Mullite refractory castable is favored in high-temperature industries due to its good fire resistance, thermal shock resistance, and strength. They are often used in high-temperature furnace linings in industries such as steel, petrochemicals, and cement. To achieve the best use of mullite castables, the correct construction method is essential. This article will introduce the construction steps and precautions of mullite castables in detail to help you understand how to ensure construction quality and use results.
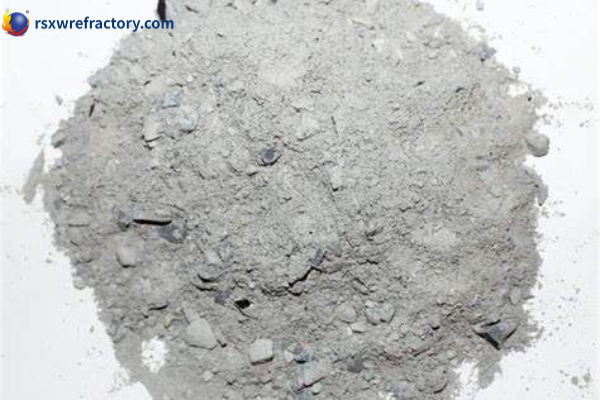
Construction of mullite castable
Preparation before construction
High-strength high-alumina mullite castable is made of multiple ingredients, with active composite ultrafine powder and a small amount of pure calcium aluminate cement added. It has high activity, so the storage conditions and time requirements are high. It must be strictly prevented from moisture. If the packaging is damaged or damp, it must not be used. Its storage period should not exceed three months from the factory. Construction machinery must be cleaned to ensure the normal operation of construction machinery, such as forced mixers, vibrating rods, scales, and drilling hand drills.
Construction of mullite refractory castable
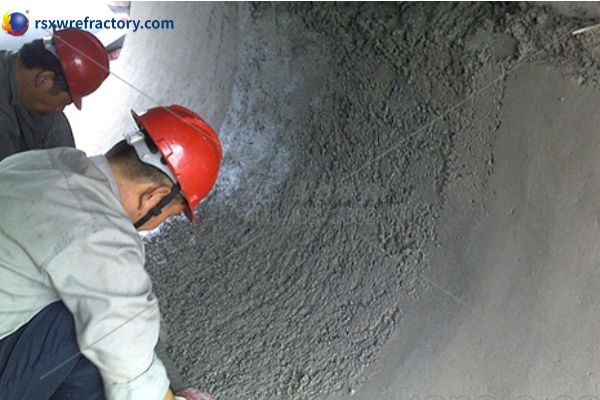
Before construction, operators should master each process’s key points and quality requirements. After adding the materials to the mixer, dry mix and stir for 1 minute, and then add water. If the materials are too dry or too thin, the quality will be affected. It is OK to knead them into a ball and make a slurry. It is strictly forbidden to add water temporarily when pouring out of the tank. Once the amount of water is determined, it should not be changed easily to ensure that the density of each mixing is consistent. The recommended mixing time is 5 minutes. It is not good to be too long or too short. The mixed castable should be poured immediately, and the parking time should not exceed 20 minutes.
The castable should be laid evenly at the construction site. Do not use too much force to dislocate the formwork, expansion plate, anchor bricks, and other facilities. Generally, the material is vibrated with a vibrator after about 300mm of laying, and each part should be returned to the slurry. When pulling out the vibrator, it should be lifted slowly to avoid leaving holes. If it is found that there is no vibration, it should be dug out and re-vibrated. After pouring, the surface of the casting body does not need to be smoothed.
Natural curing for 2 to 3 days. During the curing period, it is strictly forbidden to step on or touch the castable. When the castable solidifies, vent holes should be made in time to help remove water vapor. Demolding can be done only after it is confirmed to have sufficient strength.
Mullite castable baking
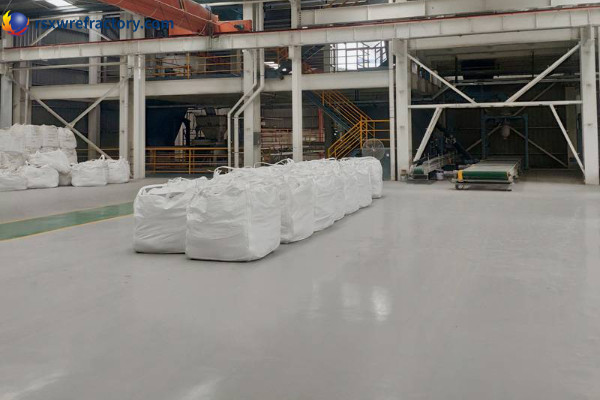
High-strength and high-aluminum mullite castables are dense and high-strength, with very low porosity, and it is not easy to remove water smoothly. Especially in the stage of removing a large amount of free water in the temperature range of 100-300 ℃, it is easy to cause excessive steam pressure and cause lining peeling or explosion accidents, so special attention should be paid and sufficient removal time should be given. As the temperature rises, free and crystal water are continuously removed. When it reaches 500 ℃, the water content of the castable is only about 10% of the total water content. Therefore, the castable should be heated slowly before 600 ℃ and have sufficient insulation time. After 1000 ℃, mullite begins to form in large quantities, and the formation of mullite primary crystals is basically completed at 1300 ℃. As the mullite grains continue to grow, the castable becomes dense, the bonding force increases and the strength continues to increase.
WeChat
wechat арқылы QR кодын сканерлеңіз