The main function of graphite electrodes is to conduct electrode conduction when smelting metals in electric arc furnaces. Due to the increasing proportion of steel smelted in electric arc furnaces globally, the use of electric arc furnaces to smelt steel plates and other secondary forming steels is the main item that consumes graphite electrodes. Bunga qo'chimcha, graphite electrodes are also used in smelting furnaces to melt non-ferrous metals and ceramics and in the waste recycling industry.
What is a graphite electrode nipple?
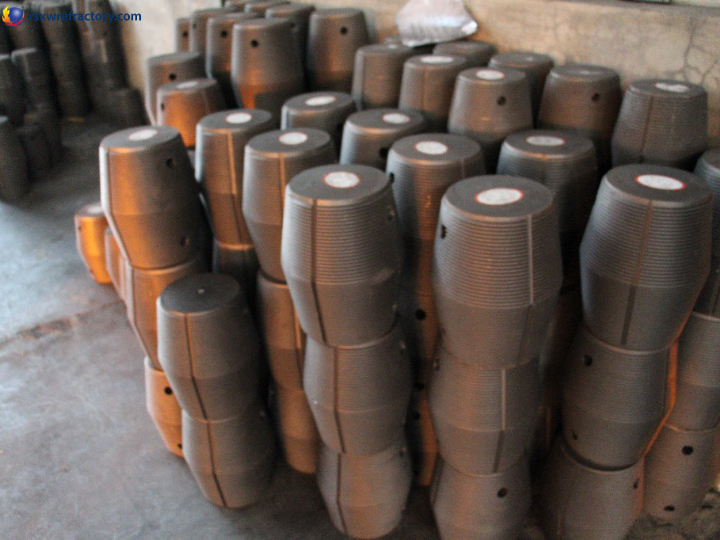
Graphite electrode joints are accessories for graphite electrodes. Graphite electrodes generally have higher requirements for joints. Joints generally have special production processes, which can be divided into (ordinary power graphite electrode joints, high-power graphite electrode joints, and ultra-high power graphite electrode joints). Graphite electrodes and nipples have the advantages of high strength, not easy to break, and good current passing.
Technical Parameter of Graphite Electrode
Graphite Electrode
Buyum | Nominal diameter mm | ||||||||||
75~130 | 150~225 | 250~300 | 350~450 | 500~800 | |||||||
Grade | Excellent | 一 | Ex | 一 | Ex | 一 | Ex | 一 | Ex | 一 | |
Resistivity μΩ·m ≤ | Electrode | 8.5 | 10.0 | 9.0 | 10.5 | 9.0 | 10.5 | 9.0 | 10.5 | 9.0 | 10.5 |
Connector | 8.0 | 8.0 | 8.0 | 8.0 | 8.0 | ||||||
Flexural strength MPa ≥ | Electrode | 10.0 | 10.0 | 8.0 | 7.0 | 6.5 | |||||
Connector | 15.0 | 15.0 | 15.0 | 15.0 | 15.0 | ||||||
Elastic Modulus GPa ≤ | Electrode | 9.3 | 9.3 | 9.3 | 9.3 | 9.3 | |||||
Connector | 14.0 | 14.0 | 14.0 | 14.0 | 14.0 | ||||||
Bulk density g/cm3 ≥ | Electrode | 1.58 | 1.53 | 1.53 | 1.53 | 1.52 | |||||
Connector | 1.70 | 1.70 | 1.70 | 1.70 | 1.70 | ||||||
Thermal expansion coefficient 10-6/Shum room temperature ~600℃ ≥ | Electrode | 2.9 | 2.9 | 2.9 | 2.9 | 2.9 | |||||
Connector | 2.7 | 2.7 | 2.8 | 2.8 | 2.8 | ||||||
Ash % ≤ | 0.5 | 0.5 | 0.5 | 0.5 | 0.5 |
High Power Graphite Electrodes
Buyum | Nominal diameter mm | |||
200~400 | 450~500 | 550~700 | ||
Resistivity μΩ·m ≤ | Electrode | 7.0 | 7.5 | 7.5 |
Connector | 6.3 | 6.3 | 6.3 | |
Flexural strength MPa ≥ | Electrode | 10.5 | 10.0 | 8.5 |
Connector | 17.0 | 17.0 | 17.0 | |
Elastic Modulus GPa ≤ | Electrode | 14.0 | 14.0 | 14.0 |
Connector | 16.0 | 16.0 | 16.0 | |
Katta zichlik g / sm3 ≥ | Electrode | 1.60 | 1.60 | 1.60 |
Connector | 1.72 | 1.72 | 1.72 | |
Thermal expansion coefficient 10-6/Shum Room temperature~600℃ ≥ | Electrode | 2.4 | 2.4 | 2.4 |
Connector | 2.2 | 2.2 | 2.2 | |
Ash % ≤ | 0.5 | 0.5 | 0.5 |
Ultra High Power Graphite Electrode
Buyum | Nominal diameter mm | ||||
300~400 | 450~500 | 550~650 | 700~800 | ||
Resistivity μΩ·m ≤ | Electrode | 6.2 | 6.3 | 6.0 | 5.8 |
Connector | 5.3 | 5.3 | 4.5 | 4.3 | |
Flexural strength MPa ≥ | Electrode | 10.5 | 10.5 | 10.0 | 10.0 |
Connector | 20.0 | 20.0 | 22.0 | 23.0 | |
Elastic Modulus GPa ≤ | Electrode | 14.0 | 14.0 | 1.66 | 14.0 |
Connector | 20.0 | 20.0 | 1.78 | 22.0 | |
Katta zichlik g / sm3 ≥ | Electrode | 1.67 | 1.66 | 1.66 | 1.68 |
Connector | 1.74 | 1.75 | 1.78 | 1.78 | |
Thermal expansion coefficient 10-6/Shum Room temperature~600℃ ≥ | Electrode | 1.5 | 1.5 | 1.5 | 1.5 |
Connector | 1.4 | 1.4 | 1.3 | 1.3 | |
Ash % ≤ | 0.5 | 0.5 | 0.5 | 0.5 |
Types of graphite electrodes
- Ordinary power graphite electrode: allows the use of lower current density, which is generally used in ordinary electric furnaces for steelmaking, silicon refining, yellow phosphorus refining, va hokazo.
