Oxy-combustion glass kiln, the volume concentration of water vapor in the flame space is greatly increased, and the volume concentration of alkali volatiles increases by 3 ل 6 times. Traditional air-assisted combustion kilns use siliceous materials when there is a lot of space in the upper part. High-concentration water vapor and high-concentration alkali volatiles form a strong alkaline atmosphere, which harms the performance of the silica bricks in the superstructure.
Compared with the large kiln, the concentration of alkali vapor in breast walls, gables, and other parts will be slightly lower, but they also face acid-base neutralization reactions, and the exceeding normal erosion rate makes the life of the kiln unpredictable. فضلاً عن ذلك, the eroded and peeled materials fall on the glass surface to form scum, which further affects the melting performance and glass quality.
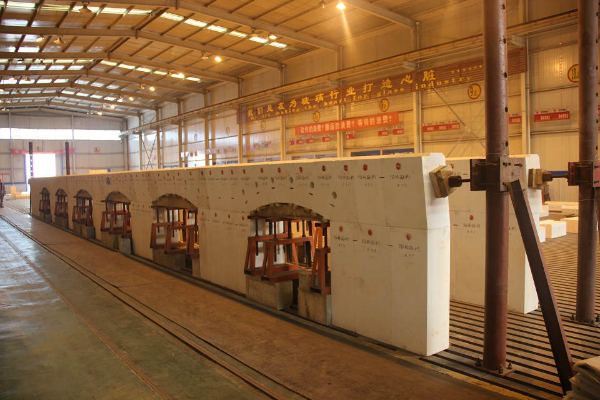
How to choose refractory materials for all-oxygen glass furnaces?
في الوقت الحالي, the refractory materials used more in the superstructure of oxy-combustion glass furnaces are mainly fused casting materials, such as fused AZS series, fused alumina series, و fused chromium corundum series (currently there is a tendency to use sintered chromium corundum instead), إلخ. In addition to the common ER1681, ER1685 and ER1711, the electrofusion AZS series also includes ER1851 and ER1195. The fused alumina series includes fused α-β alumina and fused β-alumina materials.
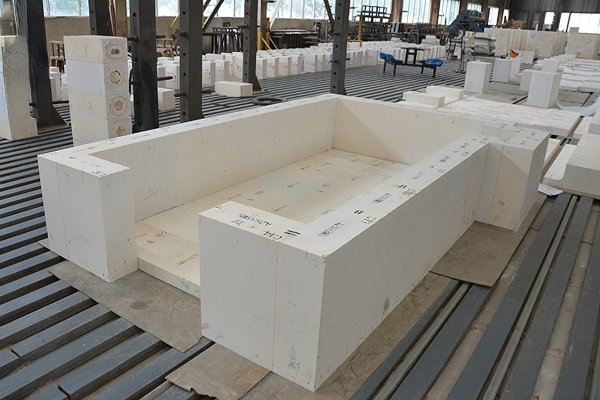
High zirconium series refractory materials
High-zirconium series products usually refer to products with a zirconium oxide content of 85% ل 95%. Although its production is difficult and its price is high, it is widely used in many glass industries due to its superior performance.
Due to its excellent properties, it reduces the generation of stones and bubbles in glass production, so it is more suitable for parts in contact with glass in glass furnaces, such as borosilicate glass, aluminosilicate glass, glass ceramics, and display glass. has good performance in the furnace. Depending on the requirements, there are subdivided products with high resistivity.
Fused α-β alumina products
It is composed of about 50% each of α-alumina and β-alumina. The two crystals are interlaced to form a very dense structure. It has very good resistance to strong alkali and has very good corrosion resistance below 1350℃. Because it does not contain harmful impurities such as iron and titanium, the glass phase content is very small, and the contamination of the glass by its exfoliation is minimal. In addition to being used in common flow channels, clarifiers, lip bricks of float glass melting furnaces, إلخ., it can also be used in Used as the roof of the kiln (mainly considering the longer service life and the pollution of the glass liquid by hanging droplets).
High-purity magnesium aluminum spinel
The chemical formula of magnesia-aluminum spinel is MgO-Al2يا3, containing 28.3% MgO and 71.7% آل2يا3 (atypical data, for reference only). Its main advantages are strong corrosion resistance to reducing atmospheres such as free CO2, free SOX, and free K2O/Na2يا, and good thermal stability and wear resistance. Magnesia-aluminum spinel has a high melting point, small thermal expansion coefficient, low thermal stress, good thermal shock stability, smaller volume density (2.7ز / سم 3) than electrofusion materials, and strong resistance to alkaline atmospheres ability.
Isostatically pressed high zirconium bricks
Isostatically pressed high zirconium bricks have been used in oxy-combustion kilns due to their excellent density, مقاومة التآكل, and lower price than fused high zirconium bricks, with good results.
Dense chromium oxide brick
Due to its excellent thermal shock performance, alkali resistance, and erosion resistance, dense chrome bricks have been widely used in fiberglass kilns, including the flame space of all-oxygen combustion fiberglass kilns. The chromium in dense chrome bricks adopts different chromium contents according to different parts of use. عمومًا, Cr2O3>90% and bulk density>4.0g/cm3.
Chromium oxide has a strong coloring ability. عمومًا, it is not recommended to use chromium-containing refractory materials for high-white or higher-quality glass, especially in parts that are in contact with the glass liquid. For colored glass or green and white materials with lower quality requirements, it can be considered to extend the life of the kiln.
Electrofusion and re-sintered mullite
Typical product data of electrofusion resintered mullite bricks are: Al2O376%, Fe2O30.1%, SiO223%. Load softening temperature T0.5>1700℃, bulk density 2.66g/cm3, normal temperature compressive strength 1100N/mm2, glass phase content <4%. Due to its relatively neutral characteristics, large furnaces in oxy-fuel fiberglass kilns are currently used more frequently.
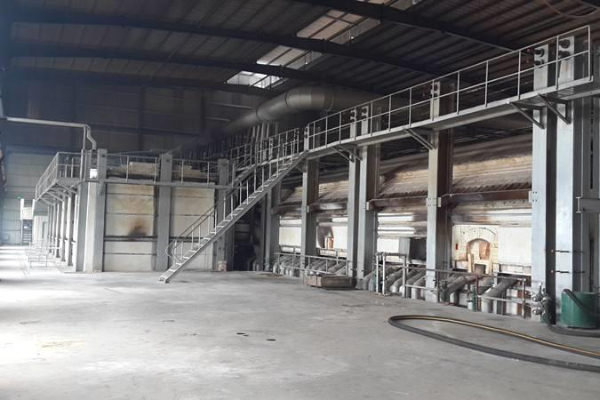
Calcium-free silica brick
The advantages of its product are: ① It uses fused silicon oxide as a binding phase, does not contain calcium oxide, and the silica content can reach more than 98.5%; ② The density is smaller (1.8ز / سم 3), which reduces the weight of the entire rice bowl; ③The price is lower than the same level of electrofusion materials; ④It has a lower expansion coefficient (0.6% at 650℃) and higher operating temperature (T0.5 is 1690℃) than silica bricks; ⑤Better volume stability sex. I have experience in using it in an all-oxygen combustion kiln in China, but there is a deformation problem that threatens the safety of the kiln.
وي شات
مسح رمز الاستجابة السريعة باستخدام wechat