How is refractory castables constructed and what are the precautions during construction? This post describes the construction method of high-temperature kiln castable.
Preparation of refractory castables before construction
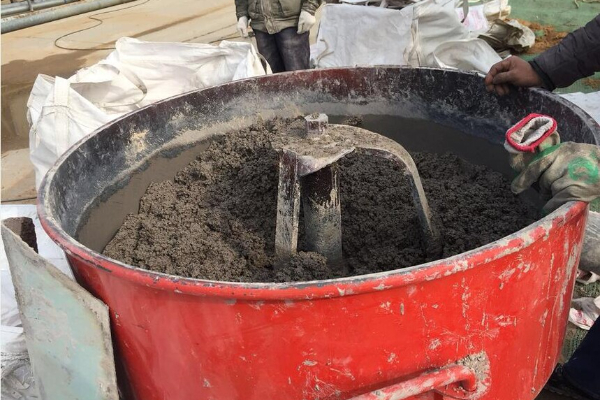
Transport the forced mixer, vibrator, and other tools to the construction site and test whether the operation is regular. فضلاً عن ذلك, pay attention to the use of forced mixers and high-frequency vibrators. Refractory materials are generally packed in bags, anchor bricks, and insulating refractory bricks. Calcium silicate boards, ceramic fiber blankets, refractory clay bricks, burner bricks, and other matching refractory materials must be transported to the site together for easy use at any time. When using a chemical binder, its concentration and density should be adjusted in advance, transported to the site for help, and stirred evenly before use.
Construction ratio of castables
Bagged refractory castables and admixtures should be sampled and tested according to the requirements of the manufacturer before construction. And check the main performance. When purchasing refractory materials, attention should be paid to their performance indicators. Proportioning will be done after the products are qualified.
Insulating layer masonry and formwork
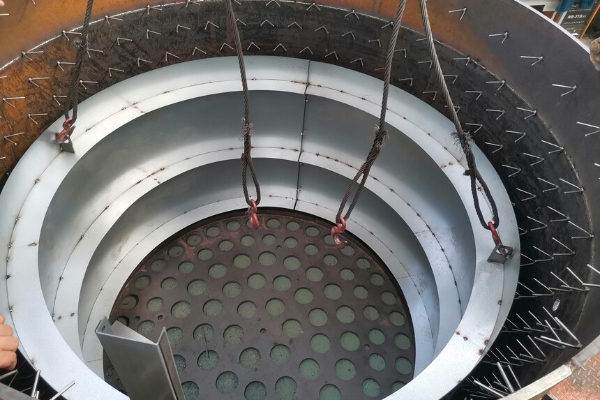
- Before the construction of refractory castables, calcium silicate boards or ceramic fiber blankets should be laid, metal connectors should be installed, and anchor bricks should be placed.
- Masonry refractory bricks or pouring lightweight refractory castables
- Set up templates. Apply oil or stickers to the working surface of the formwork first, and then place it close to the working surface of the anchor bricks for support. The height of the formwork should be 600-1000mm each time to facilitate loading and vibration molding. When there is fetal membrane, it should be Set up the fetal membrane and then set up the template. The surface of the heat insulation layer should be pasted with a plastic film to absorb water in a way that affects the performance of the castable.
- When the furnace wall is high, the masonry of the heat insulation layer should also be built in layers to prevent the pouring of the heat insulation layer when the castable vibrates.
How to construct a refractory castable furnace roof?
When constructing the refractory castable furnace roof, according to the design size requirements, first support the entire formwork firmly and then apply oil; then hang the hanging bricks on the suspension beams with metal connectors. Some connectors need to be made of wood. Wedges fix the hanging bricks, and some don’t need to be fixed. The hanging bricks should be placed vertically to the working surface of the furnace lining. The distance between the bottom end surface and the formwork surface is 0~10mm, and more than 60% of the end surfaces of the hanging bricks should be in contact with the formwork surface. When the spacing is greater than 10mm, the metal connector should be adjusted to meet the requirements. When there is a hole, the tire mold should also be installed firmly, and then the formwork should be supported.
Castable mixing
For kneading, a forced mixer should be used. When the amount of material is small, manual mixing can also be used. The variety of refractory castables is different, and there are certain differences in mixing; bagged materials or refractory bone powder and cement, إلخ., the allowable error is 1.0% of soil, the allowable error of additives is +0.5%, and the allowable error of water and liquid binder is + 0.5%, the admixture must be accurate.