- High-power graphite electrode: allows the use of a current density of 1.5-2 times that of ordinary power electrodes, mainly used in higher power steelmaking electric furnaces.
- Ultra-high power graphite electrode: allows the use of current density much higher than high power electrodes, has better conductivity, thermal stability, and mechanical strength, and is used in ultra-high power steelmaking electric furnaces.
What are the characteristics of graphite electrodes?
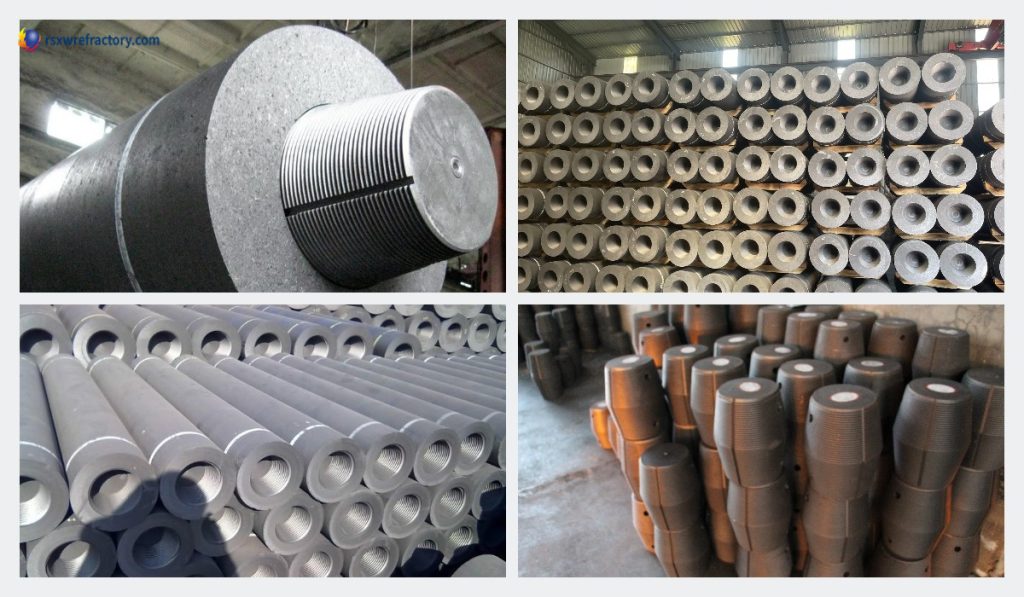
- Graphite electrodes have high conductivity. Graphite is a good conductor, and its conductivity is second only to metals, and in some aspects, it is even better than some metals. This characteristic makes graphite electrodes widely used in the power industry, electronics industry, and other fields.
- Graphite electrodes have high thermal stability. Graphite has an extremely high melting point and can maintain the stability of its structure and performance in high or even ultra-high-temperature environments, which makes graphite electrodes widely used in high-temperature industries such as high-temperature metallurgy and glass manufacturing.
- Graphite electrodes have strong chemical stability. Graphite has good corrosion resistance to most acids, alkalis, and organic solvents, which makes graphite electrodes widely used in the chemical industry, environmental protection industry, and other fields.
- Graphite electrodes are easy to process. Graphite is soft and easy to cut, carve, and shape, which makes graphite electrodes highly flexible and convenient in the manufacturing process.
