Refractory materials for cement kilns should be strictly and reasonably selected according to each part’s working conditions to extend the kiln lining’s life and the equipment operation cycle and ensure that the cement kiln can create better economic benefits. The rotary kiln of the cement plant requires refractory materials to have good mechanical strength, high refractoriness, thermal shock resistance to temperature changes, small thermal expansion and burning line changes, excellent resistance to chemical erosion, good wear resistance and porosity, accurate size, neat appearance, etc.
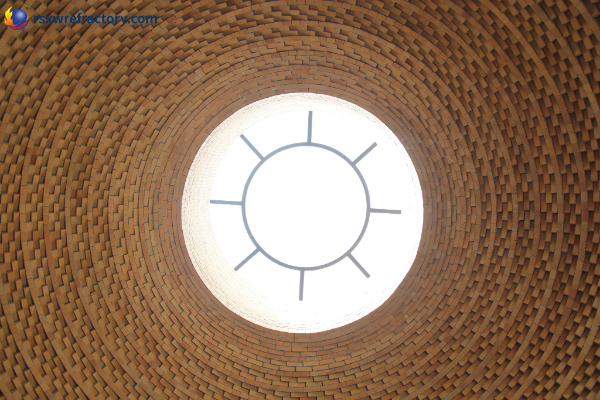
Refractory materials for cement kilns introduction
Refractory clay bricks
Clay bricks are aluminum silicate refractory products with 30-40% aluminum oxide content. Its mineral composition is 20-50% mullite (3Al2O3·SiO2), 25-60% glass phase, and quartz and quartz (up to 30%). Ordinary clay bricks can be divided into first-class (>40%), second-class (>35%), and third-class (>30%) according to the Al2O3 content; the corresponding refractoriness is not less than 1730℃, 1670℃ and 1610℃; the load softening temperature is 1250~1450℃; the thermal stability is good.
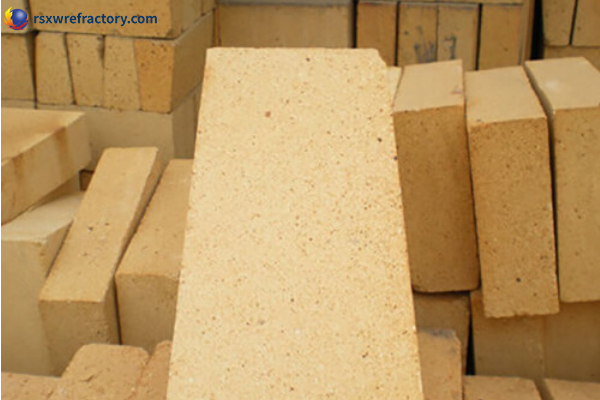
High alumina brick
High alumina bricks are aluminum silicate refractory products with more than 48% alumina content. The mineral composition is corundum (α-Al2O3), mullite, and glass phase, and its content depends on the Al2O3/SiO2 ratio and the type and quantity of impurities. The grades are divided according to the Al2O3 content. my country’s high alumina bricks are divided into three grades: LZ65 contains Al2O365~70%, refractoriness 1790℃, LZ55 contains Al2O355~65%, refractoriness 1770℃; LZ48 contains Al2O3 48~55%, refractoriness 1750℃.
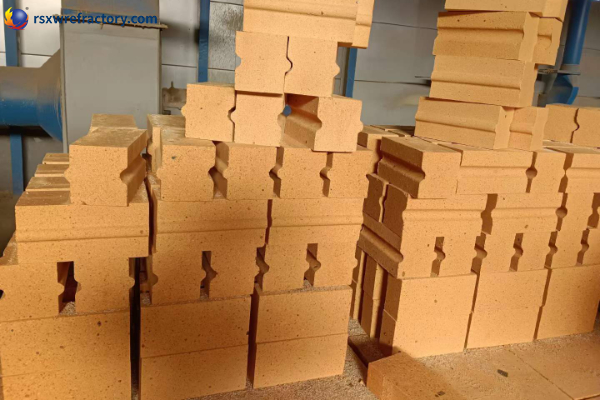
Phosphate-bonded high alumina kiln lining bricks
Phosphate-bonded high-alumina kiln lining bricks include two products, one is phosphate-bonded high-alumina bricks (referred to as phosphate bricks), and the other is phosphate-bonded high-alumina wear-resistant bricks (referred to as wear-resistant bricks). Phosphate bricks use a phosphoric acid solution with a concentration of 42.5-50% as a binder, and the aggregate is a bauxite clinker calcined at more than 1600°C in a rotary kiln. During the use of the bricks, phosphoric acid reacts with the fine powder of burnt alumina on the brick surface and refractory clay and finally forms a binder mainly composed of cristobalite-type aluminum orthophosphate. Wear-resistant bricks use industrial phosphoric acid and industrial aluminum hydroxide to form an aluminum phosphate solution as a binder, and its molecular ratio is Al2O3:P2O5=1:3.2. The aggregate used is the same as that of phosphate bricks. During the use of the bricks, a binder mainly composed of cristobalite-type aluminum orthophosphate is formed like phosphate bricks.
