Aluminum smelting furnaces mainly include reverberatory furnaces, rotary drum furnaces induction furnaces, και τα λοιπά. The operating temperature is generally 700-1000°C. The damage to the lining of this type of furnace is mainly caused by the penetration and erosion of molten aluminum. The lining is generally made of clay bricks, high alumina bricks, and corundum mullite bricks. It can also be made of high alumina refractory castables and refractory plastics. Due to good use conditions, the furnace has a longer life.
What refractory materials are used in different types of aluminum smelting furnaces?
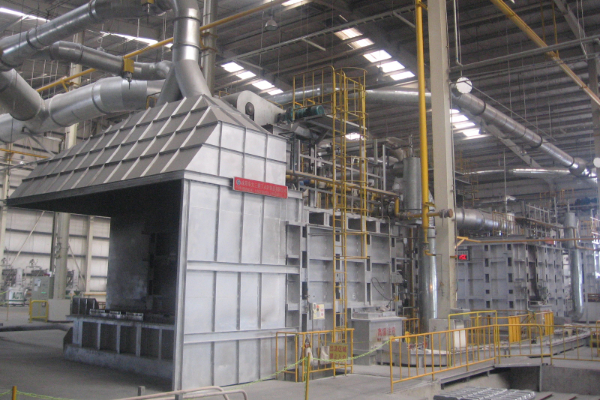
Reverberatory furnace refractory materials
The furnace is divided into two types: fixed type and tilting type. Γενικά, gas or heavy oil is used as fuel. Aluminum is usually smelted using a stationary reverberatory furnace. The non-working layer of the reverberatory furnace is built with refractory fiber felt and clay-insulating bricks. The working layer above the molten pool is generally built with clay bricks. It can also be hoisted with prefabricated blocks of high-aluminum refractory castables or poured on site or with high Aluminum refractory can be hammered into plastic. The working layer of the molten pool has different materials according to different usage requirements. Γενικά, it is built with high-aluminum bricks with an AL2O3 content of more than 75%. It can also be poured into the overall working layer with high-aluminum refractory castables with an AL2O3 content of 80%. When smelting high-purity metallic aluminum, the working layer of the molten pool should be constructed of high-purity mullite bricks, zircon bricks, or corundum bricks, and the aluminum discharge port, aluminum flow channel, and its lining should be used to resist the penetration and penetration of liquid aluminum. To prevent erosion, large silicon carbide bricks are generally used. The refractory materials used in the holding furnace and its flux and alloy material processing chamber are basically the same as those in the reverberatory furnace. When using electrolytic aluminum liquid as raw material, first use a siphon or vacuum bag to suck out the aluminum liquid from the bottom of the aluminum electrolytic tank, then transport it to the reverberatory furnace and pour it into the charging port. After charging, oxygen is blown into the molten pool while heating to perform dehydrogenation treatment. The siphon lining is generally made of refractory fiber-reinforced lightweight refractory castables as the thermal insulation layer, and can also be built with clay insulation bricks. The working layer is generally built with dense clay bricks or corundum bricks. The thermal insulation layer of the vacuum bag lining is the same as that of the siphon, and its working layer is built with high-quality clay bricks or high-aluminum bricks. Under normal operation, the service life of the reverberatory furnace and holding furnace is about 2-5 years.
Refractory materials for induction furnaces
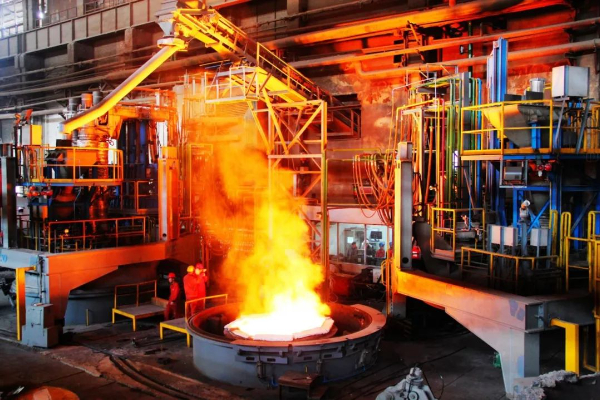
Induction furnace linings are generally constructed of clay bricks or third-grade high-alumina bricks. The base layer of the furnace bottom is first poured with high-aluminum refractory castables, and then high-alumina bricks are laid. When the capacity of the induction furnace is less than 10T, the lining can be made of high-aluminum refractory castables or refractory ramming materials with an alumina content of 75%, or corundum refractory castables. The lining around the furnace inductor coil is generally poured with corundum refractory castables or vibrated densely with dry vibrating materials. Due to different types of raw materials and operating conditions, the service life of the furnace also varies. Γενικά, the furnace age is 0.5-4 years. Repair easily damaged parts such as the lining around the coil 1-5 times.
Rotary furnace refractory materials
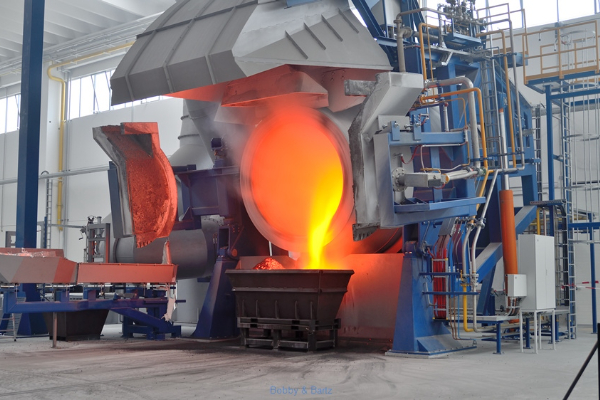
The non-working layer is built with clay-insulating bricks, which can also be poured with lightweight refractory castables or made into prefabricated blocks; the working layer is built with dense clay bricks or high-aluminum bricks. The age of rotary drum furnace is generally 300-500 heats. When salt flux is added to smelt aluminum blocks, chemical corrosion intensifies and the furnace age decreases.
WeChat
Σαρώστε τον κωδικό QR με το wechat