The manufacturing process of furnace electrodes
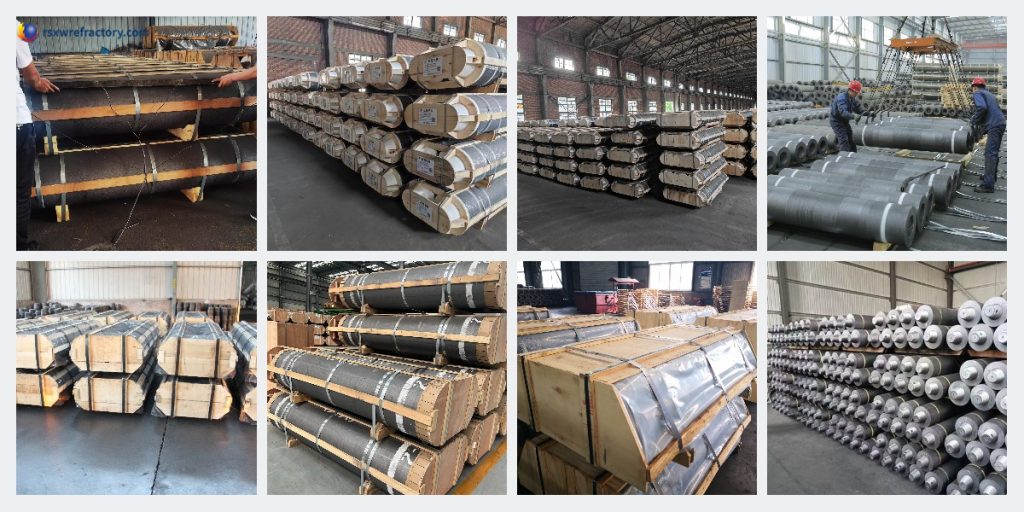
The manufacturing process of graphite electrodes mainly includes the steps of raw material selection, batching, kneading, molding, roasting, and graphitization.
First of all, raw material selection is the first step in the manufacture of graphite electrodes. The raw materials of graphite electrodes are mainly petroleum coke and pitch coke. The selection of these raw materials directly affects the performance and quality of graphite electrodes. Secondly, batching is the mixing of the selected raw materials in a certain proportion to achieve the expected performance. The batching process requires precise measurement and control to ensure the stable performance of graphite electrodes. Then, kneading is to mix and knead the prepared raw materials to form a uniform mixture. The kneading process has an important influence on the uniformity and density of graphite electrodes. Keyingisi, molding is to press the kneaded materials to form the preliminary shape of the graphite electrode. The molding process requires precise control of pressure and temperature to ensure the shape and size accuracy of graphite electrodes. Then, roasting is to heat treat the formed graphite electrode at a high temperature to make its structure more stable. The roasting process requires precise control of temperature and time to ensure the performance and quality of graphite electrodes. Nihoyat, graphitization is to graphitize the baked graphite electrode at high temperatures to make it more graphitized and have better performance. The graphitization process requires extremely high temperatures and long processing time and is the most critical step in the manufacture of graphite electrodes.
Uses of graphite electrodes
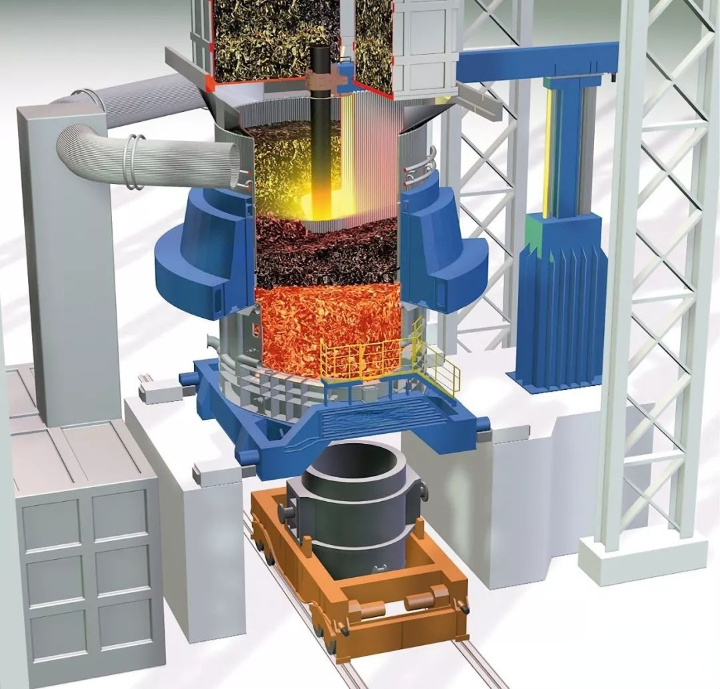
Graphite electrodes are important carbon products. They play a role in conducting electricity and transferring heat in production. They are consumables on smelting equipment such as arc steelmaking furnaces, ore-heat furnaces, electric furnaces, and resistance furnaces.
Graphite electrodes have a wide range of uses and are mainly used on various smelting equipment such as arc steelmaking furnaces, ore-heat furnaces, electric furnaces, and resistance furnaces. As a conductive material, graphite electrodes play a vital role in the smelting process.
In arc steelmaking furnaces, graphite electrodes generate high-temperature arcs through conduction to melt the charge and achieve the purpose of steelmaking. In ore-heat furnaces and electric furnaces, graphite electrodes are used to conduct current and generate heat energy to heat and melt the charge. Bunga qo'chimcha, graphite electrodes are also widely used in chemical, metallurgical, mechanical, electronic, and other industrial fields.
WeChat
QR kodini wechat orqali skanerlang