In industrial production, protecting and maintaining high-temperature thermal equipment is crucial. Various refractory materials, especially ramming materials, play a key role. Ramming materials of different materials have their own unique characteristics and application ranges and can meet the needs of different industrial furnaces. This article will introduce five different materials of ramming materials, and let us understand their characteristics and application fields.
Five types of ramming materials
Carbon ramming mass
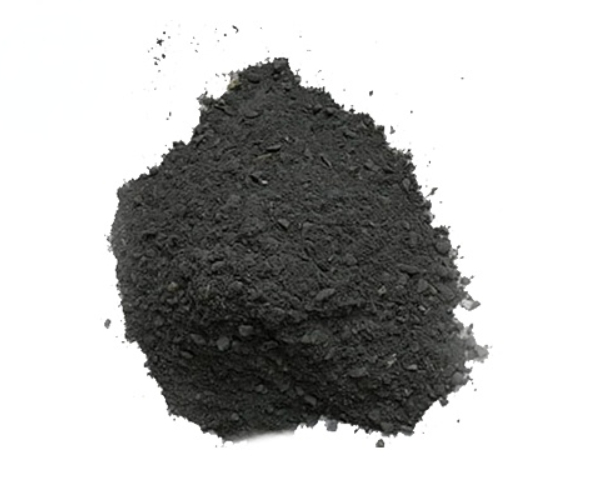
According to different blast furnace types and different material design requirements, carbon ramming materials are mainly used in the gaps between the blast furnace bottom carbon bricks the bottom sealing plate between the hearth carbon bricks and the cooling stave, and The leveling above the center line of the furnace bottom water-cooling tube and the filling of the cooling stave require that the carbon ramming material after ramming has a certain strength and density, filling every corner and small gaps to achieve impermeability. The requirements for leakage of molten iron and gas, and the thermal conductivity of the carbon ramming material must be consistent with the performance of the hot carbon bricks and cooling staves of the blast furnace, so as not to affect the life of the blast furnace and maintain normal production of the blast furnace.
At present, a common problem encountered in the use of carbon ramming materials is that the thermal conductivity of general carbon ramming materials is low, which is not conducive to the rapid cooling of the blast furnace body, thereby affecting the service life. Therefore, the updated research and application of carbon ramming materials with high thermal coefficients have great market prospects. Whether adding admixtures to the carbon ramming material, changing the properties of the material through in-situ reactions at high temperatures, or changing the local material usage structure from a design perspective, the carbon ramming material layer can reach the same level as the carbon ramming material when the working temperature rises. The thermal conductivity of the bricks and cooling staves matches to ensure normal heat conduction without damaging the overall construction structure, thereby achieving the requirement of improving the service life of the blast furnace.
Silica ramming mass
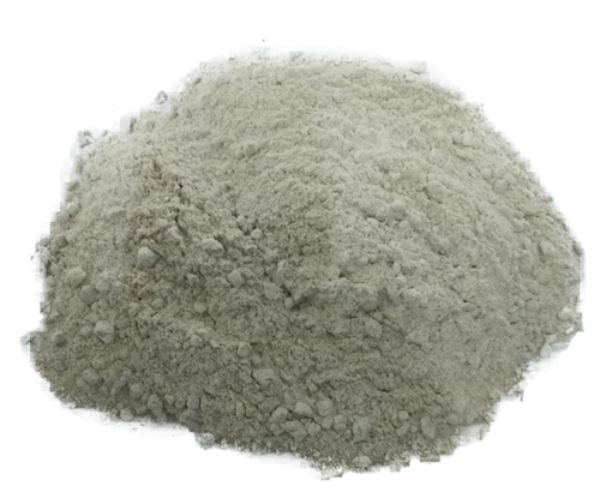
The main raw material of silica ramming material is silica. Silica is the general name for vein quartz, quartzite, and quartz sandstone. Mainly used in acid refractory bricks for the metallurgical industry. Pure silica can be made into quartz glass or refined single-crystal silicon. In the chemical industry, it is used to prepare silicon compounds and silicates, and can also be used as a filling in sulfuric acid towers. In the building materials industry, it is used in glass, ceramics, Portland cement, وغیرہ.
