How to choose refractory castable under different circumstances? First of all, the selection should consider the kiln environment, use location, use temperature, and corrosion properties.
Types of refractory castables
Refractory castables include acidic, alkaline, and neutral castables; they are divided into heavy castables and light castables according to density; they are divided into aluminum silicate, magnesia, magnesium chromium, corundum castables, and silicon-based materials.
How to choose castables?
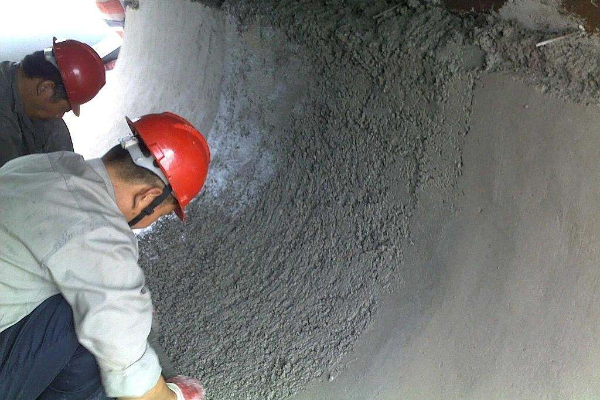
To choose the appropriate refractory castable, you must consider the location, temperature, and pouring thickness. Considering these aspects, this can reduce costs and achieve reasonable use effects.
If it is the working layer, heavy refractory castables with high-temperature resistance should be selected. If the erosion is acidic, castables that are resistant to acid erosion should be selected. If the erosion is alkaline, castables that are resistant to alkaline erosion should be selected. If the parts in contact with molten slag should use castables with strong resistance to slag erosion; parts with severe material impact should use high-strength and wear-resistant castables; if parts with frequent temperature changes should use castables with good thermal shock resistance.
Lightweight refractory castables should be used as the castables for the insulation layer. The main considerations are load-bearing structure, lowering the temperature of the furnace shell, and reducing heat loss. Then choose thermal insulation castables with different volume densities. Generally, 1.2 volume density is used. For thermal insulation castables, if the user has weight requirements, they should choose thermal insulation castables with a body density of 0.6-1.0.
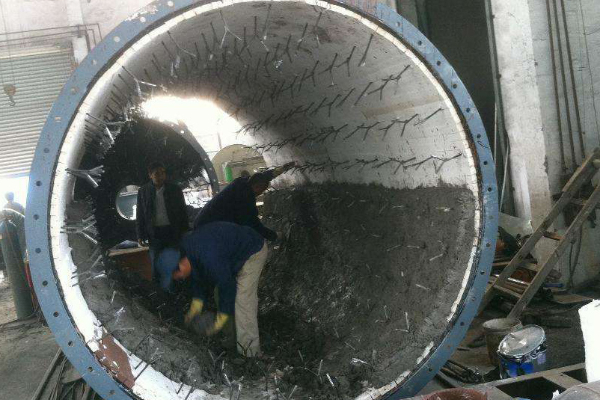
No matter what kind of refractory castable is chosen, there is an economic cost. Different grades of castables are used depending on the temperature. The castables used at different temperatures are also different. Generally speaking, clay castables are used below 1200°C, high-aluminum castables are used between 1300°C and 1400°C, and corundum castables are used if the temperature exceeds 1450°C; this is both economical and practical.
The construction thickness of refractory castables is different. If it is less than 50mm thick, you must use smearing material or spray paint. If it is for repair or furnace top use, choose plastic. If the thickness of the castable is greater than 100mm, large particle aggregates are needed to improve the wear resistance of the castable. Generally, the best thickness of the castable is 200mm.
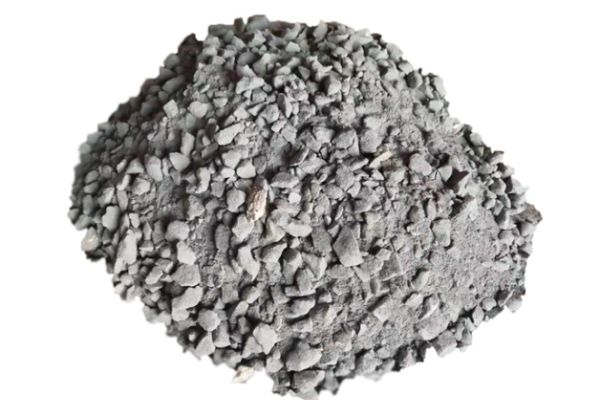
The usage quantity of refractory castables should be calculated based on the volume because the castables are stored for 6-9 months. If they cannot be used and are stored for too long, there will be agglomeration or the binding agent will fail due to condensation, which will affect the service life of the castables.
WeChat
Scan the QR Code with wechat