Glass kilns are one of the core equipment of glass production enterprises. Their operating stability and service life directly affect production efficiency, product quality, and the operating costs of enterprises. Generally speaking, the design life of a glass kiln is 5 to 10 years, but the actual service life often varies due to many factors. So, what are the key factors that affect the service life of glass furnaces? This article will conduct a detailed analysis from multiple perspectives, such as design, materials, construction, operation, and maintenance.
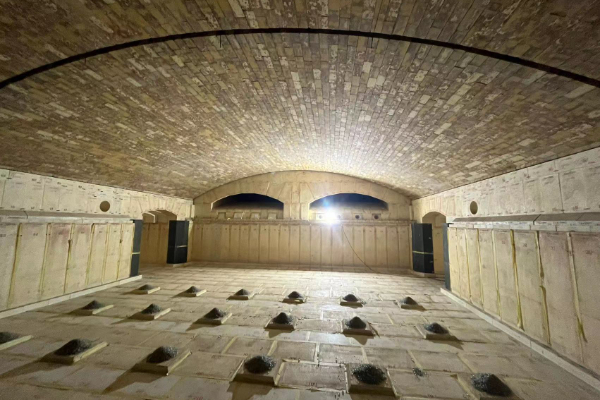
Glass furnace design quality
A good design is half of the success of a project. The design of a glass kiln is a systematic project involving many disciplines such as mechanical calculation, thermal calculation, fluid mechanics, refractory materials, thermal energy instrumentation, etc. The complete kiln design includes; process layout, kiln size, energy distribution, flame space aspect ratio, liquid flow and air flow, comprehensive configuration of refractory materials, steel structure, control system, combustion system, molding equipment, process control, kiln masonry, installation, baking, heat protection, environmental protection and other related technologies.
Selection of refractory materials
The selection of refractory materials is the top priority to ensure the service life of the kiln. The reasonable selection of refractory materials must first be familiar with the characteristics of various refractory materials, and select high-quality and reasonable materials according to the characteristics of the products and the characteristics of each part of the kiln. In particular, the selection of fused zirconium corundum brick manufacturers and the selection of materials play a vital role in the service life of the glass kiln. The selection of fused bricks is mainly based on regular manufacturers. Whether the company itself has the equipment and ability to detect and inspect, whether the products produced can meet the national standards and meet the requirements of various indicators of kiln design, especially the selection of materials for important parts such as the feeding port corners, pool walls, kiln sills, bubbles, flow holes, and large arches of the glass kiln, and the reasonable matching of AZS-33#, 36#, and 41# materials are all key factors affecting the life of the kiln.
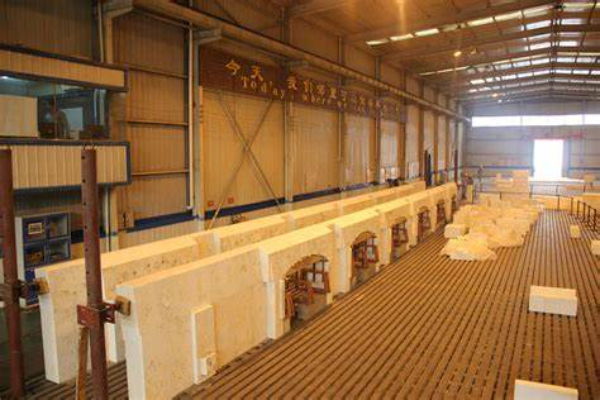
Glass kiln construction quality
Whether the refractory masonry slurry is full, how pure the slurry is, whether the size of the masonry brick joints meets the design requirements, whether the operation of the transition layer between different materials is correct, whether the production and erection of the kiln arch are reasonable, and whether the extension line of the brick joint formed by each arch brick of the furnace cover passes through the center of the circle (if the extension line of the brick joint formed by each arch brick of the furnace cover cannot pass through the center of the circle, the cracks of the furnace cover will be uneven during kiln baking, and the cracks will be concentrated in a certain place, forming a larger gap), all of these will affect the overall life of the kiln. In particular, when laying the fused zirconium corundum brick body, pay attention to its thermal expansion coefficient, reserve expansion gaps in advance, and avoid cracking due to the expansion and extrusion of the brick body during kiln baking!
