Spraying mass is a kind of refractory material that depends on pneumatic tools for spraying construction. It is mainly used for new refractory lining of components and repairing damaged lining. It can be divided into light, semi-light, heavy gunning materials, and alkaline patching materials according to the raw materials used and the role of use. It has the characteristics of convenient construction, high work efficiency, labor savings, and so on.
What is refractory spray coating?
The material composition of refractory spray coating is similar to that of refractory castables of the same type, except that the critical particle size of refractory aggregate is smaller, generally 3-5mm. It is constructed by spraying. The combined amount of refractory powder, ultrafine powder, and binder is relatively large, generally 35~45%.
Technical Parameter of Hot Sale Spraying Mass
Item | Light Or Semi-light | Heavy | Alkali | ||||||
QP-0.8 | QP-1.3 | QP-1.8 | ZP-40 | ZP-50 | ZP-60 | MP | MGP | ||
Al2O3 % | ≥30 | ≥40 | ≥45 | ≥40 | ≥50 | ≥58 | / | / | |
MgO % | / | / | / | / | / | / | ≥80 | 60~70 | |
CaO % | / | / | / | / | / | / | / | 20~40 | |
Bulk Density g/cm3 110℃×24h | ≤0.8 | ≤1.3 | ≤1.8 | ≥2.0 | ≥2.1 | ≥2.3 | 1.8~2.1 | 1.8~2.0 | |
Cold Crushing strength MPa | 110℃×24h | ≥4 | ≥7 | ≥15 | ≥25 | ≥35 | ≥35 | ≥5 | ≥5 |
Temp×3h | ≥3 800 | ≥5 1200 | ≥13 1300 | ≥25 1000 | ≥30 1000 | ≥30 1000 | ≥10 1500 | ≥8 1500 | |
Permanent Linear Change Rate % | ±0.8 800 | ±0.8 1200 | ±0.8 1300 | ±0.5 1000 | ±0.5 1000 | ±0.5 1000 | -0.5~1.0 1500 | -0.5~1.0 1500 | |
Thermal conductivity W/(m · k) 350±25℃ | ≤0.21 | ≤0.35 | ≤0.70 | / | / | / | / | / |
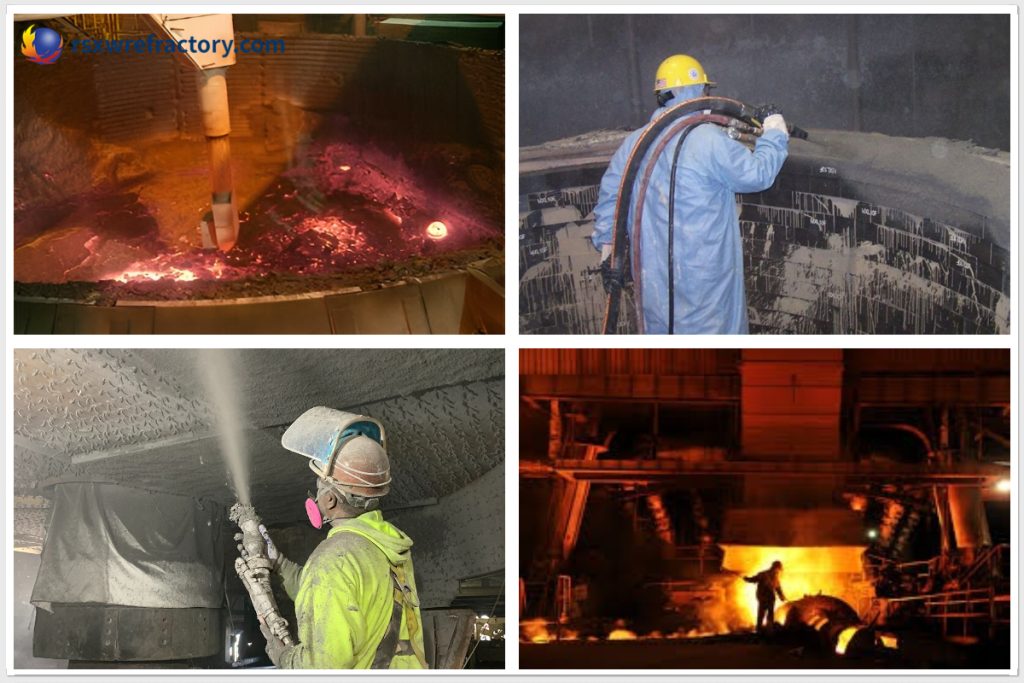
Advantages of refractory spray mass
- Easy construction
- Excellent adhesion
- Excellent integrity
- Diverse material selection
- Excellent performance
- Suitable for quick repair
- Environmental protection and energy saving
- Reduce maintenance costs
Classification of spray coatings
(1) Heavy refractory spray coating
The bulk density of heavy refractory spray coating is generally greater than 1.8g/cm3. Refractory aggregate and powder are generally made of aluminum silicate materials, with a critical particle size of 5 or 10mm. The particle composition is: 3~5mm is about 30%, 1~3mm is about 30%; less than 1mm is about 40%. The binder is made of aluminate cement water glass, stb., plus admixtures. It is generally constructed using the semi-dry method or pseudo-dry method.