Magnesia brick
Magnesia brick is an alkaline refractory product with a magnesium oxide content of not less than 91%, calcium oxide content of not more than 3.0%, and periclase (MgO) as the main mineral. It has good thermal conductivity, a large thermal expansion coefficient, good resistance to alkaline slag, and poor resistance to acidic slag. The load-deformation temperature is not high due to the low melting point of silicate cementation around the periclase grains, and the collapse temperature is not very different from the starting point. The refractoriness is higher than 2000℃, but it is meaningless for practical use. Therefore, the development direction must be magnesia bricks with high load deformation performance combined with forsterite and magnesia-alumina bricks with high thermal shock stability combined with magnesium-alumina spinel (MgO·Al2O3).
Magnesia alumina spinel brick
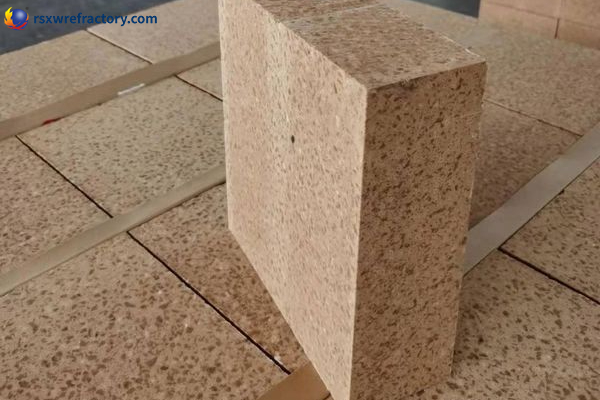
Magnesia-alumina spinel brick is a magnesia brick with magnesia-alumina spinel as the main mineral, which is produced by adding alumina to the ingredients to improve the thermal shock stability of magnesia bricks. After the production of directly bonded magnesia-chrome bricks, it is currently developing in the direction of advanced magnesia-alumina spinel bricks. In production, high-purity magnesia sand and synthetic spinel are used as raw materials, and the ratio of the two is 0.7-0.8 to 0.3-0.2. The production methods include electric melting and sintering. The advantages of spinel bricks are good thermal shock stability. During use, it can react with clinker to form a very thin calcium aluminate protective layer on the surface of the brick, making it difficult for the liquid phase to penetrate, and the anti-stripping performance is better than that of directly bonded magnesia-chrome bricks. However, the corrosion resistance is slightly inferior to that of directly bonded magnesia-chrome bricks.
Ordinary magnesia chrome brick
Magnesia-chrome bricks contain MgO55-80%, Cr2O3≥8%, the main minerals are periclase and chrome spinel, and the silicate phases are forsterite and calcium forsterite. If the Cr2O3 content is as high as 18-30%, and MgO25-55%, it is called magnesia-chrome bricks. Ordinary magnesia-chrome bricks have strong resistance to alkaline slag and better resistance to acidic slag than magnesia bricks, high load softening point, good volume stability at high temperatures, and small re-burning linear shrinkage at 1500℃.
