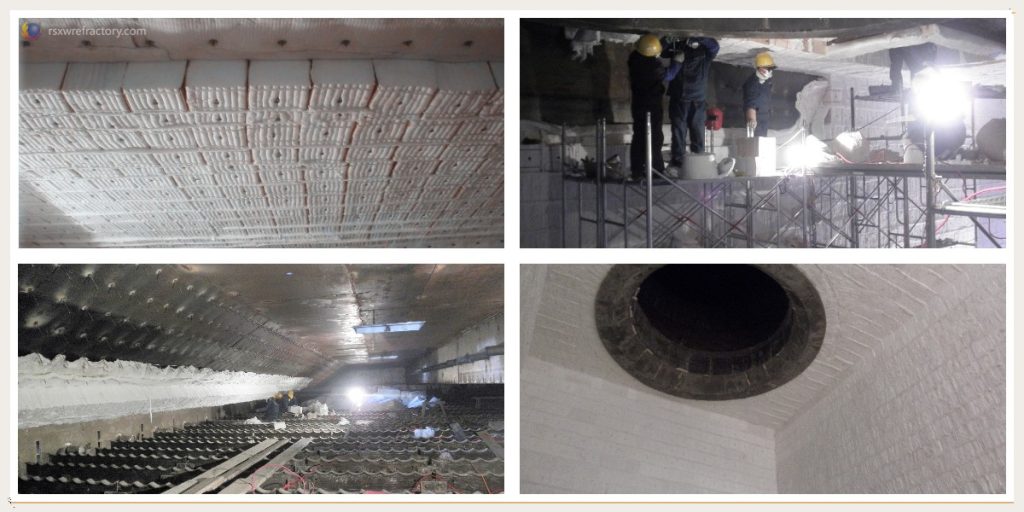
- Industrial Furnaces and Kilns: Ceramic fiber modules are widely used as thermal insulation linings for industrial furnaces and kilns, where they play a vital role in maintaining high temperatures, reducing energy consumption, and improving process efficiency.
- Boilers and Heaters: In boilers and heaters, ceramic fiber modules provide effective insulation, minimizing heat loss and optimizing energy use. Their ability to withstand high temperatures ensures reliable performance in these demanding applications.
- Petrochemical and Chemical Processing: Ceramic fiber modules are used in the petrochemical and chemical processing industries for thermal insulation of reactors, vessels, and pipelines, ensuring process temperature control and preventing heat-related incidents.
- Power Generation: Within the power generation industry, ceramic fiber modules improve energy efficiency by insulating boilers, turbines, and other high-temperature components, reducing heat losses and improving overall plant performance.
- Aerospace and Automotive: Ceramic fiber modules are used in the aerospace and automotive industries for high-temperature insulation of exhaust systems, jet engines, and other components that experience extreme heat.
Benefits of using aluminum silicate fiber modules
- Energy efficiency: By minimizing heat loss and optimizing energy use, aluminum silicate fiber modules contribute to significant energy savings in industrial operations. Their low thermal conductivity and low heat storage capacity reduce energy consumption and operating costs.
- Improve process efficiency: Ceramic fiber modules increase process efficiency by providing consistent and reliable temperature control. Their ability to withstand extreme temperatures ensures optimal process conditions, increasing productivity and reducing downtime.
- Enhanced safety: The use of high-temperature-resistant fiber modules improves the safety of industrial environments by preventing heat-related accidents and injuries. Its high-temperature resistance and excellent insulation properties minimize the risk of burns and fires, Creating a safer workplace for employees.
- Durability and longevity: Refractory ceramic fiber modules are extremely durable and long-lasting, providing cost-effective insulation solutions for industrial applications. Their wear resistance, as well as their ability to withstand harsh conditions, ensure a long service life and maximize Reduced maintenance requirements.
Installation method of aluminum silicate fiber module
Derust the furnace plate → Weld the module bolts onto the plate → Take out the module → Screw the module guide rod onto the small head of the screw → Put the module through the guide along the center hole and lean it against the furnace plate → Use a special wrench to tighten the nut onto the screw → Unscrew the guide rod → Install other modules in turn → Pull out the central plastic tube of the module → Remove the module strapping belt → Install the next row of folding modules
Installation requirements of aluminum silicate fiber modules
- The welding and placement of anchor nails should be accurate and the error should be strictly controlled:
- Install the backing layer first, then construct the fiber module:
- Install the furnace roof module first and then install the furnace wall:
- The furnace wall module should be installed from the bottom to the top:
- The modules are mostly arranged in the same direction, the “soldier row” arrangement. After installing a row of modules, the compensation blanket should be compressed and laid as required:
- The joints between the roof and the wall and between the walls should be compressed and laid with compensation blankets.
WeChat
QR kodini wechat orqali skanerlang