Kiln baking
Whether the heating curve of kiln baking is reasonable will affect the life of the kiln because the glass kiln is a combination of various refractory materials, and the expansion coefficients of various refractory materials are different, and the expansion coefficients of some refractory materials are nonlinear. It has crystal lattice rearrangement, which causes abnormal volume changes of refractory materials. Therefore, the formulation of the heating curve of kiln baking should consider the special performance and characteristics of each refractory material.
The stability of the glass furnace’s temperature field is very important when baking the kiln. It not only means that the temperature difference of the same contour line should be small, but also the temperature difference between the upper and lower temperature of the kiln flame space should be small, that is, the temperature difference within different contour lines should be small, so that the heating curve can be implemented for the special requirements of each refractory material, so that the furnace body can expand evenly, avoiding the brick body bursting caused by uneven heating of the kiln brick body or too fast heating; the kiln steel structure, that is, the top wire clamp, should be adjusted in time when baking the kiln, which will affect the baking life of the kiln.
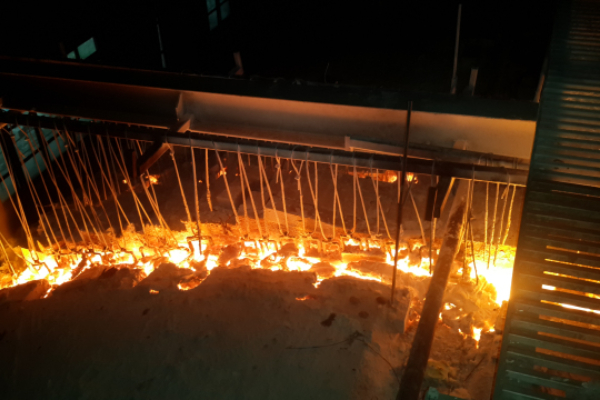
Kiln operation and maintenance
The correct operation of the kiln not only refers to the control of melting temperature and the amount of material in and out, but also includes how to make full use of the melting area of the melting pool to evenly distribute the material pile in the melting pool; how to change the heat transfer effect of the batch material through the feeding equipment. The type, installation and use of the feeder are also effective in reducing energy consumption or melting temperature; the bubbling frequency and bubble diameter of the kiln bubbling system also affect the melting effect and the kiln temperature; factors such as whether the broken glass and the batch material contain metal, the use pressure of the kiln, and the daily maintenance of the glass furnaces such as cleaning and sanitation have a great impact on the life of the kiln. During use, the equipment will be affected by multiple factors such as high temperature, high pressure, and chemical corrosion. If it is not maintained in time, it will easily lead to aging and damage of the equipment. Therefore, when using kiln equipment, regular inspection and maintenance should be carried out, and damaged parts should be replaced in time to ensure long-term and stable operation of the equipment.
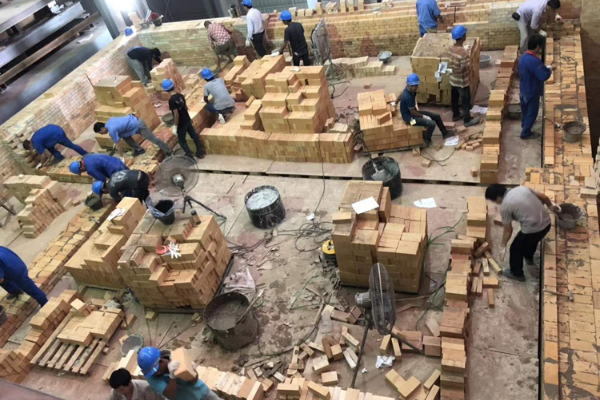
WeChat
Matawai te Waehere QR me te wechat