Corundum ramming mass
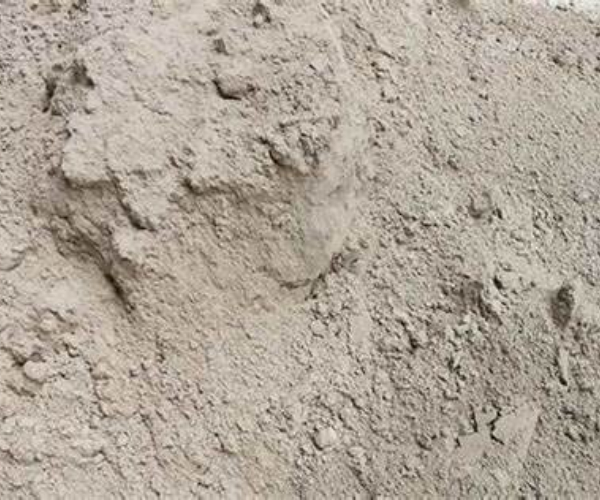
Corundum ramming material is a bulk material made of corundum, silicon carbide, graphite, and electrically calcined anthracite as raw materials, mixed with a variety of ultrafine powder additives, and fused cement or composite resin as a binding agent. It is used to fill the gap between the furnace cooling equipment and the masonry or the filling material for the masonry leveling layer.
Magnesium ramming mass
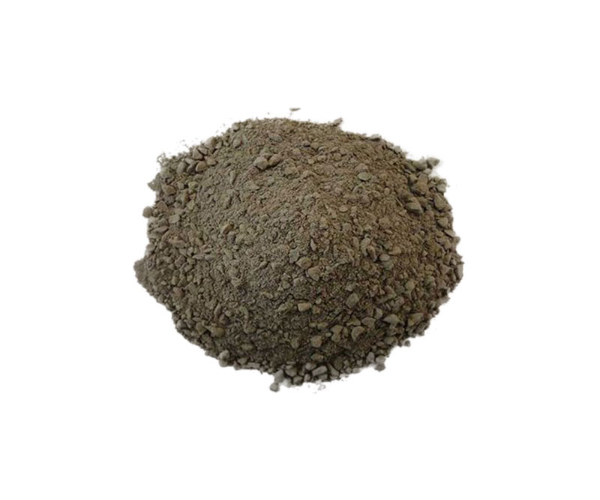
Magnesia ramming material is a bulk material made of fused magnesia as raw material, mixed with a variety of ultra-fine powder additives, and fused cement or composite resin as a binding agent. It is used to fill the gap between the furnace cooling equipment and the masonry or the filling material for the masonry leveling layer.
Medium frequency furnace ramming mass
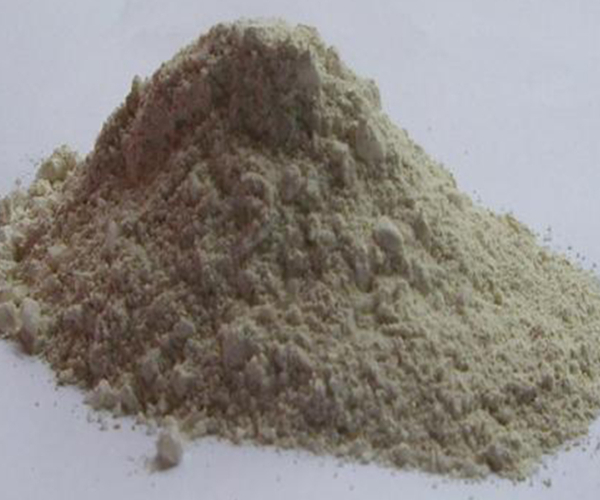
The medium-frequency induction furnace has an induction coil made of copper tubes wound around the outside of the furnace. The metal charge is placed in the furnace. When the alternating current passes through the induction coil, an alternating magnetic flux is generated in the coil. Through the closed metal charge, the furnace charge An induced current is generated within a certain depth on the surface, causing the charge to heat and melt. The furnace lining is made of refractory materials, which require good corrosion resistance, peeling resistance, no cracks, and a long service life. The material used in the intermediate frequency furnace is the ramming material of the intermediate frequency furnace, and its main performance indicators are.
WeChat
وی چیٹ کے ساتھ کیو آر کوڈ اسکین کریں۔