(2) Lightweight refractory spray coatings
There are many types of lightweight refractory spray coatings, mainly clay, ceramsite, and perlite refractory spray coatings. Lightweight refractory spray coatings are mainly used for the thermal insulation layer of kilns, and can also be used for the working layer of tubular heating furnaces, flue,s, and chimneys.
The critical particle size of refractory aggregates for lightweight refractory spray coatings is 5mm. The particle grading is: 35mm is about 19%-30%; 0.6-3mm is about 8%-14%; 0.088-0.60mm is about 30%-40%, and less than 0.088mm is about 25%-35%.
Introduction to the construction method of refractory spraying mass
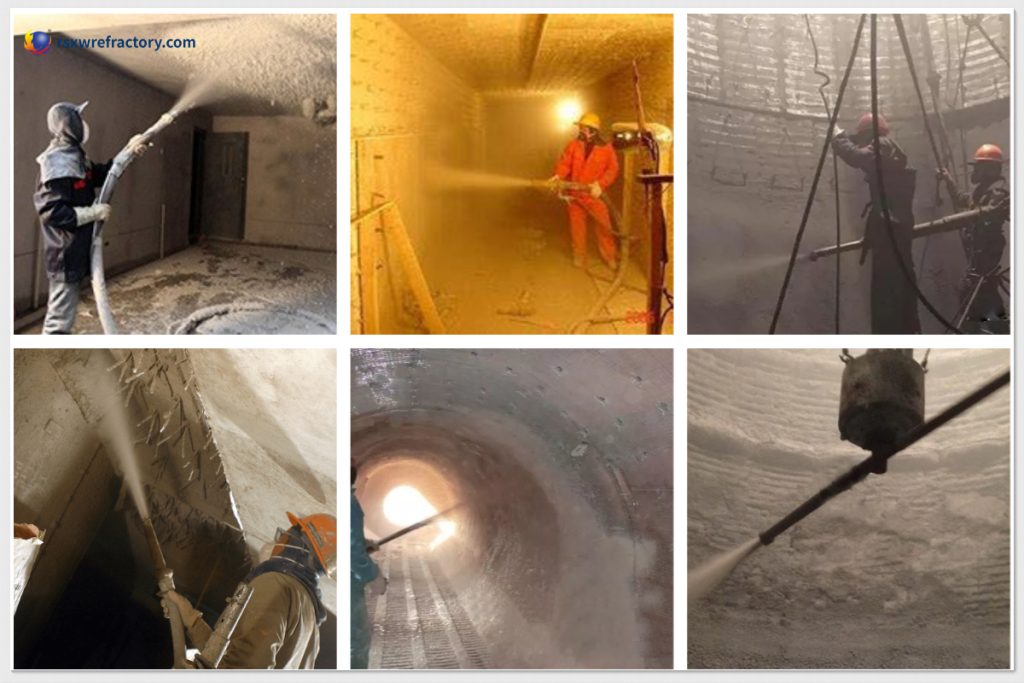
Flame spraying
This method uses oxygen to transport the mixed refractory spray layer to the nozzle and spray it together with the combustible gas. The combustible gas is burned, the material moves in the flame and melts into a plastic state, and is sprayed on the spraying surface. This method is mainly used for thermal spraying furnace linings, with little damage to the original lining, easy sintering of the spray layer, and long service life, but the cost is high. In addition, after melting or semi-melting with a plasma gun, spraying the refractory mixture onto the spraying surface and spraying the slag with appropriately adjusted furnace composition onto the lining (i.e., slag splashing method) also belong to this type of method.