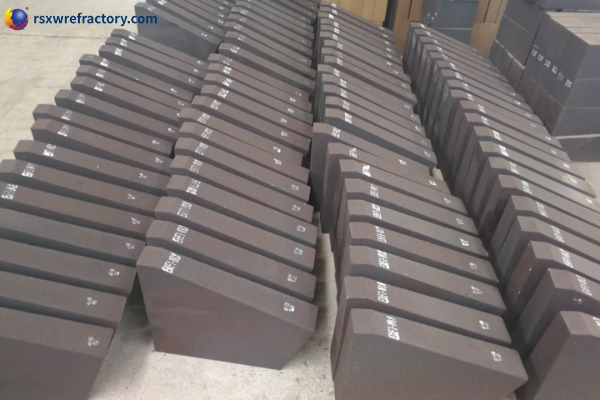
Direct bonded magnesia chrome bricks
In large kilns, the kiln temperature is above 1700℃, and ordinary magnesia-chrome bricks are difficult to meet the requirements. Directly bonded magnesia-chrome bricks are a high-quality magnesia-chrome refractory material developed to adapt to large-scale cement production. Directly bonded magnesia-chrome bricks are made of high-quality magnesia ore and chromite ore as raw materials. They are first fired into light-burned magnesia sand, then granulated into balls under high pressure according to a certain gradation, fired into heavy-burned magnesia sand at a high temperature of 1900℃, and then a certain proportion of chromite ore is added, pressed, and formed, and calcined in a tunnel kiln at 1750-1850℃. Those fired at 1750-1800℃ are high-temperature directly bonded magnesia-chrome bricks, and those fired at 1800-1850℃ are ultra-high-temperature directly bonded magnesia-chrome bricks.
Sodium polyphosphate combined with magnesium brick
This brick is a chemically bonded magnesium brick, which is composed of high-calcium synthetic magnesium sand as aggregate, sodium polyphosphate as binder, and pulp waste liquid as a hydration inhibitor. Its ratio is: high-calcium magnesium sand: sodium polyphosphate: pulp waste liquid: water, the ratio is 3:0.7~1.0:3:3.5. After mixing, it is wet-milled, pressed, and dried at 150~200℃ to become a finished product. Sodium polyphosphate bonded magnesium brick has both room temperature curing and heat curing properties, and the room temperature strength and compressive strength at 1450℃ are both high; load softening point, generally 0.6% deformation starting point fluctuates between 1500~1690℃, 4% deformation point is above 1700℃; thermal expansion coefficient and elastic modulus are higher than ordinary magnesium chrome bricks; thermal shock stability is also better than ordinary magnesium chrome bricks; cement clinker erosion resistance is also good.
Alkali resistant brick
Alkali-resistant clay bricks with an Al2O3 content of 25-28% cause the alkali in the kiln gas to condense on the brick surface and then react chemically with the brick surface quickly, forming a high-viscosity glaze layer, which blocks the pores for the alkali to continue to erode the inside of the brick body, thereby preventing “alkali cracking”. my country’s ordinary alkali-resistant clay bricks have SiO2>65%, Al2O3<30%, bulk density>1.9g/cm3, apparent porosity<25%, room temperature compressive strength>20MPa, thermal conductivity 1.163W/m·k (350℃), thermal expansion coefficient 6×10-6/℃, and load softening point starting point>1320℃.
Insulating refractory materials
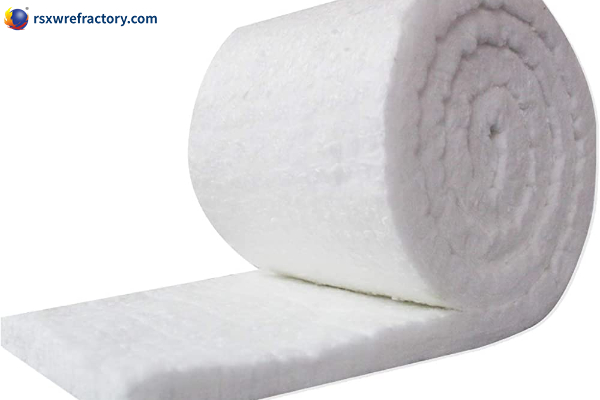
Insulating refractory materials are insulating products made of lightweight refractory materials. Its varieties include lightweight calcined bricks, refractory insulating concrete, insulation boards, and ceramic refractory fiber products. They all have the characteristics of porous structure, lightweight, low thermal conductivity, and good thermal insulation performance.
WeChat
wechat арқылы QR кодын сканерлеңіз