Mixing different types of refractory castables
- For the mixing of refractory castables such as cement, clay combination, and low cement series, first pour dry bulk materials such as bagged materials, admixtures, and admixtures into the mixer for 1.0min, and then add water for wet mixing 3 ~5min, after the material color is uniform, the material is discharged. Then it is transported to the face of the palm and the fabric is started.
- To mix water glass refractory castables, it is best to first pour the refractory granules into a mixer for dry mixing, then add water glass solution for wet mixing. After the particles are wrapped by water glass, add refractory powder and other materials. The wet mixing is about After 5 دقائق, the material is ready for use; if the dry materials are mixed together, pour them into a mixer and mix dry for 1.0 دقائق, add 2/3 of the water glass solution and mix wet for 2 ل 3 دقائق, then add the remaining binding agent to wet Mix for 2~3 minutes and the ingredients are ready to use. The mixing of resin and carbon-containing refractory castables is similar.
- For kneading of refractory castables such as phosphoric acid and phosphate salts, first pour the dry material into a mixer and dry mix for 1.0 دقائق, add about 3/5 of the binder and mix wet for 2 ل 3 minutes before discharging the material and transporting it to a designated place for stacking. Cover tightly with plastic film to trap the material. The trapped material time should be greater than 16 ساعات. After weighing the trapped ingredients and coagulant, pour them into a mixer for secondary mixing, add the remaining binding agent, and mix wet for 2 ل 4 minutes before use.
Precautions for mixing
When mixing refractory castables, if heat-resistant steel fibers, refractory fibers, and organic fibers need to be added to the material, they should be continuously scattered into the mixing material of the mixer during the wet mixing process of the refractory castables. Medium, stir while scattering, do not add in lumps. After the mixer comes out of the mixer, if it is too dry, too thin, or lacks certain materials, the material should be discarded and must not be reused; the mixer should be used up within 0.5~1.0h. Materials that have initially hardened and dried should be discarded.
Precautions for mixing
When mixing refractory castables, if heat-resistant steel fibers, refractory fibers, and organic fibers need to be added to the material, it should be continuously scattered into the mixing material of the mixer during the wet mixing process of the refractory castables. Medium, stir while scattering, do not add in lumps. After the mixer comes out of the mixer, if it is too dry, too thin, or lacks certain materials, the material should be discarded and must not be reused; the mixer should be used up within 0.5~1.0h. Materials that have initially hardened and dried should be discarded.
Vibration molding of castables
- When pouring the bottom of the furnace, the thickness of the pavement is about 200mm and then vibrates with a flat vibrator. If the vibrating rod is used to vibrate, the thickness of the paving material is 200~400mm. When constructing the furnace wall, spread the material from one end or the place where the expansion is left, and the thickness of the material is 300~400mm. Immediately after distributing, vibrate with a vibrating rod, and vibrate while distributing, and continue construction. The formwork should also be installed continuously. When there is an expansion joint, the expansion joint material should be added, and the state required by the design should be maintained.
- When vibrating the molding, the flat plate vibrator should move continuously, and the edges of the flat plates should overlap to prevent vibration leakage; when using the vibrator, the vibrator should be inserted into the material layer slowly, moved continuously, and pulled out slowly to prevent holes and leaks. Vibrate. The vibrating rod must not collide with formwork, anchors, and insulation. It is better to keep the vibrating rod away from the template and the wall, preferably 80~120mm. The lining body generally needs to be vibrated more than two times continuously until the surface returns to the slurry, less row, and no settlement.
- The construction of the roof lining also starts from the end, and the thickness of the fabric is generally 250~300mm. The vibrating rod moves between the hanging bricks along the length and width of the furnace and does not collide with the hanging bricks. When the surface of the material returns to the slurry and reaches the design thickness, the construction can continue. During the construction process, expansion joint materials, temperature-measuring hole tire molds, إلخ. should be released. After the construction of the entire furnace top lining, it can be used as a heat insulation layer, but the metal connectors of the hanging bricks must not be buried in it.
- When the refractory castable lining is completely constructed and has initial strength, the formwork can be removed and the site cleaned. في نفس الوقت, according to the variety of requirements of refractory castables, maintenance
وي شات
مسح رمز الاستجابة السريعة باستخدام wechat