Zirconia corundum brick is a refractory brick made from industrial alumina and zircon sand as raw materials. According to the manufacturing process, zirconia corundum bricks can be divided into fused zirconium corundum bricks and sintered zirconia corundum bricks.
Introduction to fused zirconium corundum bricks
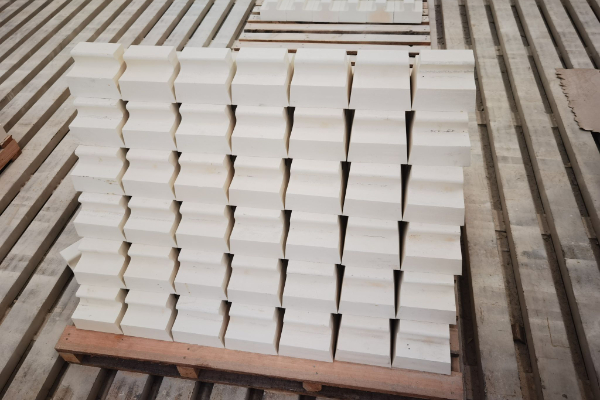
Fused zirconium corundum bricks are commonly known as tin bricks, also known as corundum-baddeleyite bricks. The main chemical components are Al2O3 50% to 70%, ZrO2 20% to 40%, and the rest is SiO2. The main mineral compositions are baddeleyite (ZrO2), korund (α-Al2O3), and glass phase. Baddeleyite crystallizes to form the backbone of the brick body. ZrO2 has a high melting point (2715°C) and good chemical stability. It has strong corrosion resistance to acidic and alkaline media, especially glass liquid.
Fused zirconium corundum brick uses
Fused zirconium corundum bricks, also called AZS bricks, are used in industrial furnaces such as glass melting furnaces. The parts used in glass melting furnaces are the upper pool walls, small furnace flats, small furnace stacks, tongue stack parapets, va hokazo.
Issues to consider when using fused zirconia corundum bricks
- Irregular Thermal Expansion: The expansion curve of fused zirconia corundum bricks exhibits an anomaly near 1000°C. This is due to a reversible crystal transformation of the internal ZrO2 crystals, resulting in significant volume changes. Shuning uchun, bricks containing ZrO2 should not be used in areas with rapid temperature fluctuations around 1000°C. During kiln firing, the temperature change between 900 to 1150°C should not exceed 15°C/h, and a smooth heating process is recommended. Some areas should be protected from cold air blowing, possibly using other bricks to prevent cracking.
- Shrinkage Cavities: During casting, shrinkage cavities often occur at the pouring spout. This area of the brick contains more pores and has a lower density. When constructing the glass melting tank wall, it’s important to orient the shrinkage cavities towards the inside of the furnace. If the pouring spout faces outward, it can lead to accidents where the molten glass leaks out when the brick is eroded to a very thin state. When used in the upper flame space of the tank furnace, the service life is long and there is no issue of glass leakage, so it is acceptable to have the pouring spout facing outward to extend the service life.
- Co-melting: When fused zirconia corundum bricks come into contact with clay bricks during construction, co-melting may occur at high temperatures around 1300°C. Shuning uchun, when selecting refractory materials, it is important to avoid stacking two types of refractory materials that are prone to co-melting. For instance, if silicon bricks are placed beneath fused zirconia corundum bricks, they are most susceptible to erosion from the fused zirconia corundum bricks.
Sintered zirconia corundum brick
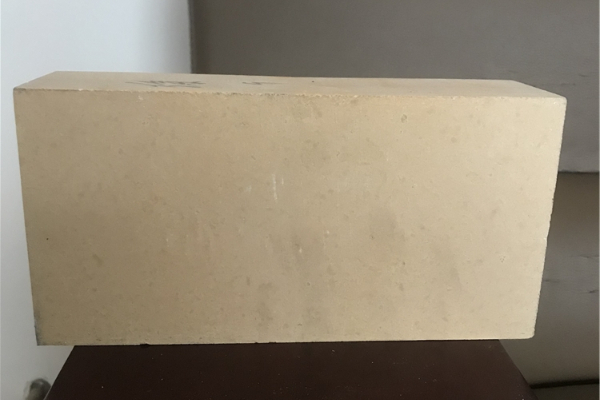
Sintered zirconia corundum brick, also known as ceramic-bonded alumina-silicon-zirconium brick, shares a similar chemical composition with fused zirconia corundum brick. However, it has the advantages of being carbon-free, having lower glass phase content, uniform structure, no shrinkage cavities, and good thermal shock resistance and erosion resistance compared to fused zirconia corundum brick.”
WeChat
QR kodini wechat orqali skanerlang