It is an important way to improve the service life of induction furnace lining maintenance and make appropriate repairs.
1) The damage to the lining of the induction furnace is roughly as follows:
(1) Thermal stress cracks, due to the thin thickness of the lining, the inner side is in contact with the high-temperature molten metal, and the outer side is close to the water-cooled coil, the temperature difference between the two sides is large, and the periodic cooling and heating cycles lead to thermal stress cracking of the lining;
(2) Corrosion by molten metal and slag, especially mechanical corrosion caused by electromagnetic stirring and overheating;
(3) Peeling, due to thermal stress or mechanical collision, vesaire., causing the lining material to fall off from the surface of the lining in block or flake form;
(4) Penetration and slagging.
2) Induction furnace maintenance
Maintenance and upkeep work is very important. It can not only detect various hidden dangers in time and avoid major accidents, but also ensure safe production, prolong service life, improve casting quality and reduce production costs. Daily production should pay attention to the following points:
(1) The raw materials added to the furnace for smelting must be clean. In order to prevent the furnace lining from being scratched during the feeding process, the size of the raw materials should not be too large, and do not directly hit the furnace bottom.
(2) During continuous smelting, do not discharge clean molten metal, and keep about 10% to protect the lining. Pay attention to prevent the smelting temperature from being too high and corroding the lining. The slag sticking to the lining should be cleaned in time, the size of the furnace body should be measured once a week, and problems should be dealt with in time.
(3) Regularly record relevant electrical parameters, cooling water temperature and shell temperature of key parts of the furnace body, and monitor the use of the furnace at any time.
(4) Observe the water pressure gauge, water temperature gauge and water flow condition and the aging degree of the hose every day, and deal with the problem in time.
(5) After the staged smelting is completed, the furnace body is covered with a thermal insulation cover to prevent the furnace body from cooling too fast and causing deep cracks. When the furnace body has large cracks or serious corrosion, remove the sintered layer of the damaged part and repair it by knotting.
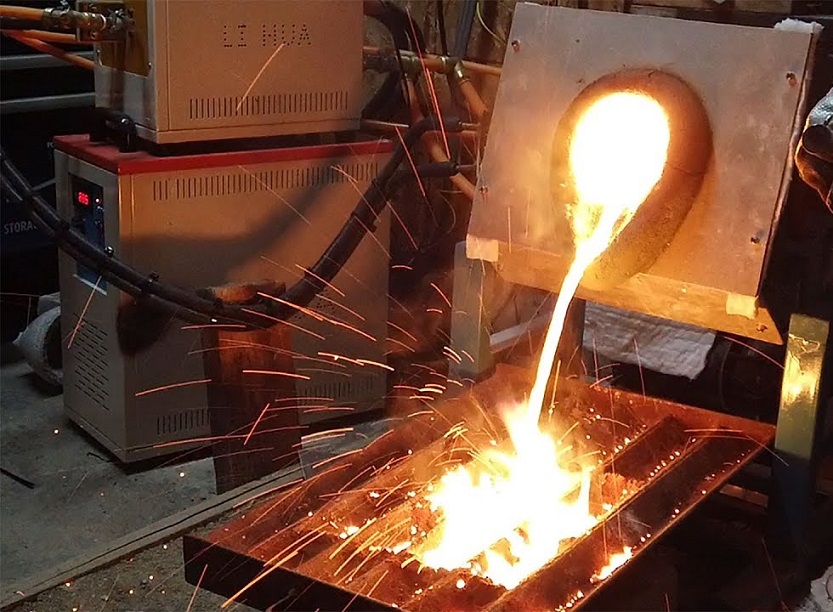
3) Induction furnace repair
Repairing the partially damaged furnace lining not only prolongs the service life of the induction furnace, but also saves a lot of refractory materials, insulation materials and insulating materials, reduces the electric energy consumed by the oven, and saves man-hours and furnace construction costs. Örneğin, a 0.5 t intermediate frequency induction furnace is lined with aluminum spinel to smelt aluminum-silicon-manganese alloy, and the general service life is about 50 heats. When using about 40 furnaces of magnesia repairing material combined with silicon micro-powder to smear and repair the cracks of the lining and the severely eroded parts, after repairing, use the residual heat of the furnace to dry naturally for 10 minutes, and use smelting and heating for baking and high-temperature treatment. The repair material was found to be firmly bonded to the original lining. After two repairs, the lining life can be increased to 90~100 heats.
There are many types of repair methods, which can be used flexibly depending on the damage of the lining. There are roughly minor repairs, medium repairs, and major repairs. Cracks smaller than 1 mm can be left unrepaired. Cracks larger than 1 mm, especially those in the horizontal direction, must be repaired. After sieving the refractory material with boric acid, it can be filled with tools such as iron wire. Add water glass wet mixed sand on the repaired surface and smooth it. If there is a small range of erosion or damage, after removing the slag and residual iron, coat with water glass, and then tap and repair with the refractory mixed with water glass, or repair with the amorphous refractory containing Al₂O₃.
There are the following types of middle school:
(1) Hot repair method: commonly used in the furnace mouth, remove the loose original lining, clean it up, put the mold with suitable height and diameter on the slope of the bowl mouth, add bulk refractory material to tamp it, and send it first Low-voltage electricity for 3~4 hours, and then send high-voltage electrification materials.
(2) Cold repair method: Repair the furnace after cooling. There may be the following situations:
① For local damage with a relatively large area, remove the compensated oxide layer, put on a suitable crucible mold, fill in the original lining material and ram it, and bake it according to the oven curve of the old furnace; ② The entire furnace lining becomes thinner, First remove and flatten the oxide layer of the inner lining, put the ramming material at the bottom for tamping, then put it into the whole furnace, and then put the ramming material for tamping in batches, and press the new furnace after completion; To repair the “foot” part, scratch the original sintered layer (it is not necessary to remove all of it), put it into the crucible, and then add material to tamp it.
(3) Repair of the induction coil: clean the broken parts, and then evenly apply insulating cement. Genel olarak, the cement is added with refractory cement, which is a hydraulic substance. It dries too slowly, and it is easy to flow and deform. If it dries too quickly, it cannot be repaired. To master the initial setting and final setting time of cement.
The middle repair is simple and easy to operate, and can be carried out repeatedly and continuously. If the intermediate repair is repeated indefinitely, it is possible to achieve zero emission of refractory materials for induction furnaces, energy saving and environmental protection. It is recommended that the induction furnace be repaired by gunning technology, and the efficiency will be better.
The so-called overhaul means removing all refractory materials and rebuilding the furnace.
The refractory materials for coreless induction furnaces are selected according to the type of smelted metal, the properties of slag, furnace capacity, operating conditions and other factors. Acidic quartz refractory for cast iron and some cast steel, copper-aluminum and alloy melting furnaces. It requires high purity (w(SiO₂)> 99%), large crystal particles, reasonable particle ratio of ramming material, and suitable sintering agent. The inner lining is knotted and firmed. High alumina bauxite and corundum spinel neutral and magnesia and magnesia spinel basic refractories for cast steel and some cast iron, copper aluminum and alloys, nickel melting furnaces, dry ramming or prefabricated Composite lining for crucibles. According to the size of the furnace capacity and the conditions of use. Careful maintenance of the furnace and timely repair of damaged parts are an important way to prolong the service life of the induction furnace. Gunning technology should be adopted, mechanized operation, repeated gunning, and strive to achieve zero discharge of refractory materials after use, and develop in the direction of permanent lining.
WeChat
QR Kodunu wechat ile tarayın