Refractory bricks are a kind of refractory product with certain size and shape and can withstand 1580℃ to 3000℃. They have a wide range of applications and can be used in industrial kilns such as iron-making blast furnaces, coke ovens, hot blast furnaces, molten iron tanks, torpedo tanks, steelmaking ladles, tundishes, converters, glass kilns, cement rotary kilns, και τα λοιπά. Refractory bricks are used as kiln linings with good effect and long service life. They are the preferred refractory products for many industrial kilns.
Refractory brick mold
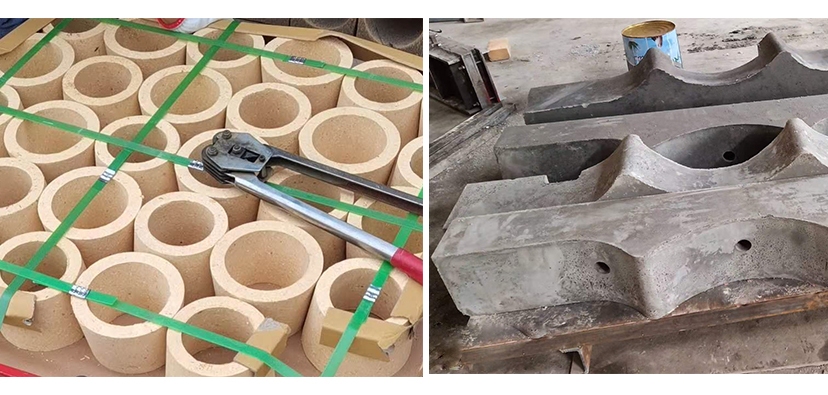
A refractory brick mold is a tool used in the production of refractory bricks. The refractory raw materials used in the production of refractory bricks are placed in the mold, and the refractory bricks are formed by pressurizing the press. The refractory brick mold can be customized according to customer needs, especially special-shaped sizes. The mold can make the refractory brick blanks better shaped and more accurate in size, ensuring the size of the refractory bricks after firing and the integrity of the refractory bricks during masonry use.
The importance of molds is self-evident. Molds have an important impact on the quality of refractory brick blanks. If there is a problem with the refractory brick production mold, the quality of the pressed refractory brick blanks may be unstable, affecting the use of refractory bricks.
Existing refractory brick-forming molds often use static pressure for compaction when making refractory bricks. During the compaction process, refractory materials with poor fluidity they cannot flow to the corners of the mold, resulting in the corners of the pressed refractory bricks being unsolid, affecting the quality of the refractory bricks. Εξάλλου, when bricks need to be produced by pressing, if a machine is used for automated production, a refractory brick ejection device or a brick ejector is often set under the mold; if specially shaped bricks are laid manually, the adjustment structure disclosed in ZL201320536438.2 is often used. The advantage of manual laying is that the defective rate can be reduced, but the disadvantage is low efficiency. Although the use of automated machinery for production can improve efficiency, the power consumption is large.
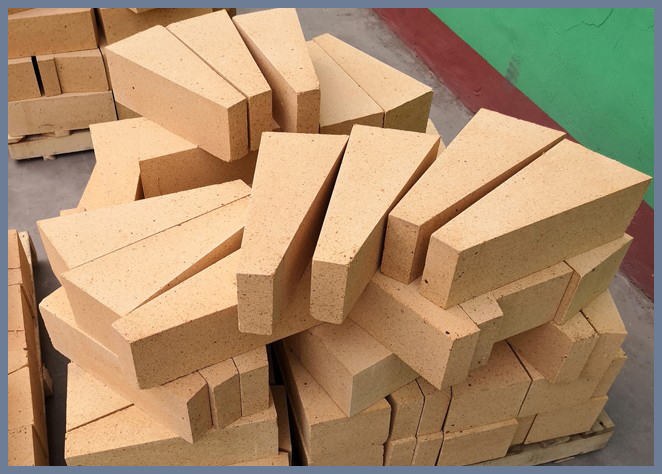
WeChat
Σαρώστε τον κωδικό QR με το wechat