Dry spraying
Dry spraying refers to spraying mixed refractory spray coating directly onto the spraying surface through a nozzle and is mainly used for furnace repair.
Wet spraying
This method refers to spraying the refractory coating on the spraying surface after adding water or liquid binder. According to the order and amount of water or liquid binder, it can be divided into four methods: mud method, wet method, semi-dry method, and pseudo method. Among them, the mixed-use of each two methods is called a mixed method. The mud method is to mix the refractory mixture into mud before spraying, which is mainly used for thermal spraying to repair furnace linings; the wet method is to mix the refractory mixture into pumping mud and then spray it; the semi-dry method is to mix the refractory mixture with a small amount of water, wet it evenly, and then send it to the nozzle, and then add the remaining water before spraying; the pseudo-dry method is to mix the refractory mixture through a mixer, add water and send it to the nozzle for spraying. The latter three methods are suitable for spraying furnace construction or spraying furnace linings.
Common types of refractory spraying mass
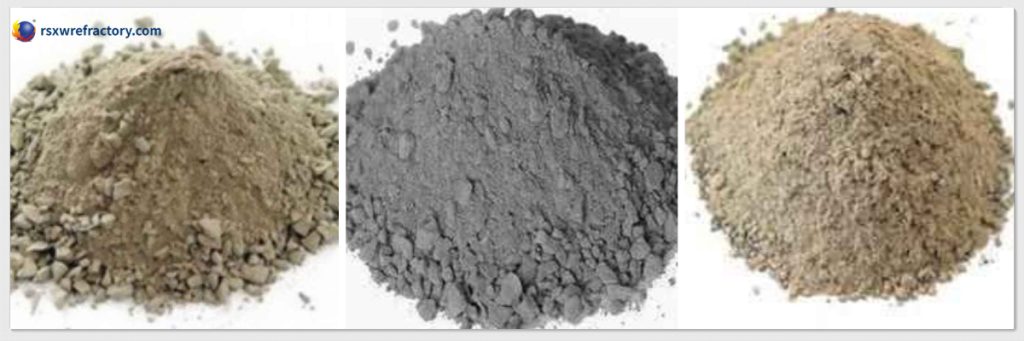
Silica refractory spray coating: silicate as the main component, adding the appropriate amount of binder and filler. It has good high-temperature resistance, corrosion resistance, and wear resistance, suitable for high-temperature environments such as metallurgy, chemical industry, and construction.
High-alumina refractory spray coating: It is mainly composed of high-purity alumina, with binders and fillers added. It has excellent high-temperature resistance and corrosion resistance and is suitable for high-temperature equipment such as steelmaking and aluminum electrolytic cells.
Magnesium refractory spray coating: magnesium salt is the main component, with added binders and fillers. It is lightweight, has high-temperature strength, and thermal shock resistance, and is suitable for high-temperature industrial furnaces such as glass kilns and ceramic kilns.
Silicon carbide refractory spray coating: Silicon carbide is the main component, with binders, antioxidants, stb. It has good high-temperature resistance, corrosion resistance, and thermal conductivity, and is suitable for large industrial furnaces in the foundry and electronics industries.
Refractory ceramic coating: It is mainly composed of ceramic particles and special binders. It has excellent fire resistance, corrosion resistance, and wear resistance, and is suitable for railways, building fire protection,n and other fields.
Wechat
Szkennelje be a QR -kódot a WeChat segítségével